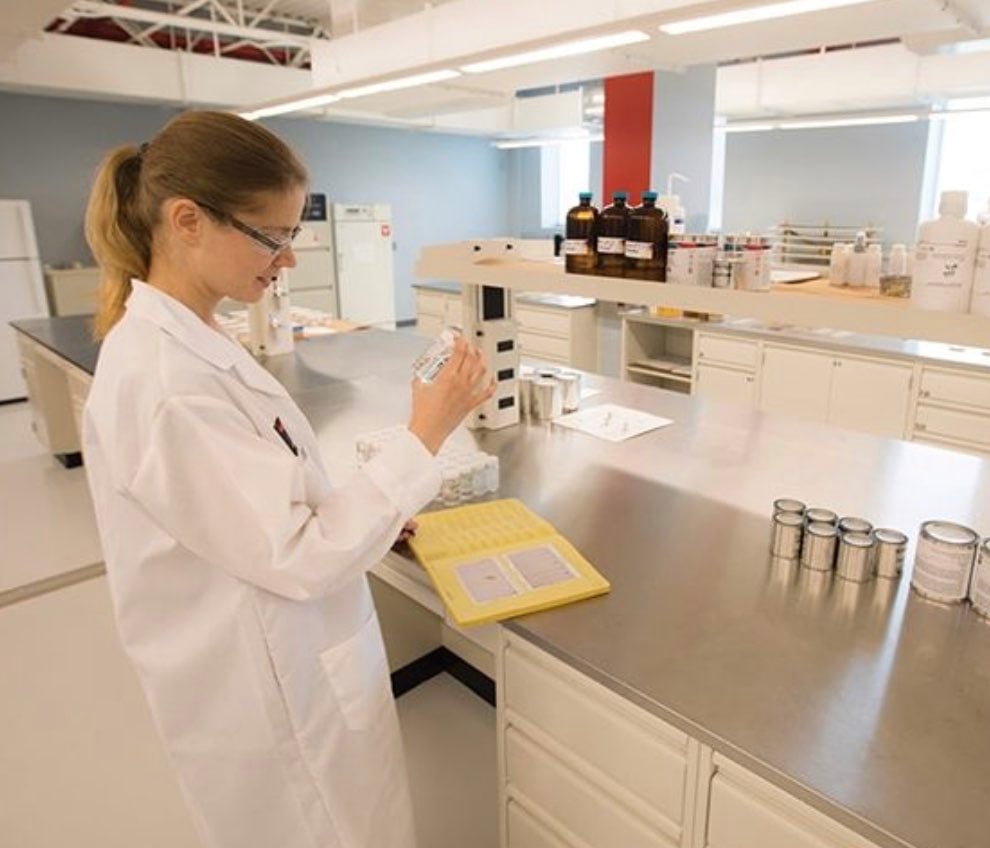
Here's a cheat sheet for ASTM coating testing standards
Essential ASTM coating testing standards for thickness, adhesion, corrosion resistance, impact, hardness, chemical resistance, weathering, and gloss. Ensure your coatings meet industry requirements.
- High Performance Coatings
This blog contains ASTM Standards to compare coating performance of different manufacturers.
Cheat Sheet for ASTM Coating Testing Standards
1. Coating Thickness
D1186 – Standard Test Method for Nondestructive Measurement of Dry Film Thickness of Coatings Using Magnetic Method
This standard outlines a procedure for accurately measuring the thickness of dry film coatings applied to ferrous substrates. The method employs a magnetic probe, which is a non-invasive tool that allows for precise thickness measurements without damaging the coating or the substrate. This is particularly useful in quality control and inspection processes where maintaining the integrity of the coating is crucial. The magnetic method is favored for its efficiency and reliability in providing consistent results across various applications.
ASTM D1400 – Standard Test Method for Inspection of Coatings in Place
This method involves the use of a micrometer or a similar precision device to measure the thickness of coatings in a non-destructive manner. By employing this technique, inspectors can assess the coating's thickness while it remains in place, ensuring that the coating meets specified requirements without the need for removal or alteration. This approach is essential for maintaining the functionality and appearance of the coating, especially in applications where the coating's protective properties are critical.
