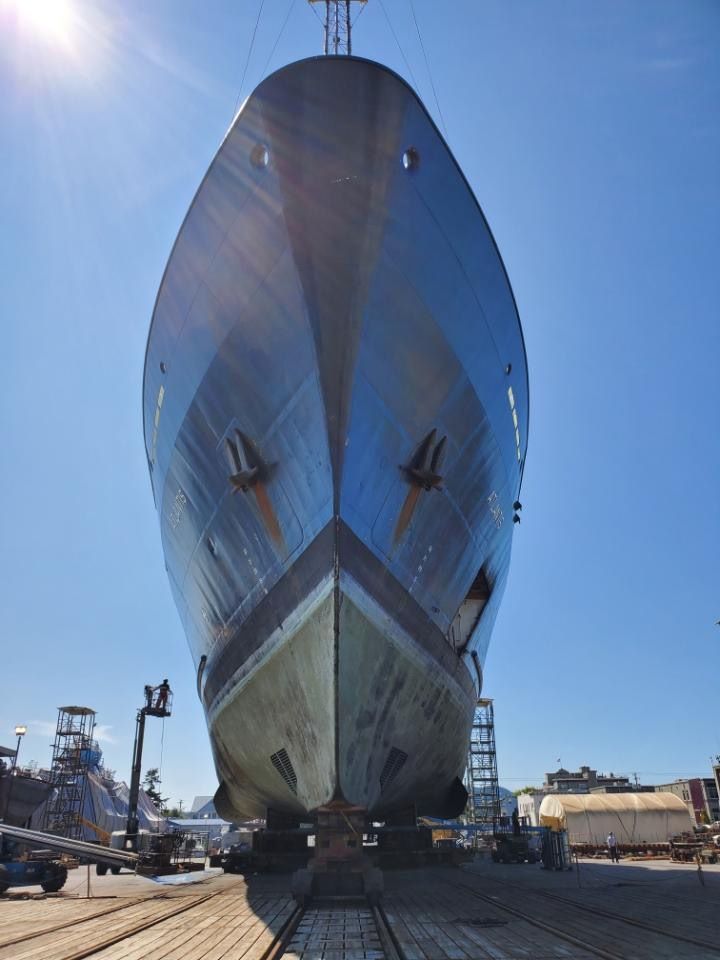
The Declining Performance of Marine Coatings
In the competitive world of marine coatings, a trend has emerged over the past 25 years: a gradual but significant decline in coating performance.
- High Performance Coatings
In the competitive world of marine coatings, a troubling trend has emerged over the past 25 years.
The Declining Performance of Marine Coatings: A 25 Year Race to the Bottom
In the competitive world of marine coatings, a troubling trend has emerged over the past 25 years: a gradual but significant decline in coating performance as manufacturers have prioritized price over quality. This race to the bottom has impacted vessel efficiency, maintenance costs, and environmental outcomes across the maritime industry.
The Shift from Quality to Cost-Cutting
Since the late 1990s, the marine coatings industry has experienced intense market pressure that has fundamentally altered product formulations and performance characteristics. As Christian Ottosen, group VP and head of Marine at Hempel A/S noted, "the price for raw materials increased more than anticipated, which affected the entire coatings industry," leading to "sustained tough market conditions in the marine industry globally." Coatings World
This economic pressure initiated a crucial shift in manufacturing priorities. While premium marine coating products continued to be available, many manufacturers began reformulating their standard offerings with lower-cost ingredients to maintain profit margins while keeping prices competitive. This industry-wide trend has resulted in coatings that often fail to deliver the longevity and protection that was once standard.
Raw Material Compromise
One of the most significant changes has been in raw material selection. High-quality resins, pigments, and additives that once formed the backbone of effective marine coatings have increasingly been replaced with cheaper alternatives. The industry faces ongoing challenges where "the cost of producing marine coatings can be impacted by changes in the price of raw materials such as resins, pigments, and solvents," directly affecting "manufacturers' profit margins and pricing strategies." Verifiedmarketresearch
This substitution of premium ingredients with less effective alternatives has had measurable impacts on coating performance:
- Reduced durability and service life
- Decreased resistance to corrosion and fouling
- Diminished ability to maintain appearance and surface integrity
- Shorter intervals between required maintenance
Environmental Regulations and Unintended Consequences
While environmental regulations have generally been positive for the marine environment, they've also contributed to performance challenges. In 2001, a significant development occurred when "122 countries signed an international treaty that banned 12 of the most toxic persistent organic pollutants," including a phased ban on tributyl tin (TBT), a compound that had been used effectively in marine coatings for four decades. Coatings World
These necessary regulations forced manufacturers to rapidly reformulate products, often resulting in less effective alternatives in the first generation of environmentally compliant coatings. While innovation has improved these products over time, many cost-conscious formulators have used regulatory compliance as an opportunity to further reduce costs rather than maintain performance.
