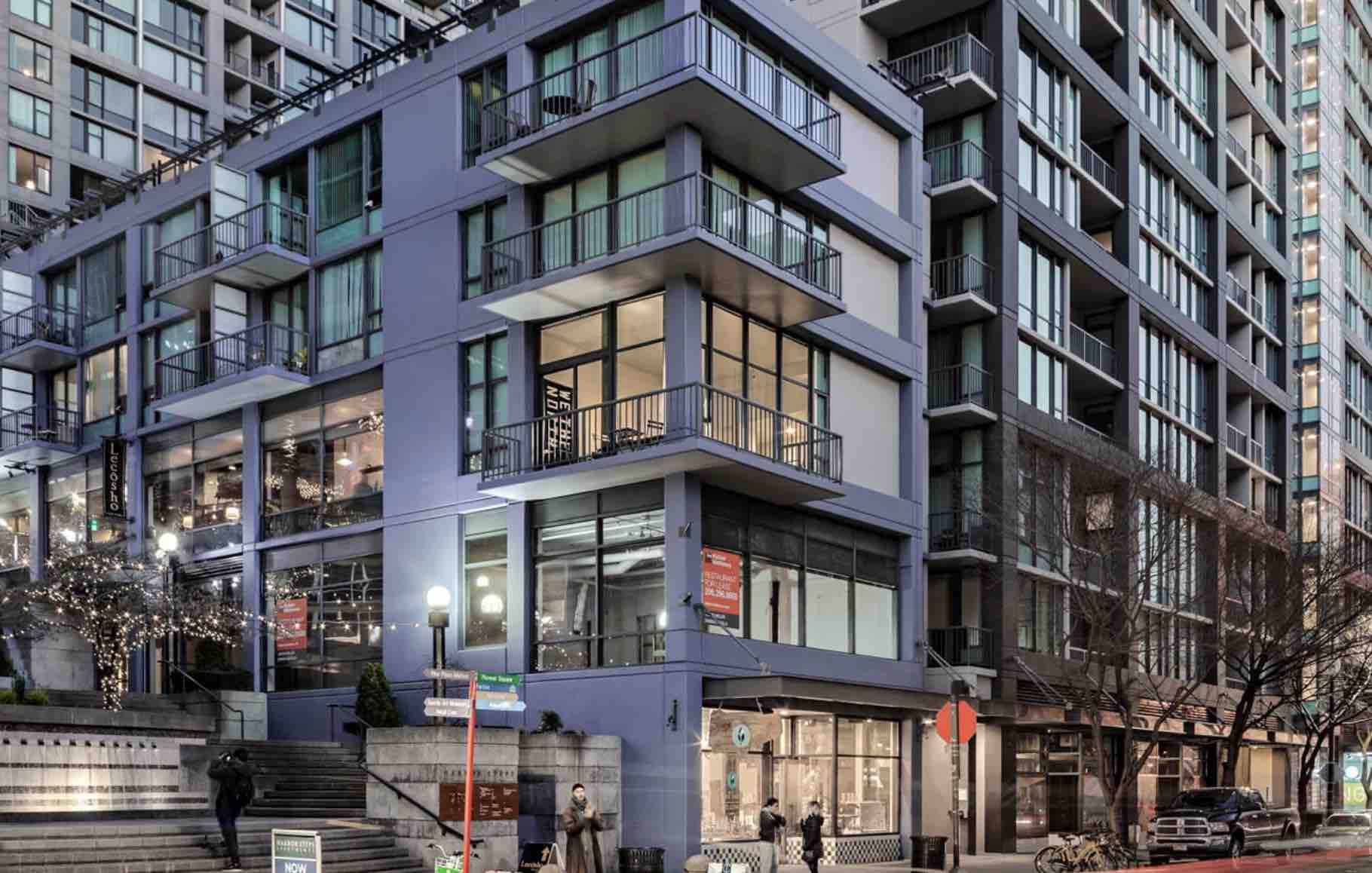
The Difference Between Elastomeric Coatings Can Be Substantial
Tnemec's Series 156, an elastomeric coating that's redefining expectations for durability, moisture resistance, and long-term performance in demanding environments.