2. Adhesion Testing
ASTM D3359 – Standard Test Methods for Measuring Adhesion by Tape Test
This method is widely utilized for evaluating the adhesion strength of coatings applied to various substrates. The procedure involves making a cross-hatch pattern on the coating surface, followed by the application of a pressure-sensitive adhesive tape. The tape is then rapidly removed, and the amount of coating that detaches is assessed. This test is particularly useful for quality control in manufacturing processes, as it provides a quick and effective means of determining whether a coating will adhere properly under different conditions. It is applicable to a wide range of coatings, including paints and varnishes, and is often used in industries such as automotive, aerospace, and construction to ensure the durability and longevity of coated surfaces.
ASTM D4541 – Standard Test Method for Pull-Off Strength of Coatings Using Portable Adhesion Testers
This test method is designed to measure the force required to detach a coating from its substrate using a hydraulic pull-off tester. The process involves attaching a loading fixture, or dolly, to the coating surface with an adhesive. Once the adhesive has cured, the tester applies a perpendicular force until the coating detaches. The force at which the coating fails is recorded as the pull-off strength. This method is highly regarded for its precision and is often employed in situations where a quantitative measure of adhesion is necessary. It is suitable for a variety of coatings, including those used in harsh environments, and is critical for ensuring that coatings will perform as expected in service.
ASTM B571 – Standard Practice for Adhesion Testing of Metallic Coatings
This standard practice is specifically tailored for assessing the adhesion of metallic coatings, such as galvanizing, electroplating, and other metal finishes. The practice includes several test methods, such as bend tests, burnishing tests, and thermal shock tests, each designed to evaluate the adhesion characteristics of metallic coatings under different conditions. These tests are essential for industries that rely on metallic coatings for corrosion protection, aesthetic appeal, or functional performance. By determining the adhesion quality, manufacturers can ensure that the coatings will not peel or flake off during use, thereby maintaining the integrity and effectiveness of the coated product.
3. Corrosion Resistance
ASTM B117 – Standard Practice for Operating Salt Spray (Fog) Apparatus
This standard is a widely recognized method for testing the corrosion resistance of coatings by subjecting them to a controlled salt fog environment. The test involves placing coated specimens in a chamber where they are exposed to a fine mist of saltwater solution, simulating harsh marine or coastal conditions. This exposure helps to accelerate the corrosion process, allowing for the assessment of how well a coating can protect the underlying material over time. The results of this test are crucial for industries such as automotive, marine, and construction, where coatings are expected to withstand corrosive elements and maintain their protective properties.
ASTM D1654 – Standard Test Method for Evaluation of Coated Specimens in Corrosive Environments
This method is employed to evaluate the performance and durability of coatings when exposed to corrosive environments. The test involves subjecting painted or coated specimens to conditions that mimic real-world corrosive scenarios, such as salt spray, humidity, or chemical exposure. After exposure, the integrity of the coating is assessed by examining factors like rust creepage, blistering, and adhesion loss. This evaluation is essential for determining the long-term effectiveness of coatings in protecting substrates from corrosion, ensuring that they meet industry standards and application-specific requirements.
ASTM D714 – Standard Test Method for Evaluating Degree of Blistering of Paints
This standard provides a systematic approach to evaluate the size, density, and distribution of blisters that may form on a coating surface. Blistering is a common defect that can occur when coatings are exposed to moisture, heat, or chemical agents, leading to the formation of raised areas on the surface. The test involves visually inspecting the coated surface and categorizing the blisters based on their size and frequency. Understanding the degree of blistering is vital for quality control and for identifying potential weaknesses in a coating's formulation or application process, which can affect its protective performance and aesthetic appearance.
4. Impact Resistance
ASTM D2794 – Standard Test Method for Resistance of Organic Coatings to the Effects of Rapid Deformation (Impact) is a comprehensive procedure designed to evaluate how well an organic coating can withstand sudden physical impacts or shocks. This test is crucial for determining the durability and resilience of coatings when subjected to forces that could cause deformation. The method involves dropping a specified weight from a predetermined height onto the coated surface, simulating real-world impacts that the coating might encounter during its service life. The test assesses the coating's ability to absorb and distribute the energy from the impact without cracking, chipping, or delaminating from the substrate. This evaluation is essential for industries where coatings are expected to endure mechanical stresses, such as in automotive, construction, and industrial applications, ensuring that the coatings maintain their protective and aesthetic properties even under challenging conditions.
