
Safeguarding The Critical Infrastructure Of Oil and Gas Assets
High performance coatings have emerged as essential solutions to protect and enhance the integrity of oil and gas pipelines and refineries.
- High Performance Coatings
Oil and gas pipelines and refineries form the backbone of energy transportation and storage, spanning vast distances across diverse terrains. However, these assets face numerous challenges, including corrosion, abrasion, chemical exposure, and environmental factors. High performance coatings have emerged as essential solutions to protect and enhance the integrity of oil and gas pipelines and refinery assets. In this blog post, we will explore the challenges faced by asset owners in the oil and gas industry and how high performance coatings provide effective solutions to address these challenges.
1. Corrosion Protection:
Corrosion is a primary concern for oil and gas industry due to the harsh operating conditions and exposure to corrosive substances. High performance coatings offer exceptional corrosion protection, forming a barrier between the pipeline and the surrounding environment. These coatings are specifically engineered to withstand corrosive elements, including moisture, soil chemistry, and aggressive chemicals present in the transported fluids, ensuring the long-term integrity of the pipelines.
2. Abrasion and Impact Resistance:
Pipelines and tank bottoms can experience abrasive forces caused by the movement of particles, such as sand, gravel, or debris, during fluid transportation. High performance coatings provide excellent abrasion and impact resistance, minimizing damage and wear. These coatings create a robust protective layer that can withstand the abrasive forces, reducing the risk of leaks, fractures, and structural failures.
3. Chemical Resistance:
Oil and gas pipelines, tanks, vessels and containment areas come into contact with various chemicals, including hydrocarbons, corrosive fluids, and cleaning agents. High performance coatings exhibit exceptional chemical resistance, preventing chemical attack and degradation. These coatings withstand exposure to acids, alkalis, solvents, and aggressive chemicals, ensuring the integrity of the pipeline's protective layer and preserving the overall performance of the infrastructure.
4. Temperature Extremes:
Oil and gas assets operate in environments with extreme temperatures, ranging from freezing cold to high heat. High performance coatings are designed to withstand temperature extremes, providing thermal insulation and stability. These coatings resist cracking, blistering, or delamination, ensuring consistent protection and performance across a wide temperature range.
5. Environmental Factors:
Pipelines traverse various environments, including deserts, forests, coastal regions, and offshore installations. High performance coatings are engineered to withstand environmental factors such as UV radiation, humidity, moisture, and marine exposure. These coatings offer UV resistance, preventing degradation and color fading, while also providing excellent resistance to moisture and harsh weather conditions.
6. Cathodic Protection Enhancement:
High performance coatings can work in synergy with cathodic protection systems to enhance corrosion prevention on pipelines and tank farms. These coatings act as a barrier, complementing the electrochemical protection provided by cathodic protection methods. By utilizing high performance coatings in conjunction with cathodic protection, pipeline operators can achieve superior corrosion control and extend the lifespan of their infrastructure.
High performance coatings play a crucial role in protecting oil and gas assets from corrosion, abrasion, chemical exposure, temperature extremes, and environmental factors. By applying these coatings, operators can enhance the integrity, durability, and performance of their infrastructure, reducing maintenance costs, preventing leaks, and ensuring the safe transportation and storage of oil and gas. High performance coatings provide effective solutions to the challenges faced by the oil and gas industry, contributing to the reliability and efficiency of critical energy transportation and storage systems.
Check out these other resources
ARO Coatings for Pipeline Protection
Don't miss these project profiles
For a comprehensive site corrosion survey or a review of your coating specification, contact us here.
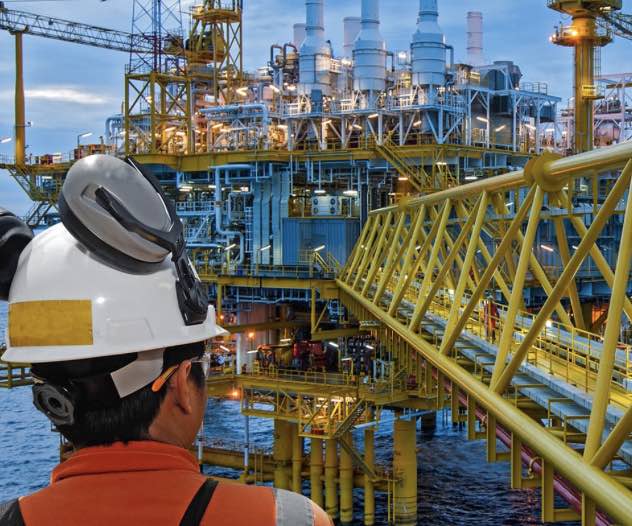
Exploring High Performance Coatings for Offshore...
