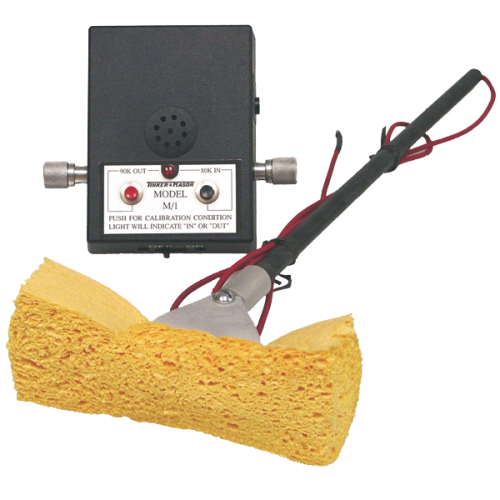
Low and High Voltage Holiday Testing is Important
Learn why low and high voltage holiday testing is crucial for ensuring the effectiveness of protective coatings. Discover the different types of holiday testing and their applications in this comprehensive guide.
- High Performance Coatings
Holiday Testing
A holiday test in designed to find pinholes within an immersion exposure lining/coating system so that water cannot get behind the liner, leading to a coating failure. So it is standard practice to holiday test as part of a quality control program after an immersion coating system is completed. This testing is outlined in detail by AMPP International Recommended Practice SP0188-99 Discontinuity (Holiday) Testing of New Protective Coatings on Conductive Substrates:
AMPP SP0188-2006 (for purchase)
There are two types of holiday testing. The first is a low voltage(wet sponge) holiday test that is intended for linings applied at less then 20 dry mils on metallic substrates. The second is a high voltage(spark) holiday test that is used for a lining system applied over 20 dry mils on metallic or concrete substrates. Systems applied above 20 dry mils are holiday tested at a value of 100 volts DC per mil.
Tinker&Rasor Low Voltage Holiday Detector Defelsko PosiTest HHD High Voltage Holiday Dectector
Tnemec’s technical bulletin 03-42 “Discontinuity (Holiday)Testing of New Protective Coatings on Conductive Substrates” best details these two testing options.
LOW VOLTAGE “WET SPONGE” HOLIDAY DETECTOR
A low voltage “wet sponge” holiday detector, (5 to 90 volts DC) equipped with an audible signal device, can be used to electrically inspect thin film protective coatings. This is accomplished by using an exploratory electrode consisting of an open cell cellulose sponge saturated with potable water to push the liquid film over the coated surface. When a discontinuity is encountered, DC current will flow through the liquid to the conductive substrate thus completing the circuit and causing an audible signal to be emitted. Despite being classified as “low voltage”,
the low voltage wet sponge tester is a sensitivity device that is independent of voltage requirements. In other words, the operating voltage has little importance other than part of the particular electronic design. A number of commercially available, industry-accepted, “wet sponge” type instruments are on the market. The following electronic principle describes two types of devices generally used:
- Lightweight, self-contained, portable devices based on the electrical principle of an electromagnetic sensitive relay or solid-state electronic relay circuit that energizes an audible or visual indicator when a coating discontinuity is detected. Examples of instruments working on this principle are the Tinker & Rasor M1 Low-Voltage Holiday Detector and Elcometer Model 269 Pinhole Detector.
- Lightweight, self-contained, portable devices based on the principle of an electronic relaxation oscillator circuit that reacts significantly to the abrupt drop in electrical resistance between the high dielectric value of the coating film and the conductive substrate at the point of coating film discontinuity. This results in a rise in oscillator frequency as well as in the audible signal from the device. An example of an instrument working on this principle is the K-D Bird Dog Low-Voltage Holiday Detector.
Several prerequisites must be met prior to low voltage holiday testing. First, the protective coating surface must be dry before conducting the electrical inspection. Secondly, if the coating surface is exposed to an environment where electrolytes such as salt particles may have formed, it should be cleaned with fresh water and allowed to dry completely. Sufficient curing of the coating shall be allowed prior to conducting a low-voltage holiday test. The length of time required for testing is generally equivalent to the “Place to Service” time listed on the Product Data Sheet. Solvents retained in the coating film may produce erroneous results.
Wetting agents help break down surface tensions of the liquid allowing faster and increased penetration of the water into discontinuities, resulting in superior testing without adversely affecting electrical inspection. However, when a holiday test is conducted between coats of a multicoat system, a wetting agent should not be used. A wetting agent such as that used in photographic film development is an excellent product for this purpose and is readily available in leading camera stores world wide. The recommended dilution amount is 1 fluid ounce (.0296 liters) wetting agent to 1 U.S gallon (3.7854 liters) potable water. The sponge shall be saturated sufficiently to barely avoid dripping of the solution while moved over the coating. Attach the ground wire from the low-voltage instrument ground terminal to the uncoated conductive substrate and ensure positive electrical contact.
