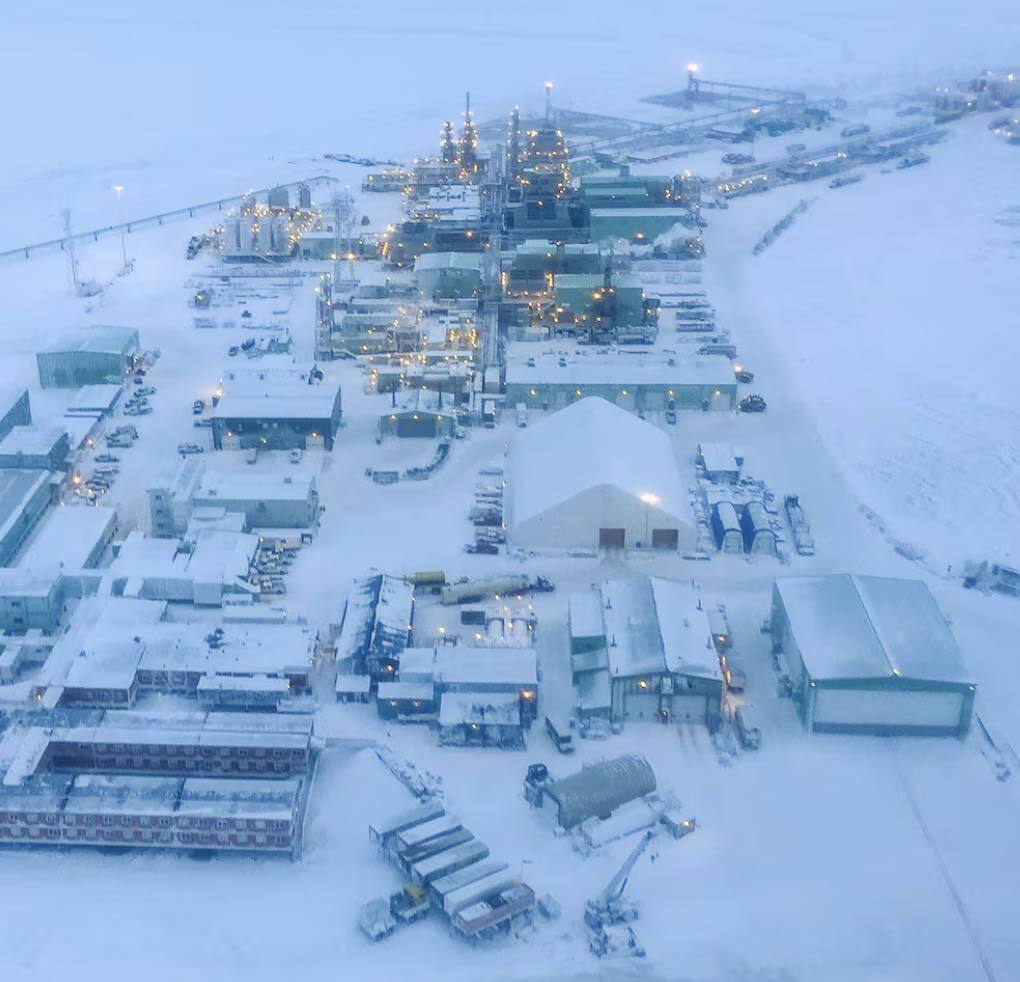
High Performance Coatings in Extreme Winter Conditions
High performance coating projects in cold states like Minnesota and Alaska can't always wait for spring. With cold friendly products, they don't have to.
- High Performance Coatings
High performance coating projects in cold states like Minnesota and Alaska can't always wait for spring. With cold friendly products, they don't have to.
Conquering the Cold: High Performance Coatings in Extreme Winter Conditions
When temperatures plummet below freezing and harsh winter winds sweep across the landscape, most construction and maintenance activities grind to a halt. However, critical infrastructure projects in states like Minnesota and Alaska, for example, can't always wait for spring's arrival. For contractors working in these extreme environments, applying high performance coatings during winter months presents unique challenges that demand specialized solutions and meticulous attention to environmental controls.