5. Hardness Testing
ASTM D3363 – Standard Test Method for Film Hardness by Pencil Test
This method offers a straightforward and accessible approach to evaluating the hardness of coatings by utilizing pencils of varying hardness levels, as defined by the H scale. The test involves systematically using pencils with increasing hardness to scratch the coating surface until the pencil that does not leave a mark is identified. This process helps determine the coating's resistance to surface damage and wear, providing valuable insights into its durability and suitability for various applications. The pencil test is particularly favored for its simplicity and cost-effectiveness, making it a popular choice in both laboratory and field settings for quick assessments of coating hardness.
ASTM D4366 – Standard Test Method for Instrumented Indentation Hardness of Coatings
This method provides a more sophisticated and precise evaluation of coating hardness by measuring the depth of an indentation made by a probe. The test involves applying a controlled force to a probe, which then indents the coating surface. The depth of the indentation is measured to determine the coating's hardness, offering a quantitative assessment of its resistance to deformation. This method is highly regarded for its accuracy and is often used in research and development settings where detailed hardness data is required. It is particularly useful for coatings that are expected to endure significant mechanical stress, ensuring that they maintain their protective and functional properties under demanding conditions.
6. Chemical Resistance
ASTM D1308 – Standard Test Method for Effect of Household Chemicals on Organic Finishes
This standard test method is designed to evaluate the resistance of coatings to common household chemicals, which can include a variety of substances such as cleaners, detergents, and solvents. The test involves applying these chemicals to the surface of the coating and observing any changes or damage that may occur. This assessment is crucial for determining the durability and longevity of coatings in environments where they are likely to come into contact with such chemicals. By understanding how coatings react to these substances, manufacturers can ensure that their products maintain their appearance and protective qualities in everyday use, making this test particularly relevant for coatings used in residential and commercial settings.
ASTM D5402 – Standard Test Method for Evaluating the Resistance of Coatings Using a Chemical Spot Test
This method provides a systematic approach to assess a coating's resistance to chemical penetration by applying various chemical agents directly onto the coating surface and observing the reaction. The test involves placing small drops of different chemicals on the coating and monitoring any changes, such as discoloration, swelling, or degradation, over a specified period. This evaluation helps determine the coating's ability to withstand exposure to potentially harmful chemicals, which is essential for applications where chemical resistance is a critical factor. The results of this test can guide the selection of coatings for environments where they may be exposed to industrial chemicals, ensuring that the coatings provide adequate protection and maintain their integrity under challenging conditions.
7. Weathering Resistance
ASTM G154 – Standard Practice for Operating Fluorescent Light Apparatus for Exposure of Nonmetallic Materials
This standard practice is designed to simulate accelerated weathering conditions for coatings by using a fluorescent light apparatus. The test aims to replicate the effects of natural environmental factors such as sunlight, temperature fluctuations, and humidity on nonmetallic materials. By exposing coatings to these controlled conditions, the test provides valuable insights into how they will perform over time when subjected to outdoor elements. This method is particularly useful for predicting the longevity and durability of coatings, helping manufacturers and researchers assess their resistance to fading, cracking, or other forms of degradation that can occur due to prolonged exposure to sunlight and varying weather conditions. The results from this test are crucial for industries that require coatings to maintain their protective and aesthetic properties in outdoor settings, such as automotive, construction, and marine applications.
ASTM G26 – Standard Practice for Operating Light and Water Exposure Apparatus for Exposure of Nonmetallic Materials
This standard practice is similar to ASTM G154 but incorporates additional exposure to water cycles, providing a more comprehensive assessment of a coating's weathering resistance. The test involves using a specialized apparatus that subjects nonmetallic materials to cycles of light and water, simulating the combined effects of sunlight and moisture that occur in natural environments. This method is essential for evaluating how coatings withstand not only the drying and heating effects of sunlight but also the potential damage caused by rain, dew, or humidity. By understanding how coatings react to these combined stressors, manufacturers can ensure that their products are capable of enduring harsh weather conditions without losing their protective or aesthetic qualities. This test is particularly relevant for applications where coatings are expected to face frequent exposure to both sunlight and water, such as in outdoor furniture, building exteriors, and marine equipment.