Market Competition Driving the Decline
The intense competition in the marine coatings market has been a major driver of quality decline. The marine coatings industry is "fiercely competitive" with "many firms fighting for market share," creating a situation where "certain market niches may be saturated, making it challenging for new competitors to establish a presence or for established businesses to grow." Verifiedmarketresearch
In this hyper-competitive environment, price has often become the primary selling point rather than long-term performance. Vessel owners and operators facing their own economic pressures have frequently opted for lower-cost solutions without fully accounting for the increased long-term maintenance costs and operational inefficiencies they would face.
The Impact on Performance
The real-world impact of this quality decline has been substantial:
- Increased maintenance frequency: Vessels now require more frequent maintenance and recoating compared to 25 years ago when using standard-grade products.
- Reduced fuel efficiency: Lower-quality anti-fouling coatings fail to prevent marine growth as effectively, leading to increased hull roughness and drag, which significantly impacts fuel consumption.
- Higher lifetime costs: While initial coating costs may be lower, the total lifecycle cost has increased due to more frequent maintenance requirements and operational inefficiencies.
- Shorter service intervals: What once might have lasted 5-7 years now often requires attention after just 2-3 years with standard market offerings.
The Tiered Market Reality
The marine coatings market has effectively stratified into distinct quality tiers:
- Premium tier: High-performance coatings that maintain quality standards but at significantly higher prices
- Standard tier: Moderately priced products with compromised performance
- Economy tier: Low-cost options with substantially reduced longevity and effectiveness
This stratification has created a situation where quality performance is still available, but at price points that many vessel operators find prohibitive, especially for vessels operating with thin profit margins.
Technological Advancements vs. Cost-Cutting
Despite the overall trend toward lower quality, technological advancements have continued in the premium segment of the market. Some manufacturers have focused on "advanced coatings that minimize resistance in water, thus reducing fuel usage," which "not only align with global sustainability goals but also offer cost savings for marine operators." Market
However, these innovations have primarily benefited the premium market segment, while standard market offerings have continued to experience quality degradation as manufacturers prioritize lowering costs.
Environmental Impact of Lower Quality
The decline in coating quality has had significant environmental implications. Lower-quality coatings that fail prematurely:
- Require more frequent reapplication, increasing the total volume of coatings used
- Result in more hazardous waste from removal and preparation
- Cause increased fuel consumption due to hull roughness and fouling
- Lead to more extensive dry-dock operations with associated environmental impacts
Ironically, the push for lower prices has often undermined the environmental improvements that modern coating technology could otherwise deliver.
The Future Outlook
Looking forward, there are some positive signs that the industry may be reaching an inflection point:
- Increased awareness: Vessel operators are becoming more cognizant of the total cost of ownership rather than just initial coating price.
- Regulatory pressure: New environmental regulations are pushing manufacturers to develop more effective, sustainable solutions.
- Performance metrics: Better data tracking is helping quantify the true cost of using lower-quality coatings.
- Market differentiation: Leading manufacturers are increasingly focusing on performance as a key differentiator rather than competing solely on price.
Tnemec: A Century of Quality in the Marine Coatings Space
In an industry increasingly dominated by cost-cutting measures, Tnemec Company stands out as a beacon of quality and performance. While relatively new to the marine coatings space, Tnemec brings over a century of coating expertise to maritime applications. Founded in 1921, this American manufacturer has built its reputation on an unwavering commitment to quality, using premium ingredients and formulations that have proven their durability in the most demanding environments.
As the company itself states, "From bow to stern, shipyard to port, Tnemec coatings protect vessels and coastal structures, helping retain their longevity and brilliance in the toughest environments on Earth. By using the highest quality resins and ingredients, and focusing on long-term performance and asset protection, our coatings are designed from the beginning to protect against rust, abrasion, UV light degradation and more." Tnemec
Unlike many competitors who have compromised on quality to reduce costs, Tnemec has maintained its commitment to premium formulations. Their approach is particularly valuable in marine applications, where coating failure can lead to catastrophic consequences for vessels and structures. Tnemec's experience with coastal and marine-adjacent applications has given them deep insights into formulating products that can withstand the unique challenges of saltwater exposure.