The Harsh Reality of Cold Weather Coating Applications
In Minnesota, where winter temperatures regularly drop below -10°F, and in Alaska, where they can plummet to -40°F or lower, traditional coating systems face significant performance limitations. The challenges extend far beyond simply dealing with cold air temperatures – contractors must navigate a complex web of environmental factors that can compromise coating performance and application quality.
Primary Challenges in Cold Weather Applications
Temperature-Induced Viscosity Changes As temperatures drop, coating viscosity increases dramatically, making application more difficult and potentially compromising film thickness uniformity. What flows smoothly at 70°F may become thick and difficult to spray or brush at 35°F, requiring heating systems and specialized equipment.
Moisture and Condensation Issues Cold weather often brings high humidity and condensation problems. When warm coating materials meet cold substrates, moisture can become trapped beneath the coating film, leading to poor adhesion, blistering, and premature failure.
Extended Cure Times Chemical cure reactions slow significantly in cold temperatures. A coating that cures in 4 hours at room temperature might require 12-24 hours at 20°F, extending project timelines and increasing exposure to weather-related complications.
Substrate Preparation Challenges Cold steel and concrete can be particularly difficult to prepare properly. Frost formation, ice accumulation, and thermal shock from heating equipment can create surface contamination that compromises coating adhesion.
Environmental Control: The Key to Success
Successful cold weather coating applications require sophisticated environmental control systems that go far beyond simple heating. Contractors in Minnesota and Alaska have developed specialized approaches to create optimal application conditions even in extreme weather.
Temporary Enclosures and Heating Systems
Professional cold weather coating operations typically involve constructing temporary enclosures around the work area. These structures must provide:
- Temperature Control: Maintaining consistent temperatures between 50-80°F within the enclosure
- Humidity Management: Controlling relative humidity to prevent condensation
- Air Quality: Ensuring proper ventilation for worker safety and coating performance
- Substrate Warming: Gradually bringing cold substrates to proper application temperature
Monitoring and Documentation
Advanced coating projects require continuous monitoring of environmental conditions, including:
- Air temperature and humidity
- Substrate temperature
- Dew point calculations
- Wind speed and direction
- Coating material temperature
This data is crucial for quality control and warranty compliance, as coating failures in extreme environments can be catastrophic and expensive to remedy.
Tnemec's Cold Weather Solutions
Recognizing the unique demands of cold weather applications, Tnemec has developed specialized coating systems designed to perform reliably in extreme conditions. These products offer contractors proven solutions for critical infrastructure projects that cannot wait for favorable weather.
Series 335 Tank Lining for Chemical Immersion
The Series 335 stands out as a breakthrough product for cold weather applications in chemical immersion environments. This two-component epoxy tank lining can be applied at temperatures as low as 35°F, significantly extending the application window for contractors in northern climates working on chemical storage and processing facilities. Key features include:
- Low Temperature Application: Reliable performance down to 35°F
- Chemical Resistance: Excellent protection against a wide range of chemicals and solvents
- Moisture Tolerance: Formulated to handle higher humidity levels common in cold weather
- Fast Cure: Optimized cure chemistry for cold temperature applications, with quick return to service
Series 21 Epoxoline Potable Water Tank Lining
For projects requiring potable water storage systems in extreme cold, the Series 21 Epoxoline offers exceptional performance. This specialized tank lining provides:
- Cold Weather Flexibility: Maintains film integrity at extremely low temperatures
- Potable Water Safety: Meets strict standards for drinking water applications
- Chemical Resistance: Protects against water treatment chemicals and disinfectants
- Long-term Durability: Maintains performance despite extreme temperature cycling
Series 132 Chembuild Epoxy
The Series 132 represents Tnemec's commitment to cold weather industrial applications. This high-solids epoxy coating system offers:
- Extended Application Window: Can be applied at lower temperatures than conventional epoxies
- Surface Tolerant: Can be applied over moisture and without dew point considerations
- High Build Capability: Achieves substantial film thickness in fewer coats
- Chemical Resistance: Excellent protection against industrial chemicals and corrosives
- Thermal Shock Resistance: Withstands rapid temperature changes without cracking
Best Practices for Cold Weather Success
Pre-Application Planning
Successful cold weather projects begin with thorough planning months in advance. This includes:
- Weather Monitoring: Tracking long-term forecasts and identifying optimal application windows
- Equipment Preparation: Ensuring all heating, monitoring, and application equipment is properly maintained
- Material Storage: Maintaining coating materials at proper temperatures before application
- Substrate Assessment: Evaluating substrate conditions and preparation requirements
Application Techniques
Cold weather applications require modified techniques and procedures:
- Gradual Temperature Transitions: Slowly warming substrates to prevent thermal shock
- Modified Mixing Procedures: Adjusting mixing ratios and procedures for cold weather viscosity changes
- Equipment Modifications: Using heated hoses, spray equipment, and application tools
- Quality Control Measures: Implementing enhanced inspection and testing protocols
Post-Application Care
Proper curing and protection are critical in cold weather applications:
- Extended Cure Monitoring: Tracking cure progress over extended timeframes
- Protection from Elements: Maintaining environmental controls throughout the cure cycle
- Quality Verification: Conducting thorough testing to ensure coating performance meets specifications
The Economic Impact of Cold Weather Capabilities
For contractors and facility owners in cold climates, the ability to apply high performance coatings during winter months provides significant economic advantages. Projects can proceed on schedule, critical infrastructure maintenance doesn't get deferred, and the shortened construction season typical of northern climates becomes less constraining.
The cost of specialized cold weather coating systems is often offset by:
- Reduced Project Delays: Avoiding costly schedule overruns
- Extended Work Seasons: Maximizing productive work time
- Improved Asset Protection: Applying protective coatings before damaging weather cycles
- Reduced Emergency Repairs: Preventing failures that require expensive emergency interventions
Looking Forward: Technology and Innovation
The future of cold weather coating technology continues to evolve, with ongoing research focused on:
- Lower Application Temperatures: Developing systems that can be applied at even more extreme temperatures
- Faster Cure Systems: Reducing cure times to minimize exposure to adverse conditions
- Improved Durability: Enhancing long-term performance in extreme temperature cycling
- Application Efficiency: Streamlining application processes for cold weather conditions
Conclusion
High performance coatings in cold weather applications represent one of the most challenging aspects of protective coating work. However, with proper planning, specialized products like Tnemec's Series 335, Series 21, and Series 132 (and others) and rigorous environmental controls, contractors can successfully protect critical infrastructure even in the harsh winters of Minnesota and Alaska.
The key to success lies in understanding that cold weather coating is not simply about applying warm materials to cold surfaces – it's about creating controlled environments, using specially formulated products, and implementing proven procedures that account for the unique challenges of extreme weather conditions.
For contractors working in cold climates, investing in cold weather coating capabilities isn't just about expanding business opportunities – it's about providing essential services that keep critical infrastructure protected year-round. As climate patterns continue to evolve and infrastructure demands grow, the ability to apply high performance coatings regardless of weather conditions becomes increasingly valuable.
The combination of advanced coating chemistry, sophisticated environmental controls, and proven application techniques makes it possible to achieve excellent coating performance even when the thermometer reads well below freezing. For the skilled contractor with the right tools and knowledge, winter no longer means the end of the coating season – it's simply another challenging environment to conquer.