AMPP SP0188 states that during testing the sponge shall be moved over the surface of the coating at a moderate rate approximately 1 ft/s, using a double pass over each area. Apply sufficient pressure to maintain a wet surface. If a discontinuity is detected, the sponge should be turned on end to determine the exact location. Low voltage (wet sponge) detectors shall not be used for the electrical testing of protective coating having a dry film thickness in excess of 20 mils due to the relative inaccuracy and lack of sensitivity for holiday detection. The low-voltage (wet sponge) tester shall be tested for sensitivity prior to initial use on each project and periodically thereafter during the project, in accordance with the manufacturer’s instructions. Refer to NACE SP0188 for complete testing procedures.
HIGH-VOLTAGE HOLIDAY DETECTOR
The second type of electrical holiday detector is the high-voltage (spark) detector that is used on high dielectric strength nonconductive protective coatings with dry film thickness’ ranging from several mils to 350 mils. It is recommended that a Low-volt Wet Sponge holiday detector be used when the coating thickness is less than 20 mils. It should be noted that thin film coatings may be damaged if tested with high-voltage equipment, and Tnemec does not recommend such practices.
The high-voltage holiday detector is appropriate for conductive substrates such as steel and concrete. Concrete is considered a conductive surface primarily due to the presence of hydroscopic particles of moisture. Additionally, the presence of metallic rebar embedded in the concrete allows an electrically conductive path for the holiday detector to complete the circuit.
A high-voltage holiday detector differs from low-voltage instruments because it locates areas or points on a coated conductive substrate where a great difference in electrical resistance between the exploratory electrode on the coated surface and the underlying structure exists at a set voltage. This electrical resistance is referred to as the coatings dielectric strength.
Two types of high voltage (spark) holiday detectors which apply test voltage to the surface of protective coatings exist. In the industry the most commonly used high voltage holiday detector is the “pulsating DC” type with output voltages ranging from 1,000 to 40,000 volts. The other is “continuous DC” with volt ranges from 1,000 volts to 15,000 volts. Both pulsating and continuous DC holiday detectors consist of an electrical energy source such as a battery or high voltage coil, an exploring electrode, and ground connection from the energy source to the conductive substrate. The device should be equipped with an audible alarm to signal current flow through the apparatus. Differences in the testing instruments are discussed below.
Occasionally one might encounter an AC High-Voltage Holiday Detector. These instruments rely on the 110 volt AC electrical grounding system connected to the testing specimen. Not only are these instruments extremely dangerous to operate, but they are not recommended by Tnemec Company to be used for holiday testing of our products.
Pulsating DC High-Voltage Holiday Detector
The pulsating type holiday detector is used for the electrical inspection of most protective coatings ranging from a few mils to 350 mils in thickness. The pulsating type holiday detector allows for high voltage testing with less electrical stress to protective coating than continuous DC detectors. Electrical pulses are generated between 20 and 60 Hz, with duration of each pulse between 20 microseconds and 200 microseconds.
Continuous DC Holiday Detector
The continuous DC holiday detector allows for high voltage testing where the combination of high electrical resistance is present in both the substrate and the ground return of the electrical circuit. This type is particularly useful where it is impractical to make direct electrical contact with embedded reinforcing steel in the concrete structure and the coating surface is clean and dry. It should not be used, however, where continuous moisture is present on the surface of the coating which may lead to current telegraphing. When current telegraphs through the contaminated moisture, the actual point of coating discontinuity is usually difficult to locate. Testing with continuous DC inspection voltages applies greater electrical stress to the protective coating because the voltage is applied continuously.
As with low-voltage holiday testing, sufficient curing of the coating shall be allowed prior to conducting a high-voltage holiday test. Length of time required for testing is generally equivalent to the “Place to Service” time listed on the Product Data Sheet. Solvents retained in the coating film may produce erroneous indicators of the presence of holidays, as well as a potentially explosive environment.
For detailed technical information about Holiday Testing, please contact High Performance Coating for assistance on your specific project.
References:
Tnemec (2008). Technical Bulletin No. 03-42 Discontinuity (Holiday) Testing of New Protective Coatings on Conductive Substrates
AMPP (206). AMPP Standard RP0188-99 Discontinuity (Holiday) Testing of New Protective Coatings on Conductive Substrates
Tinker & Rasor. (2021) Model: M/1 Low Voltage Holiday Detector(https://www.tinker-rasor.com/m1-stick).
Defelsko. (2021) PosiTest HHD High Voltage Holiday Detector (https://www.defelsko.com/positest-hhd).
