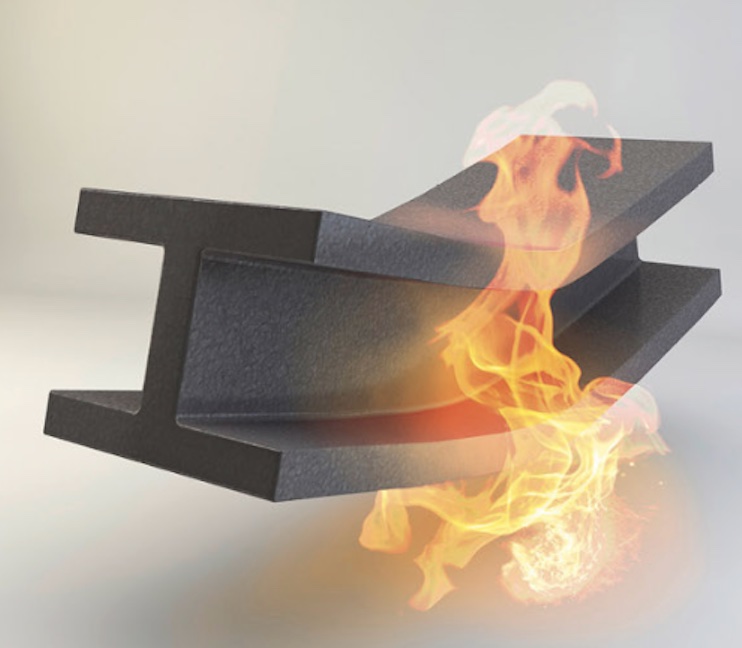
A Comprehensive Overview of Fireproofing Methods, Intumescent Focus
Our goal, in this blog, is to provide you with a comprehensive understanding of the various fireproofing materials, and their wide-ranging applications
- High Performance Coatings
In this blog, we will delve into the diverse range of fireproofing methods used in the construction industry, with a specific focus on the remarkable benefits of intumescent fireproofing. Our goal is to provide you with a comprehensive understanding of the various fireproofing materials, their wide-ranging applications, and the reasons why intumescent fireproofing is increasingly becoming the preferred choice in specific scenarios.
Fireproofing is a crucial aspect of building construction and safety. It involves implementing fire-resistant materials or coatings to protect structural elements from the devastating effects of fire. There are multiple fireproofing options available, each offering distinct benefits. This paper discusses three primary types: cementitious fireproofing, vermiculite-based systems, and intumescent fireproofing.
Cementitious fireproofing is a traditional method that involves applying a mixture of cement, aggregates, and fibers to structural elements. It provides good thermal insulation and can endure high temperatures. Cementitious fireproofing is often used for steel structures in industrial and commercial buildings.
Vermiculite-based fireproofing utilizes a lightweight aggregate derived from the mineral vermiculite. The mixture is spray-applied to create a protective layer. This type of fireproofing is suitable for steel and concrete substrates and offers excellent acoustic insulation in addition to fire protection.
Intumescent fireproofing, or intumescent coatings are a modern and widely used method of fire protection that has gained popularity due to its unique properties. It is typically applied as a thin coating to structural elements, such as steel beams and columns (or other steel structures). When exposed to heat from a fire, the intumescent coating expands to form a protective and insulating char layer, shielding the underlying structure.
When considering the use of intumescent coatings, it's essential to take into account the level of fire resistance required and the specific fire hazard exposure. Here are different types of intumescent coatings and their typical applications:
1. Thin-Film Intumescent Coatings:
- Application: Thin-film intumescent coatings are suitable for protecting structural steel components in buildings, such as beams, columns, and joints.
- Use Cases: Commercial buildings, high-rise structures, warehouses, and industrial facilities often utilize thin-film intumescent coatings to provide fire protection for their steel elements.
2. Thick-Film Intumescent Coatings:
- Application: Thick-film intumescent coatings are designed for higher fire resistance and are often used in more severe fire exposure scenarios.
- Use Cases: Critical infrastructure, petrochemical facilities, offshore platforms, and areas with heightened fire risks may require thick-film intumescent coatings to provide extended fire protection.
3. Hybrid Intumescent Coatings:
- Application: Hybrid intumescent coatings combine different fireproofing materials, such as intumescent and ablative components, to provide a comprehensive fire protection solution.
- Use Cases: Hybrid coatings are often utilized in situations where multiple types of fire hazards are present, or specific fire resistance requirements demand a more customized approach.
4. UL 1709 Jet Fire Intumescent Coatings:
- Application: UL 1709 is a standard specifically for hydrocarbon pool and jet fire scenarios, common in the oil and gas industry and related facilities.