8. Gloss and Appearance
ASTM D523 – Standard Test Method for Specular Gloss
This standard test method is designed to measure the gloss, or shine, of coatings by evaluating how light reflects off their surfaces at different angles of incidence. The gloss level of a coating is an important aesthetic and functional property, as it can affect the appearance and perceived quality of the coated surface. The test involves using a gloss meter, an instrument that directs a beam of light at a specific angle onto the coating surface and measures the amount of light that is reflected back. By assessing the gloss at various angles, such as 20, 60, and 85 degrees, this method provides a comprehensive understanding of the coating's reflective properties. This information is crucial for industries where the visual appeal of a product is paramount, such as in automotive finishes, consumer electronics, and decorative coatings, ensuring that the final product meets the desired specifications for gloss and appearance.
ASTM D2244 – Standard Practice for Calculation of Color Tolerances and Color Difference from Instrumentally Measured Color Coordinates
This standard practice provides a systematic approach for calculating color differences in coatings, which is essential for maintaining color consistency and quality control in manufacturing processes. The method involves using a colorimeter, an instrument that measures the color of a coating by capturing its color coordinates in a defined color space. By comparing these coordinates to a reference or standard color, the practice allows for the calculation of color tolerances and differences, ensuring that the coating meets the specified color requirements. This is particularly important in industries where precise color matching is critical, such as in automotive paint, textiles, and consumer goods, where even slight variations in color can impact the product's marketability and customer satisfaction. The results from this practice help manufacturers maintain uniformity in their products, ensuring that each batch of coating adheres to the established color standards.
9. Flexibility and Bend Testing
ASTM D522 – Standard Test Method for Mandrel Bend Test of Attached Organic Coatings
This standard test method is designed to evaluate the flexibility and durability of organic coatings when applied to metal substrates. The test involves bending the coated metal around a cylindrical mandrel of a specified diameter to determine the coating's ability to withstand deformation without cracking or detaching from the substrate. By assessing the coating's performance under these conditions, the test provides valuable insights into its flexibility and adhesion properties, which are critical for applications where the coated material may be subjected to bending or flexing during use. This method is particularly important for industries such as automotive, aerospace, and construction, where coatings must maintain their protective and aesthetic qualities even when the underlying material is bent or shaped. The results of this test help manufacturers ensure that their coatings can endure mechanical stresses without compromising their integrity or functionality.
10. Film Formation
ASTM D1005 – Standard Test Method for Measurement of Dry Film Thickness of Coatings Using Micrometers
This standard outlines a precise method for measuring the thickness of a dry film coating using a micrometer, a highly accurate instrument that gauges the distance between its two surfaces. The process involves placing the micrometer over the coating and gently closing it until it makes contact with the surface, ensuring that the measurement is taken without compressing the film. This method is essential for quality control in various industries, as it helps verify that the coating has been applied to the correct thickness, which is crucial for its protective and aesthetic functions. Accurate thickness measurements ensure that the coating will perform as intended, providing adequate protection against environmental factors and wear.
ASTM D2697 – Standard Test Method for Volatile Content of Coatings
This standard provides a detailed procedure for determining the percentage of volatile materials present in a coating. The test involves weighing a sample of the coating before and after it is subjected to a controlled heating process, which evaporates the volatile components. By calculating the weight loss, the volatile content is determined, offering insights into the composition and drying characteristics of the coating. Understanding the volatile content is vital for manufacturers, as it affects the application properties, drying time, and environmental impact of the coating. This information is particularly important for ensuring compliance with environmental regulations and for optimizing the formulation to achieve the desired performance and finish.