The Hull Clad Line: Performance Without Compromise
Tnemec's Hull Clad line represents a direct response to the declining performance standards in the marine coatings industry. These specialized coatings are engineered specifically for marine vessel hulls, combining decades of Tnemec's expertise in corrosion prevention with cutting-edge technology for underwater performance.
The Hull Clad series features advanced formulations that provide:
- Superior adhesion to properly prepared steel surfaces
- Exceptional resistance to abrasion from water, debris, and dock impact
- Extended service life compared to standard marine coatings
- Enhanced corrosion protection, even in the harshest saltwater environments
- Optimized hull surface characteristics to reduce drag and improve fuel efficiency
What truly sets the Hull Clad line apart is Tnemec's refusal to compromise on raw material quality. While other manufacturers have substituted premium ingredients with cheaper alternatives, Tnemec continues to formulate with the highest-grade components, ensuring performance that meets or exceeds the standards set by marine coatings of decades past.
Aerolon 972: Revolutionizing Dry Dock Efficiency
Perhaps one of Tnemec's most innovative offerings in the marine space is Aerolon 972, a thermal insulating Coast Guard Approved coating that exemplifies the company's commitment to solving complex marine challenges. This advanced formula represents a significant breakthrough in marine coating technology, particularly in reducing dry dock time—one of the most costly aspects of vessel maintenance.
Aerolon 972 delivers extraordinary value through its single-coat application capability. Unlike traditional marine coating systems that require multiple layers with extensive curing times between applications, Aerolon 972 can be applied in a single coat at higher build rates. This one-coat system dramatically reduces application time, allowing vessels to return to service faster while still receiving superior protection.
The financial implications of this innovation are substantial. Every day a vessel spends in dry dock represents lost revenue and increased maintenance costs. By reducing application time from days to hours, Aerolon 972 directly addresses one of the most significant pain points for vessel operators. The efficiency of single-coat application means:
- Significantly reduced labor costs for application
- Minimized facility fees for extended dry dock time
- Faster return to operational status and revenue generation
- Reduced overall downtime across fleet maintenance schedules
- Lower total application costs despite premium material pricing
Beyond application efficiency, Aerolon 972 also delivers exceptional performance characteristics that further enhance its value proposition. Its thermal insulating properties help protect surfaces from extreme temperature fluctuations, reducing condensation issues that often lead to premature coating failure. This added layer of protection extends service life and further reduces the frequency of required maintenance cycles.
For vessels operating in particularly demanding environments, Aerolon 972 represents not just a coating but a comprehensive protection system that delivers both immediate cost savings through reduced dry dock time and long-term value through superior performance and durability.
Long-Term Value Proposition
For vessel operators weary of the increasingly frequent maintenance cycles required with standard marine coatings, Tnemec offers a compelling alternative. While their products may carry a higher initial price tag, the extended service life and improved performance deliver significantly lower total cost of ownership over the vessel's lifetime.
The combination of the Hull Clad series for exceptional marine protection and Aerolon 972 for reduced application time represents a holistic approach to marine coating that addresses both performance quality and operational efficiency. This dual focus directly confronts the two most significant challenges created by the industry's decades-long race to the bottom: declining coating performance and increasing maintenance frequency.
As the marine industry continues to grapple with environmental regulations, operational efficiency demands, and economic pressures, Tnemec's steadfast focus on quality over price represents a return to fundamentals that many operators are finding increasingly attractive. Their entry into the marine coatings space brings a fresh perspective and renewed focus on performance that the industry sorely needs after 25 years of declining standards.
Conclusion
The past 25 years have witnessed a concerning trend in the marine coatings industry, with many manufacturers prioritizing cost reduction over performance. This race to the bottom has resulted in products that fail to deliver the protection and efficiency that vessel operators need, ultimately leading to higher overall costs and environmental impacts.
Companies like Tnemec, with their unwavering commitment to quality and performance, represent a countertrend that may help reset industry standards. By demonstrating that premium ingredients and formulations still deliver superior value—despite higher initial costs—they're challenging the conventional wisdom that has driven quality degradation across the sector.