- High Performance Coatings
The performance differences between elastomeric coatings should be compared before specifying.
Not all Elastomeric Coatings Perform Equally
In the world of architectural coatings, not all elastomeric products are created equal. While many building professionals default to familiar brands and traditional formulations, cutting-edge advancements in polymer chemistry have created a new generation of protective coatings that significantly outperform their conventional counterparts. Today, we're exploring Tnemec's Series 156 Enviro-Crete, a revolutionary coating that's redefining expectations for durability, moisture resistance, and long-term performance in demanding environments.
The Science Behind Superior Performance
Breaking Down the Chemistry
At its core, Series 156 Enviro-Crete utilizes a styrenated acrylate formulation – but that's where the similarities to standard elastomeric coatings end. This specialized resin incorporates self-cross-linking micro-polymer technology that fundamentally changes how the coating performs at a molecular level.
Traditional 100% acrylic elastomeric coatings (like those offered by Sherwin-Williams, PPG, and other major manufacturers) rely on simple polymer structures where long acrylic chains essentially lie atop one another without chemical bonding. This structure, while flexible, creates inherent vulnerabilities in moisture resistance and long-term UV stability.
Enviro-Crete takes a different approach. Each acrylate polymer chain is silane-tipped at both ends, creating reactive groups that form genuine chemical cross-links during the curing process. This results in a significantly tighter, more cohesive film that maintains flexibility while dramatically improving resistance to moisture penetration and UV degradation.
The Hollow Bead Innovation
Perhaps one of the most innovative aspects of Series 156 is its incorporation of inert hollow glass microspheres. These specialized beads serve multiple critical functions:
- Weight Reduction: At just 1/8th the weight of conventional pigments, these hollow microspheres allow for excellent film build without excessive loading of anti-sag additives. This creates a more uniform application and better overall coverage.
- Enhanced Light Reflection: The spherical structure of these beads creates a unique optical property where light actually reflects twice as it passes through the coating. This double-reflection mechanism significantly improves both hiding power and UV resistance, as harmful radiation is scattered before it can damage the underlying polymer structure.
- Superior Moisture Resistance: Unlike traditional pigments that can absorb water over time, the glass composition of these microspheres is inherently hydrophobic. This property enhances the coating's overall water resistance, preventing the gradual performance degradation common in standard elastomerics.
Micro-Polymer Penetration
The exceptionally small particle size of Enviro-Crete's micro-polymers provides another significant advantage: enhanced substrate penetration. This molecular-level penetration allows the coating to reach deeper into microscopic pores and hairline cracks in concrete, masonry, and other substrates. The result is superior adhesion and a more effective moisture barrier that protects against the primary causes of substrate deterioration.
Performance Comparison: Enviro-Crete vs. Standard Elastomerics
The true measure of any coating's value is found in its performance metrics. When we compare Series 156 Enviro-Crete to standard acrylic elastomerics like Sherwin Williams Conflex, the differences become starkly apparent through standardized ASTM testing results.
Moisture Vapor Control: ASTM D 1653
Moisture vapor transmission is perhaps the most critical performance differentiator between these coating technologies. Lower permeability means better protection against moisture infiltration, which directly impacts substrate deterioration and rebar corrosion.