LET OUR KNOWLEDGE AND EXPERTISE HELP ENSURE YOUR NEXT PROJECT IS SUCCESSFUL
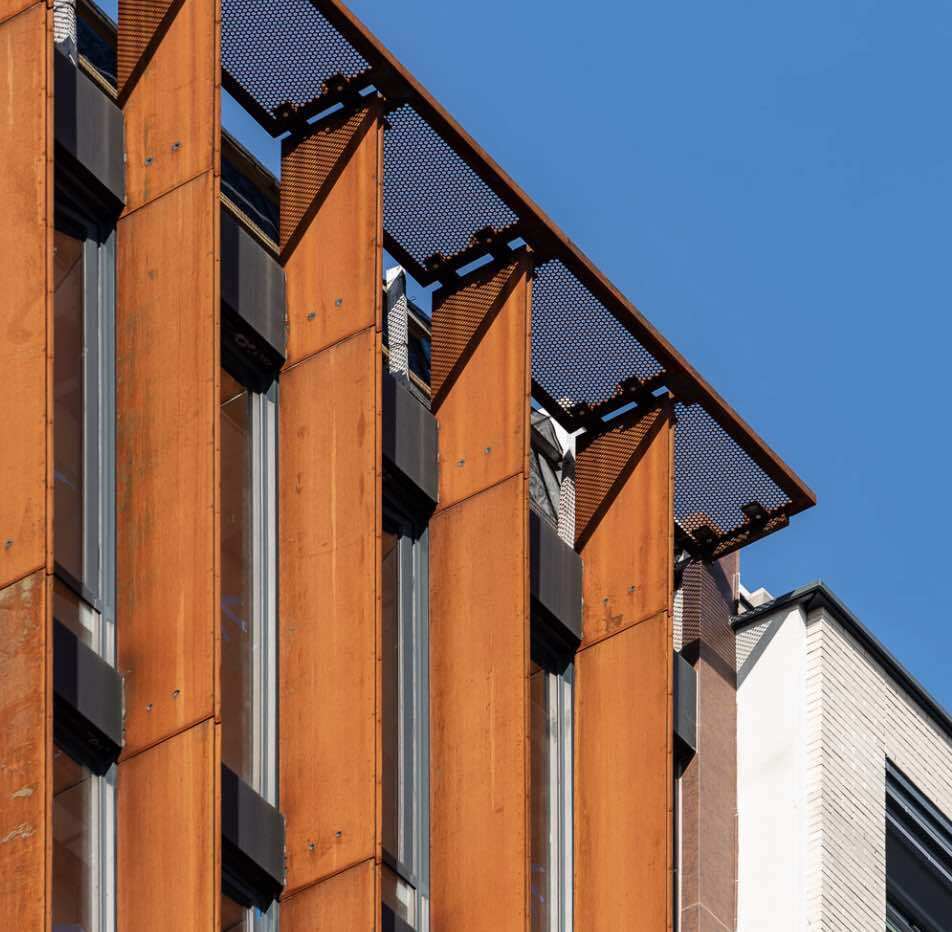
Corten Steel: Essential Guide to Surface...
Corten steel is otherwise known as weathering...
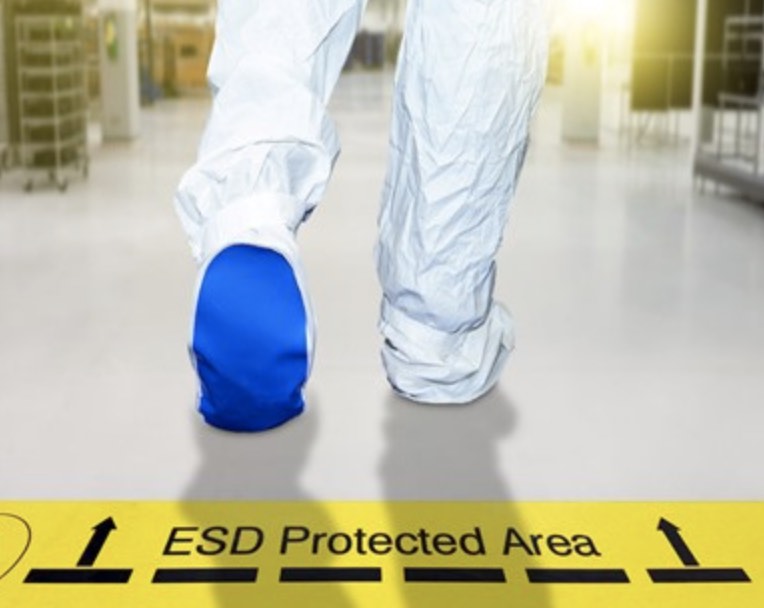
What are Static Dissipative Floor Coatings and...