- Use Cases: Oil refineries, petrochemical plants, offshore rigs, and other facilities handling flammable hydrocarbons may require UL 1709-rated intumescent coatings to protect against jet fire incidents.
Benefits of Intumescent Fireproofing:
1. Minimal Thickness: Intumescent coatings require significantly less material thickness compared to traditional methods, making them more space-efficient and aesthetically appealing.
2. Aesthetic Versatility: Unlike cementitious fireproofing, intumescent coatings can be easily concealed beneath paint or architectural finishes, allowing architects to maintain the desired appearance of the building without compromising safety.
3. Faster Application: Intumescent fireproofing can be applied faster, reducing construction time and costs.
4. Lightweight: The low density of intumescent coatings minimizes the added load on the structure, making it ideal for retrofitting and refurbishment projects.
5. Longevity: Intumescent coatings provide durable fire protection, requiring less maintenance over time compared to other fireproofing materials.
6. Passive Fire Protection: Intumescent fireproofing does not rely on external factors (sprinkler systems or alarms) to activate its fire-resistant properties, ensuring passive fire protection even during power outages.
Before specifying an intumescent coating for structural steel, or any fireproofing for that matter, an engineer should consider several key factors to ensure the fire protection solution meets the project requirements:
1. Steel Type and Grade: Understand the type and grade of structural steel being used in the project. Different steel compositions can have varying thermal and structural properties, which can impact the selection of the appropriate intumescent coating.
2. Fire Resistance Rating: Determine the required fire resistance rating for the structural steel members. This rating is usually specified in minutes or hours and indicates the duration of fire protection needed for the steel elements.
3. Fire Exposure Conditions: Evaluate the expected fire exposure conditions in the building or facility. Consider factors like the fire intensity, duration, and potential sources of ignition to choose an intumescent coating suitable for the specific fire hazard scenarios.
4. Steel Surface Preparation: Ensure that the steel surfaces are adequately prepared before applying the intumescent coating. Proper surface cleaning, roughening, and removal of contaminants are essential for the coating's adhesion and performance.
5. Coating Thickness: Calculate the appropriate intumescent coating thickness required to achieve the desired fire resistance rating. The coating thickness is a critical factor in determining the effectiveness of the fire protection provided.
6. Application Method: Consider the application method of the intumescent coating, whether it is sprayed, brushed, or roller-applied. The application method can affect the coating's uniformity and overall performance.
7. Aesthetic Considerations: Determine if the intumescent coating will be visible in the final design or if it needs to be concealed. Some intumescent coatings can be covered with additional architectural finishes without compromising their fire protection capabilities.
8. Building Codes and Standards: Familiarize yourself with relevant building codes and fire protection standards applicable to the project. Ensure that the selected intumescent coating complies with these regulations.
9. Third-Party Testing and Certifications: Look for intumescent coatings that have undergone third-party testing and certification for fire resistance performance. Certifications from reputable organizations, such as Underwriters Laboratories (UL) or British Standards (BS), provide assurance of the coating's reliability.
10. Maintenance Requirements: Consider the maintenance requirements of the intumescent coating over the building's lifespan. Some coatings may require periodic inspections and touch-ups to ensure continued fire protection efficacy.
By thoroughly understanding these factors, an engineer can make an informed decision when specifying the appropriate intumescent coating for the structural steel, ensuring effective fire protection and compliance with safety standards for the construction project.
Further, when selecting an intumescent coating, it's essential to consider the exposure conditions and fire resistance requirements of the specific application. UL-rated intumescent coatings have been rigorously tested to meet industry standards and provide reliable protection in challenging fire scenarios. While there are various fireproofing materials available, intumescent fireproofing stands out due to its numerous advantages, such as minimal thickness, aesthetic versatility, and passive fire protection, and by understanding the benefits and application, architects and engineers can make informed decisions about incorporating this effective fireproofing method into their projects, thereby enhancing both safety and design.
Consulting with fire protection engineers and adhering to relevant safety standards will help ensure that the chosen fireproofing type is appropriate for the intended use and will offer effective fire protection for the given substrate.
Reach out to a HPC Consultant for more information.