Performance Metric | Series 156 Enviro-Crete | Standard Acrylic Elastomeric Coating |
---|---|---|
Water Vapor Transmission (WVT) | Max 37.44 g/m² per 24h | Typically 150-300 g/m² per 24h |
Water Vapor Permeance (WVP) | Max 3.09 perms | Typically 15-35 perms |
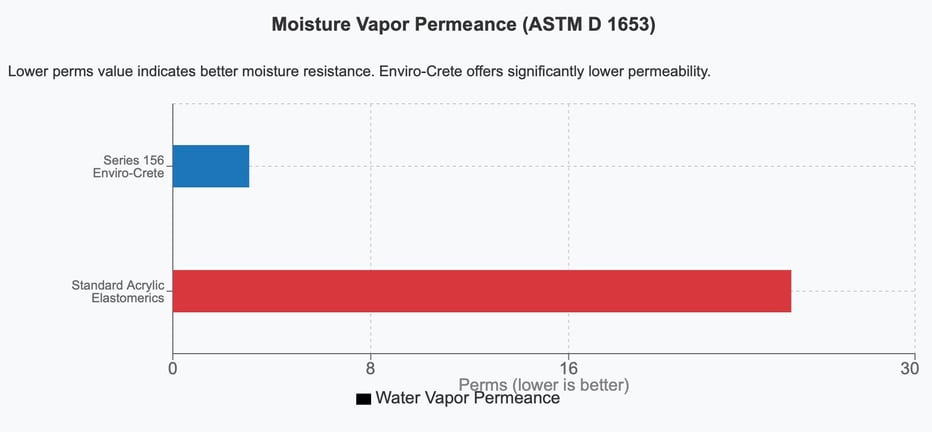
Why This Matters: The dramatic difference in permeability (up to 10x lower with Enviro-Crete) significantly reduces moisture migration through the coating. For reinforced concrete structures, this translates to superior protection against the primary cause of deterioration: moisture-induced rebar corrosion. The cross-linked polymer structure of Enviro-Crete achieves this lower permeability while still allowing enough vapor transmission to prevent blistering from trapped moisture.
Long-Term UV Stability: ASTM D 4587 QUV
Accelerated weathering tests simulate years of UV exposure in a controlled laboratory environment, providing insight into long-term performance expectations.
Performance Metric | Series 156 Enviro-Crete | Standard Acrylic Elastomeric Coating |
---|---|---|
Exposure Duration Without Failure | 5,000+ hours | Typically 2,000-3,000 hours |
Gloss Retention | Minimum 69% | Typically 30-50% |
Maximum Gloss Loss | 1.1 units | Typically 3-7 units |
Color Change (ΔE) | Maximum 3.59 DE | Typically 5-12 DE |
Physical Integrity | No blistering, cracking, chalking or delamination | Often shows chalking and minor cracking after extended exposure |
Why This Matters: UV degradation is a primary failure mechanism for exterior coatings. The significant difference in gloss retention and color stability between Enviro-Crete and standard elastomerics translates to longer aesthetic service life and reduced maintenance costs. The silane-tipped polymer structure and hollow glass microspheres in Enviro-Crete provide this enhanced UV protection through chemical stability and light-scattering properties.
Corrosion Resistance: ASTM B117 Salt Fog
The salt fog test exposes coatings to an aggressive corrosive environment that simulates coastal exposure or de-icing salt conditions.
Performance Metric | Series 156 Enviro-Crete | Standard Acrylic Elastomeric Coatings |
---|---|---|
Exposure Duration Without Failure | 5,000+ hours | Typically 1,000-3,000 hours |
Condition After Exposure | No blistering, cracking or delamination; no visible damage to coating or substrate |
Often shows blistering, delamination at scribe lines, and substrate corrosion |
Why This Matters: In aggressive environments (coastal regions, highway structures exposed to de-icing salts, or industrial areas), corrosion resistance directly impacts infrastructure longevity. The exceptional salt fog resistance of Enviro-Crete provides critical protection that extends service life and reduces lifecycle costs for these exposed structures.
Overall Performance Profile
When we compare all performance metrics simultaneously, the comprehensive advantages of Series 156 Enviro-Crete become evident:
The radar chart illustrates how Series 156 Enviro-Crete outperforms standard acrylic elastomerics across all critical performance parameters, creating a larger "performance envelope" that translates to superior protection and longevity.
Side-by-Side Field Performance: Real-World Results
Laboratory testing provides valuable standardized metrics, but real-world performance tells the complete story. Below, we examine comparative field performance of Series 156 Enviro-Crete against standard acrylic elastomerics like Sherwin Williams Conflex in different exposure conditions after 7 years of service.