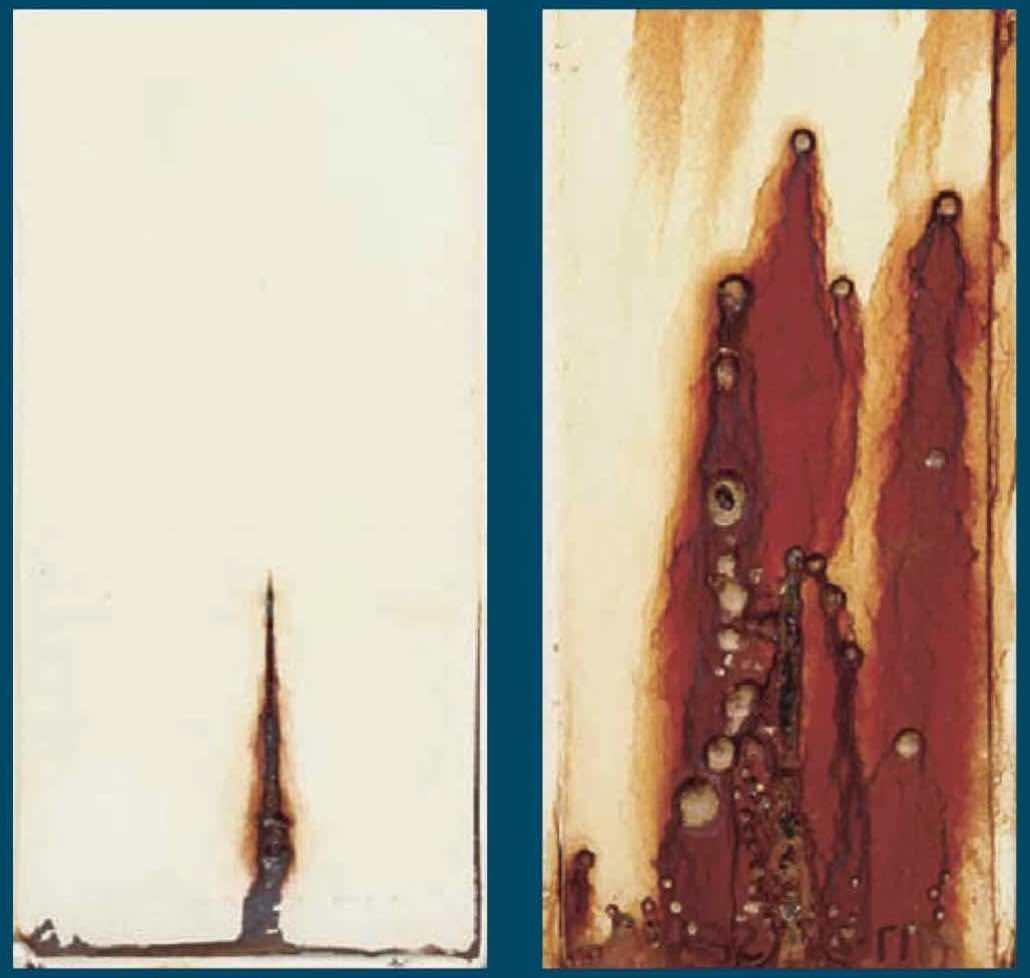
What is ASTM B117 (Salt Fog) Testing and Why is...
ASTM B117 (Salt Fog Testing) is a standard test...
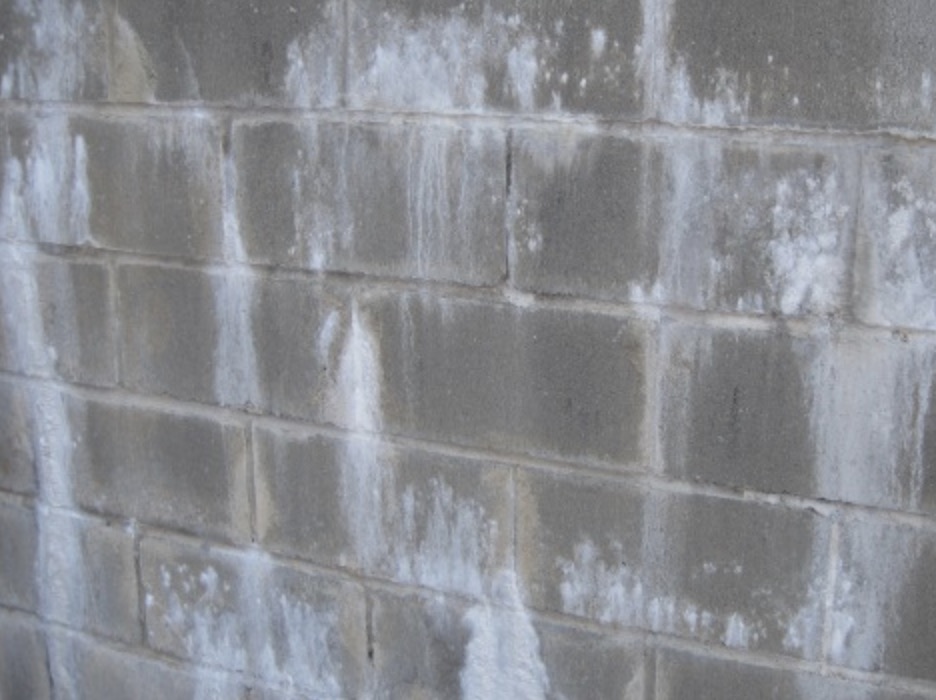
Unsightly efflorescence: What is it and how is it...
The visible collection of crystalline salt on the...