11. Abrasion Resistance
ASTM D4060 – Standard Test Method for Abrasion Resistance of Organic Coatings
Taber Abraser is a comprehensive procedure designed to evaluate the durability of organic coatings when subjected to abrasive forces. This test method involves using a Taber Abraser, a specialized instrument equipped with a rotating abrasive wheel that applies consistent friction to the coating surface. The process begins by securely mounting the coated specimen onto the Taber Abraser, ensuring that it is properly aligned for accurate testing. As the abrasive wheel rotates, it systematically wears down the coating, simulating the effects of everyday wear and tear that the coating might encounter in real-world applications. The degree of abrasion resistance is determined by measuring the weight loss of the coating after a specified number of cycles, providing a quantitative assessment of its ability to withstand frictional forces. This test is crucial for industries where coatings are expected to endure high levels of abrasion, such as in flooring, automotive, and industrial equipment, ensuring that the coatings maintain their protective and aesthetic properties over time. By understanding the abrasion resistance of a coating, manufacturers can make informed decisions about its suitability for various applications, ultimately enhancing the longevity and performance of their products.
12. Thermal Resistance
ASTM D2485 – Standard Test Method for Heat Resistance of Coatings
A comprehensive procedure designed to evaluate a coating's ability to endure high temperatures over extended periods without experiencing any form of degradation. This test is crucial for determining the thermal stability and performance of coatings when exposed to elevated temperatures, which can be a common requirement in various industrial applications. The method involves subjecting coated specimens to controlled heat conditions, often in a specialized oven or furnace, to simulate the thermal stresses they might encounter in real-world environments. Throughout the testing process, the coating is monitored for any signs of physical or chemical changes, such as discoloration, blistering, cracking, or loss of adhesion. By assessing these factors, the test provides valuable insights into the coating's durability and effectiveness in maintaining its protective and aesthetic properties under thermal stress. This information is essential for industries such as automotive, aerospace, and manufacturing, where coatings are expected to perform reliably in high-temperature settings, ensuring that they continue to protect the underlying materials and maintain their intended appearance and function.
13. Solvent Resistance
ASTM D4752 – Standard Test Method for Solvent Resistance of Organic Coatings by Solvent Rubs
A detailed procedure designed to evaluate the ability of organic coatings to withstand exposure to various solvents without sustaining damage. This test method involves applying a specific solvent to the coating surface using a cloth or pad, followed by a series of controlled rubbing actions. The purpose of this process is to simulate the potential effects of solvent exposure that the coating might encounter in real-world applications, such as cleaning or accidental spills. By observing any changes in the coating, such as softening, swelling, or removal, the test provides valuable insights into the coating's durability and chemical resistance. This information is crucial for industries where coatings are expected to maintain their integrity and appearance despite frequent contact with solvents, ensuring that they continue to protect and enhance the underlying materials effectively.
LET OUR KNOWLEDGE AND EXPERTISE HELP ENSURE YOUR NEXT PROJECT IS SUCCESSFUL
Additional Notes:
- Test Equipment: Many of these tests require specialized equipment, such as an impact tester, gloss meter, or salt spray chamber.
- Reporting: Most tests have specific reporting formats, often requiring a detailed description of the test conditions and the results.
- Test Specimens: The size, shape, and preparation of test specimens must follow specific guidelines to ensure repeatability.
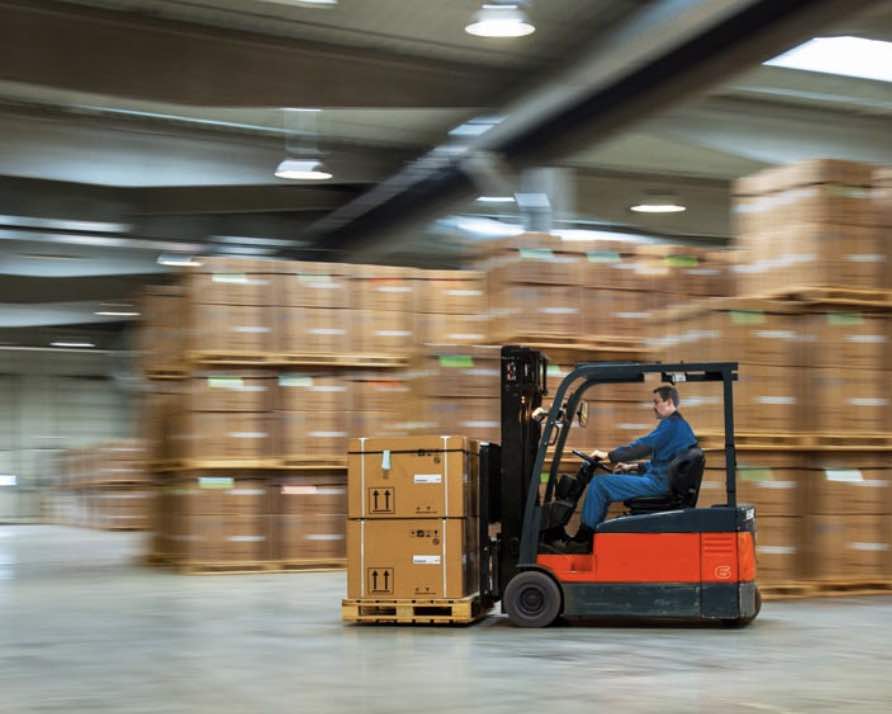
What is ASTM D4060 and Why is Abrasion Resistance...