Check out our other resources on this topic:
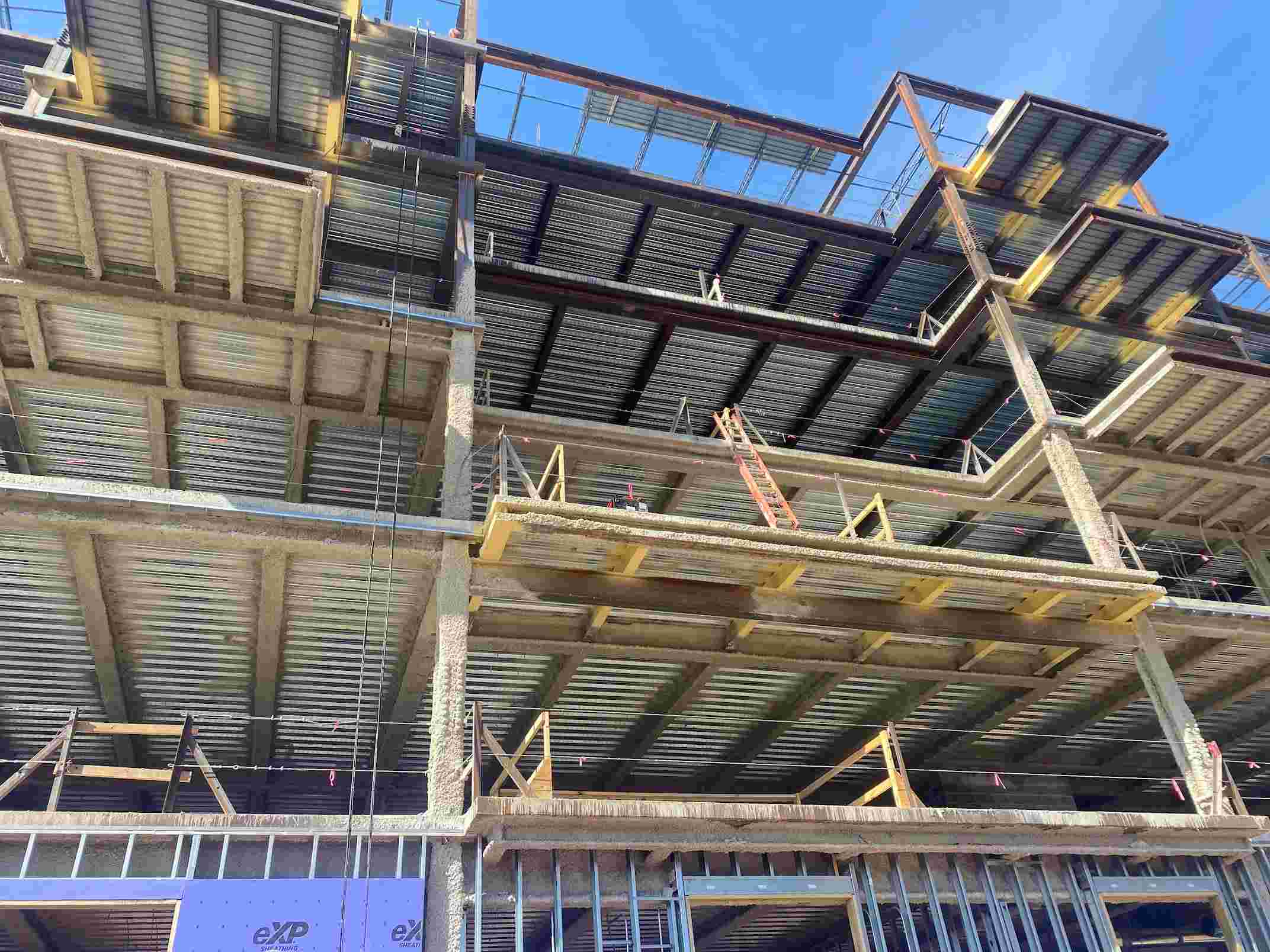
Thermal bridging – a common problem for...
Aerolon can help architects and engineers, using...

Safeguarding The Critical Infrastructure Of Oil...
Oil and gas pipelines and refineries form the...
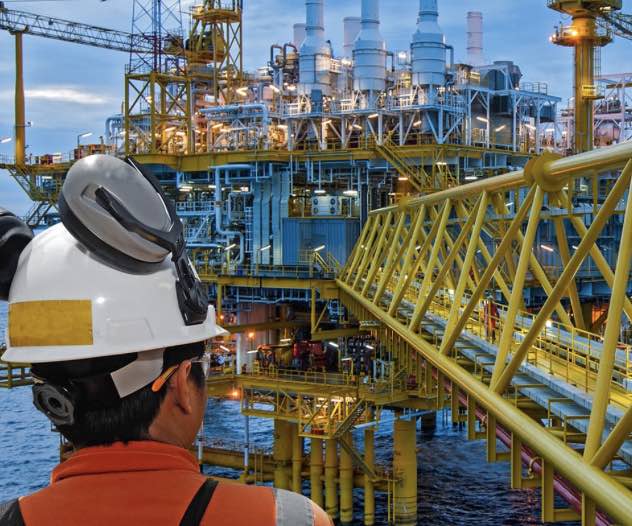
Exploring High Performance Coatings for Offshore...
Offshore and marine structures face relentless...