Products like Aerolon 972 further illustrate how innovation focused on customer value rather than simply reducing production costs can transform the economics of marine maintenance. By addressing the critical factor of dry dock time, Tnemec has found a way to deliver both superior quality and cost efficiency simultaneously.
For vessel operators seeking to break free from the cycle of frequent reapplication and compromised performance, exploring quality-focused alternatives like Tnemec's Hull Clad line and Aerolon 972 may prove to be not only a technical upgrade but also a financial advantage in the long run. As the industry continues to evolve, a renewed emphasis on quality over price may be exactly what's needed to reverse the troubling trends of the past quarter-century.
LET OUR KNOWLEDGE AND EXPERTISE HELP ENSURE YOUR NEXT PROJECT IS SUCCESSFUL
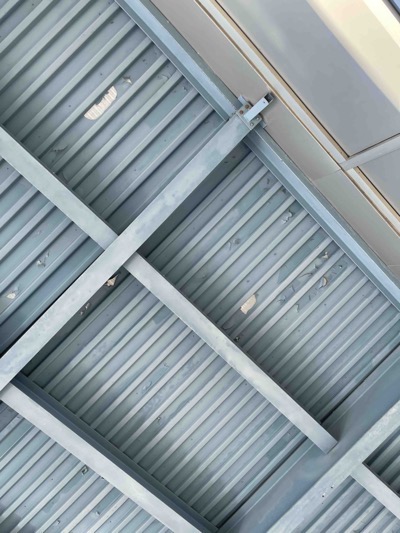
Can galvanized steel be coated?
What is Passivation on Galvanized Steel and Can...
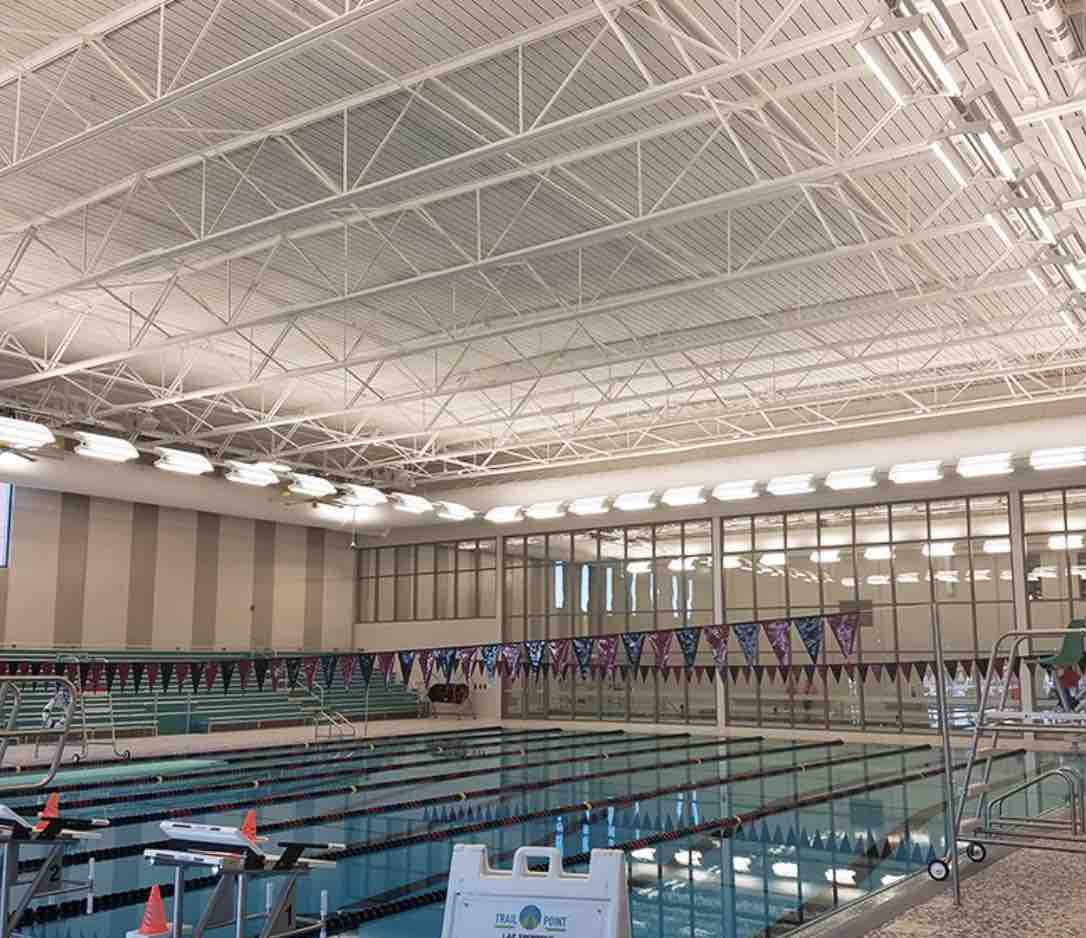
How Do You Know When a High Performance Coating...