Why is testing the abrasion resistance of...
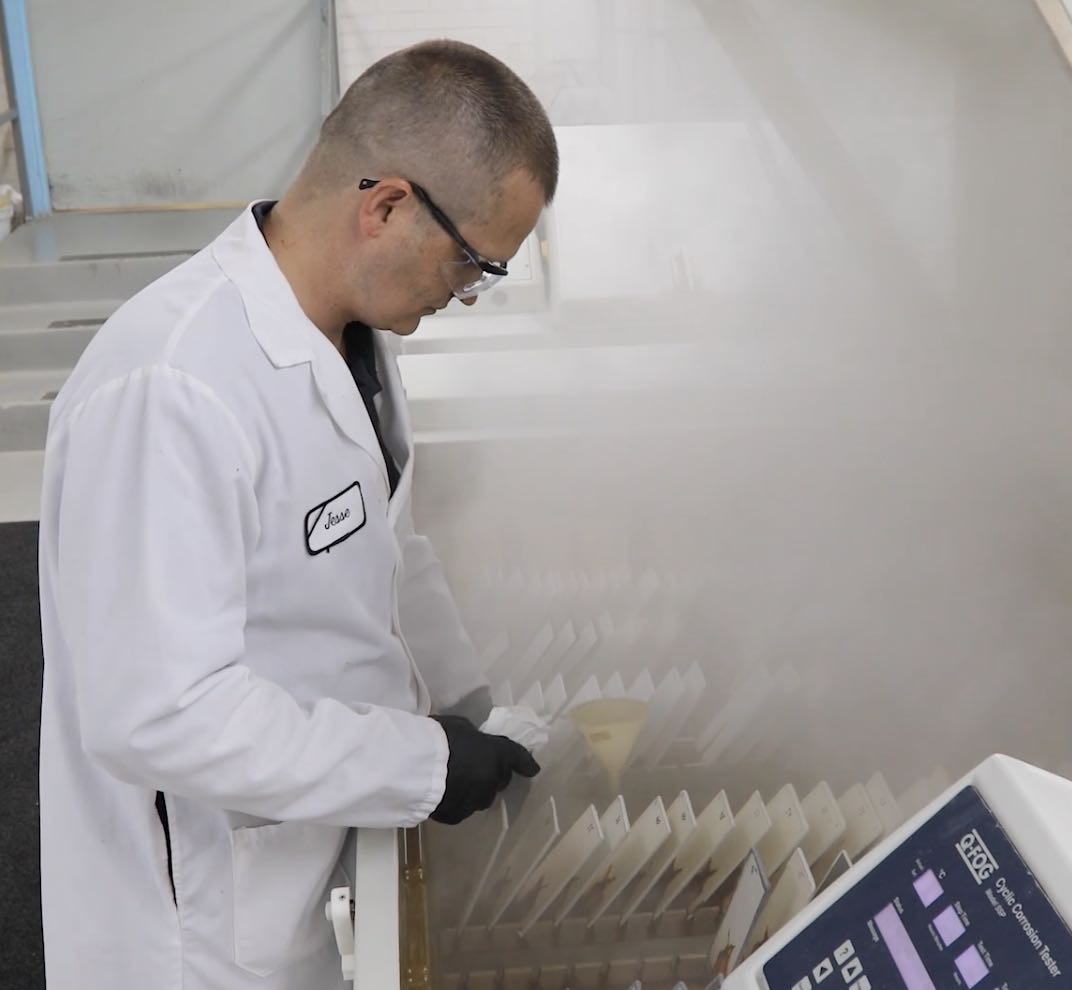
What is ASTM D4585 (Accelerated Weathering)...