Specification Guidance: Avoiding Low Performing Substitutions
When specifying coatings for high-performance applications, precision in documentation is essential. Standard elastomeric products are often submitted as "equals" to premium formulations like Enviro-Crete, despite significant performance differences.
To ensure your project receives the intended protection, specify Series 156 generically as a "waterborne acrylate" rather than an "acrylic elastomeric." This distinction helps prevent substitution with conventional acrylic elastomeric, like Sherwin-Williams' Loxon or Conflex XL, which lack the advanced cross-linking technology and performance characteristics of Enviro-Crete.
For additional specification protection, include the performance requirements detailed above in your project documents. These quantifiable metrics establish clear benchmarks that typical elastomeric coatings cannot meet.
Lifecycle Cost Analysis: The Real Value Proposition
While the initial material costs for advanced formulations like Series 156 Enviro-Crete typically exceed those of standard elastomerics by 15-30%, a comprehensive lifecycle cost analysis reveals the true economic advantages of this investment. The standard elastomeric coating requires reapplication every 7-10 years due to degradation, color fading, and loss of protective properties. These reapplication cycles include:
- Material costs
- Labor costs for preparation and application
- Facility disruption costs
- Potential costs from substrate deterioration between coating cycles
In contrast, Series 156 Enviro-Crete typically maintains its protective and aesthetic properties for 15-20+ years, resulting in:
- Eliminated reapplication costs
- Minimized maintenance expenses
- Reduced substrate repair requirements
- Lower total cost of ownership by approximately 30-45% over a 20-year period
Beyond Economics: Additional Benefits
The value proposition extends beyond direct cost savings to include:
- Reduced environmental impact through fewer reapplication cycles and associated waste
- Minimized facility disruption and operational impacts
- More predictable capital planning with fewer maintenance interventions
- Enhanced asset protection and extended infrastructure lifespan
- Improved aesthetic longevity and consistent appearance
For building owners, facility managers, and design professionals concerned with both initial quality and lifecycle performance, the advanced polymer technology in Series 156 represents a significant advancement over conventional elastomeric coatings. By understanding and specifying these differences, you ensure your projects receive both superior protection and exceptional long-term value.
LET OUR KNOWLEDGE AND EXPERTISE HELP ENSURE YOUR NEXT PROJECT IS SUCCESSFUL
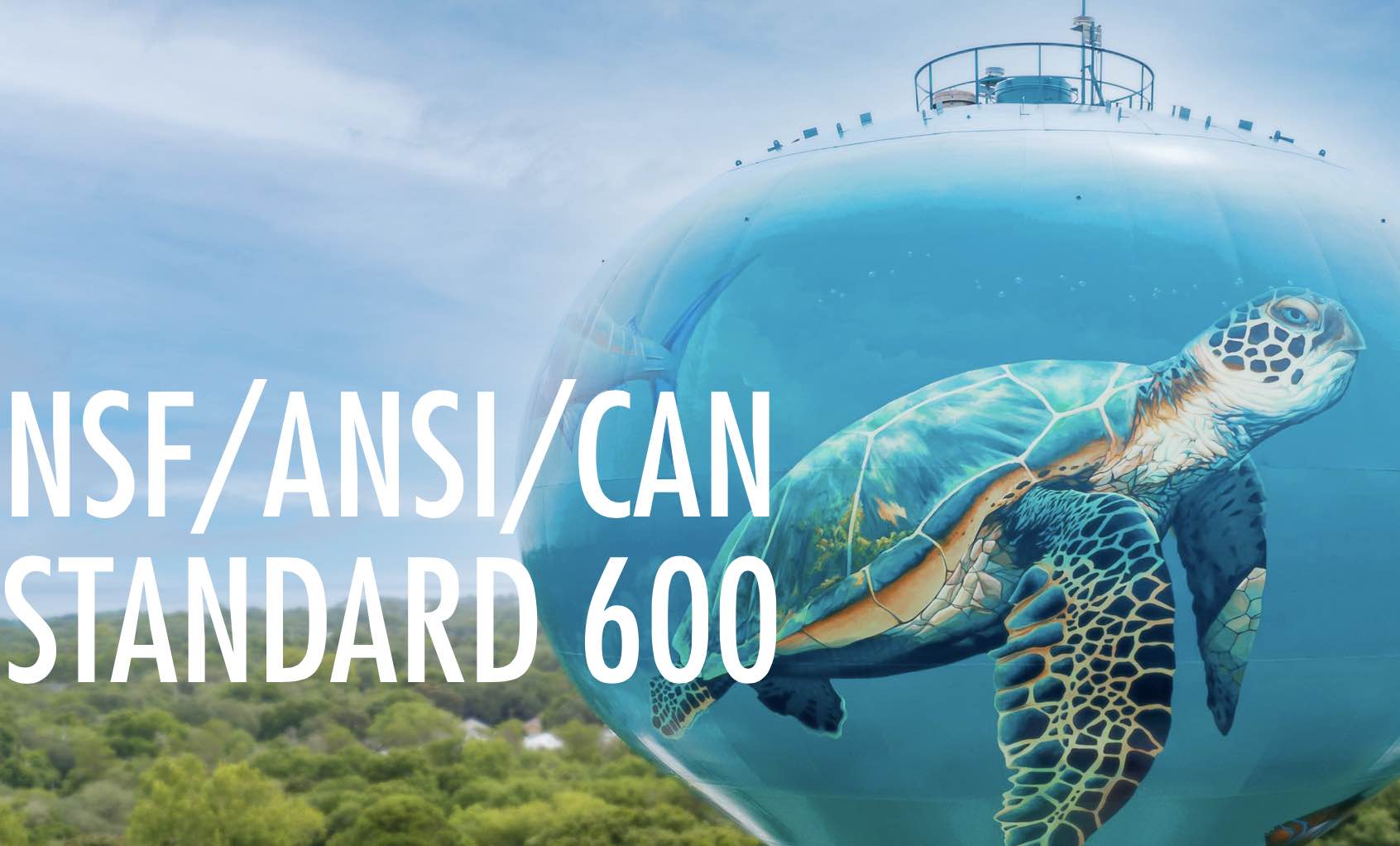
What is NSF / ANSI / CAN 600?
NSF/ANSI/CAN Standard 61 with the NSF 600...
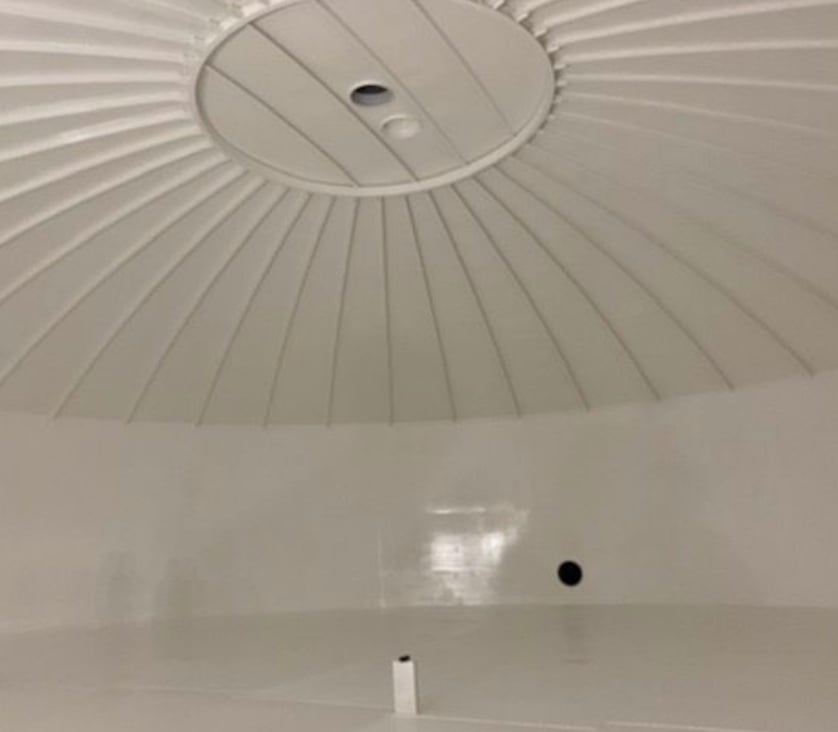
No Need To Fear NSF-600!