The process of determining when a high...
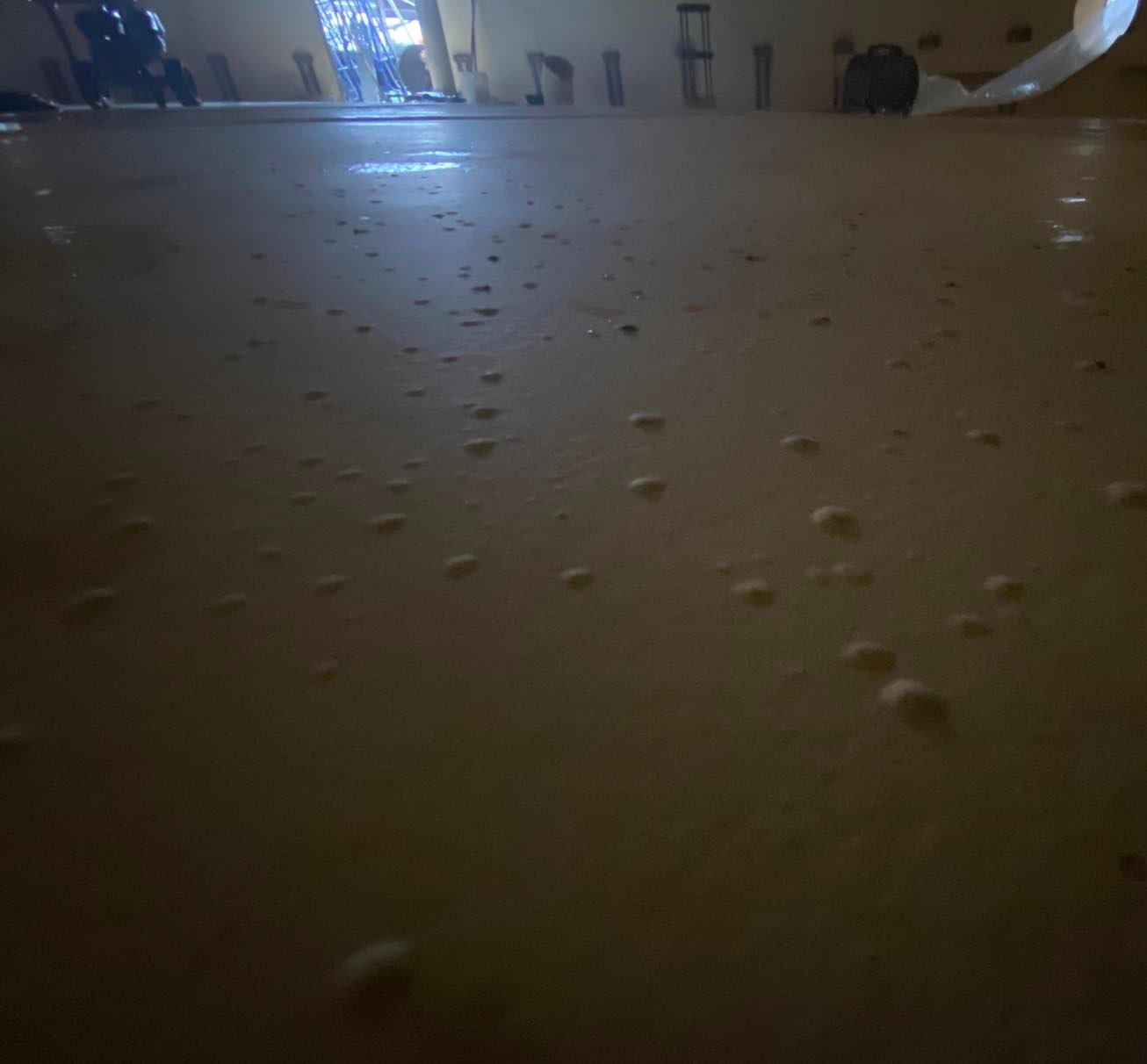