Offshore and marine structures face relentless...
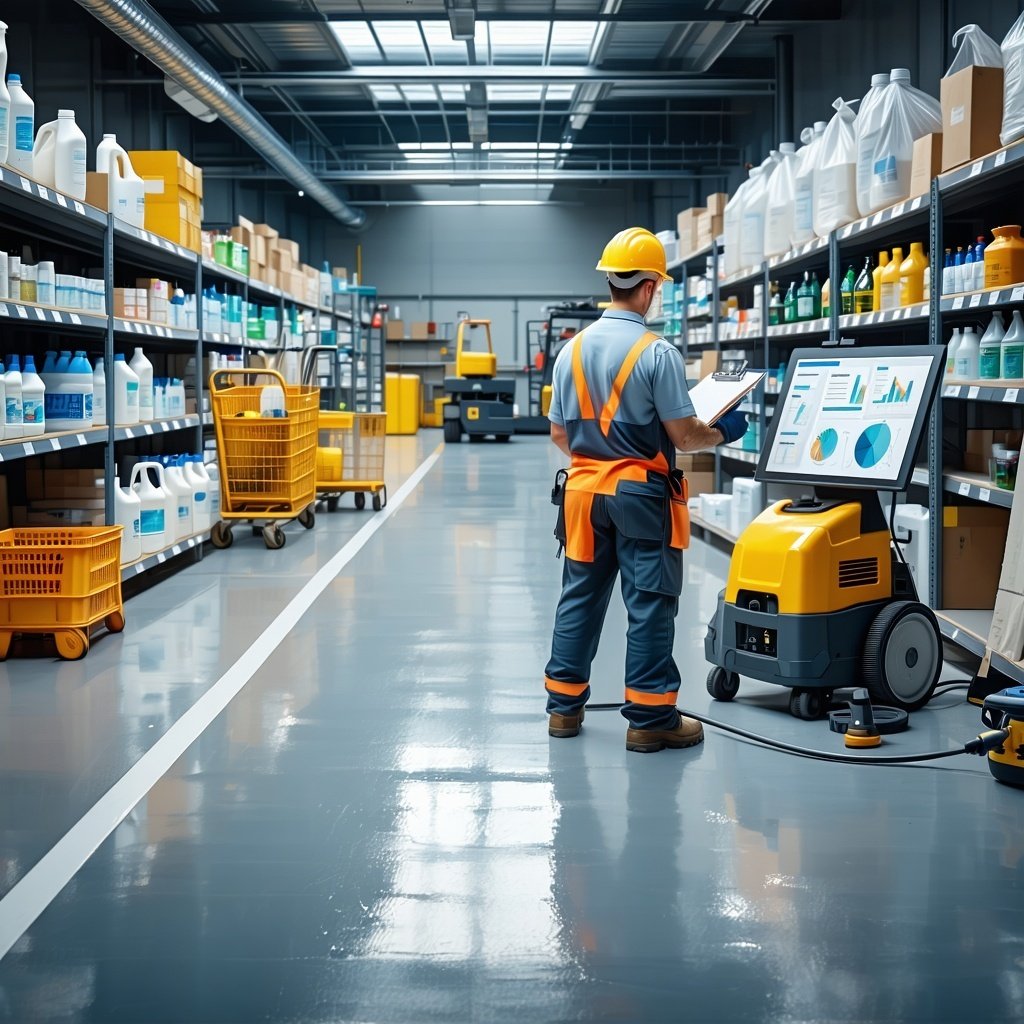
What Maintenance is Required with High...

What Is The Role of High Performance Coatings in...
High performance coatings have transformed the...