Static dissipative floor coatings are specialized...
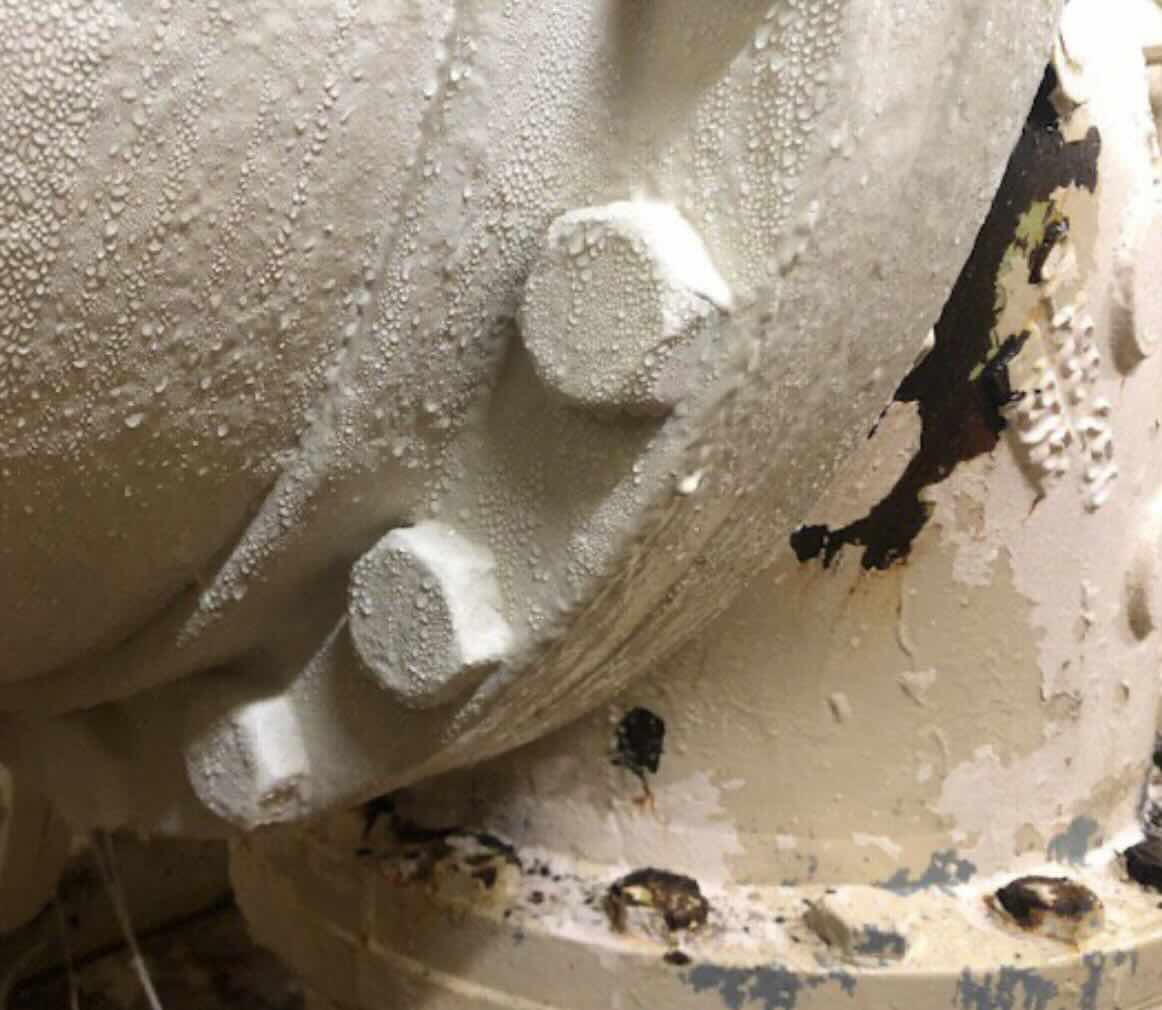
Ultimate Guide to Surface-Tolerant Epoxy Coatings
Discover the resilient world of surface-tolerant...