ASTM D4585 is a standard practice developed by...
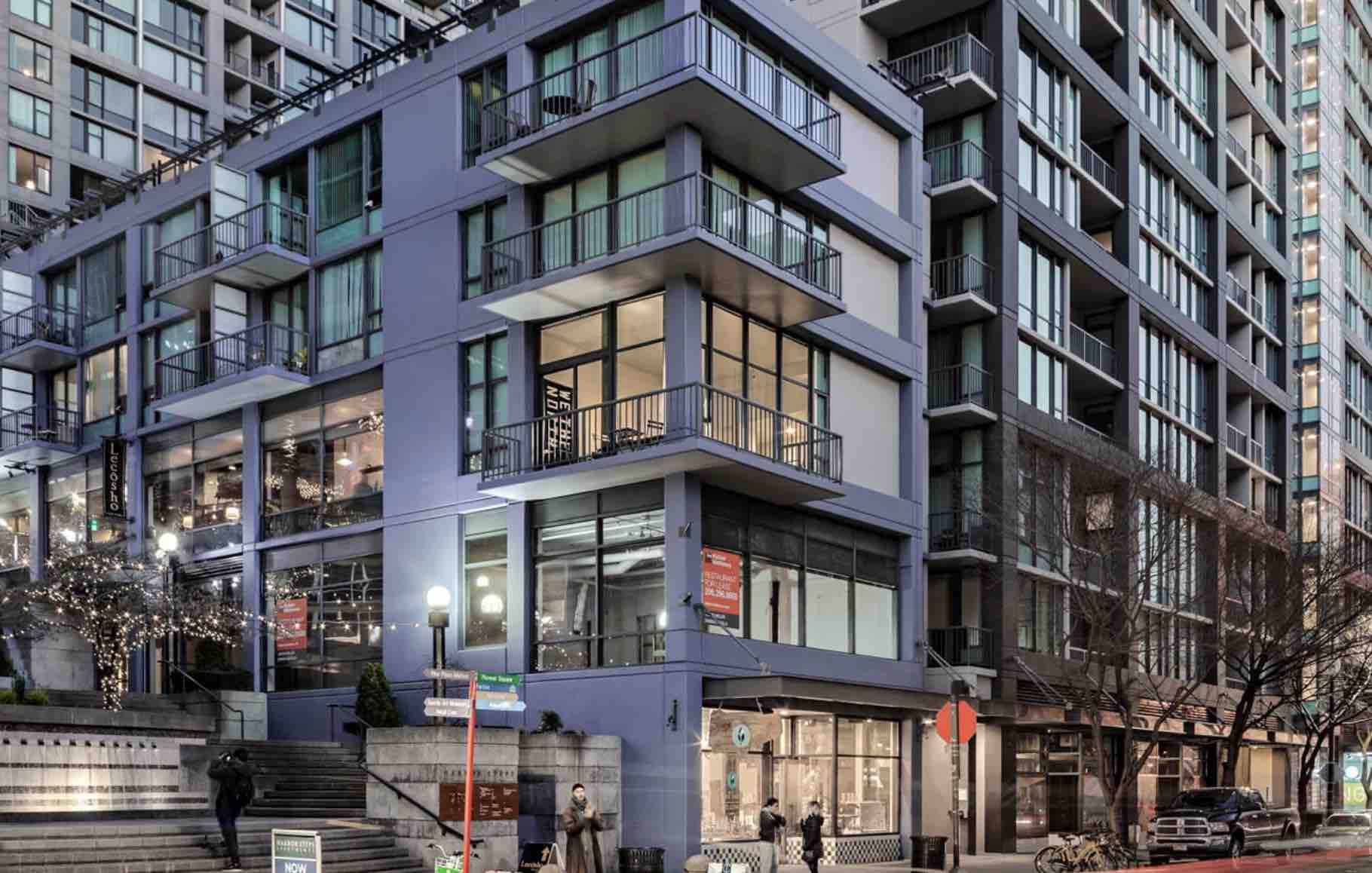
The Difference Between Elastomeric Coatings Can...
The performance differences between elastomeric...