Tnemec Company is well-prepared for the changes...
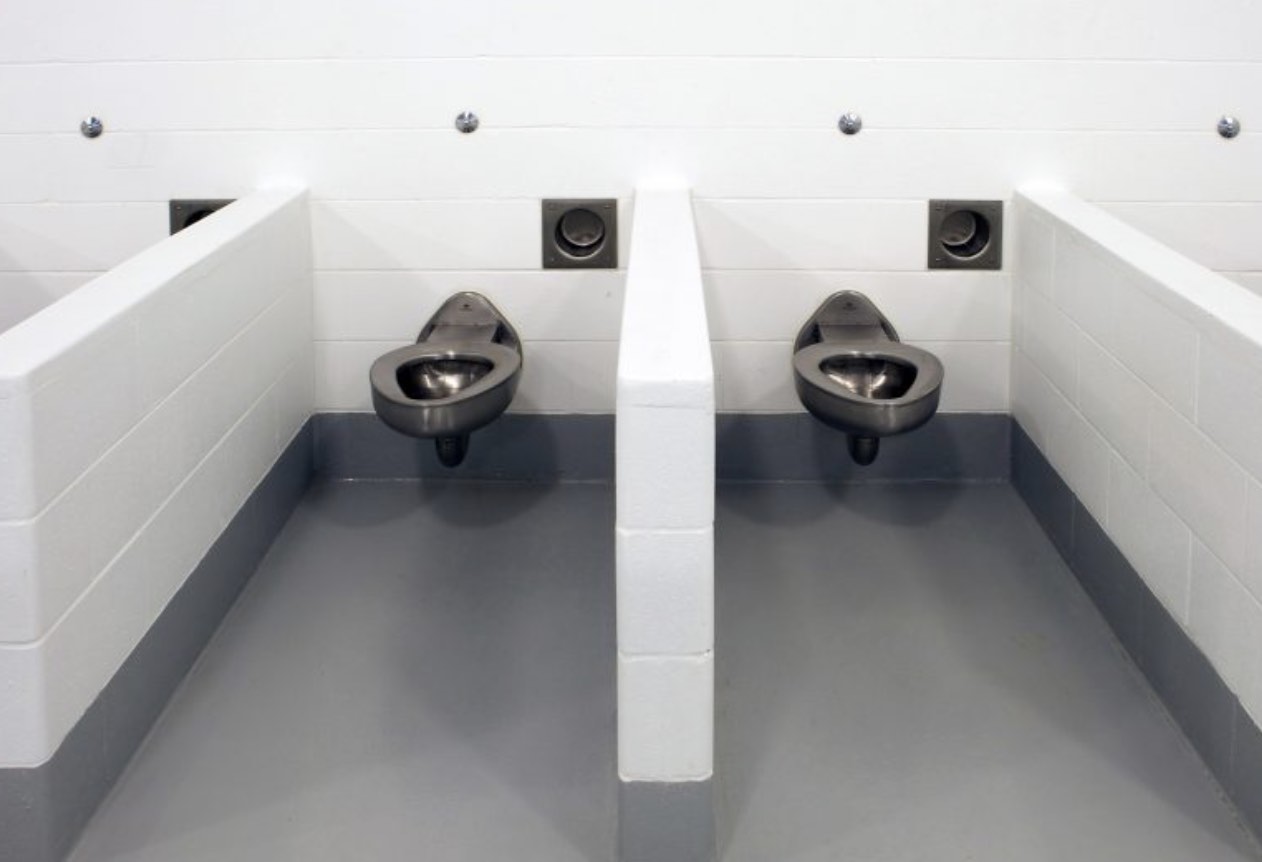
Correctional Facilities Require Coatings That...
Correctional Facilities require coatings that...