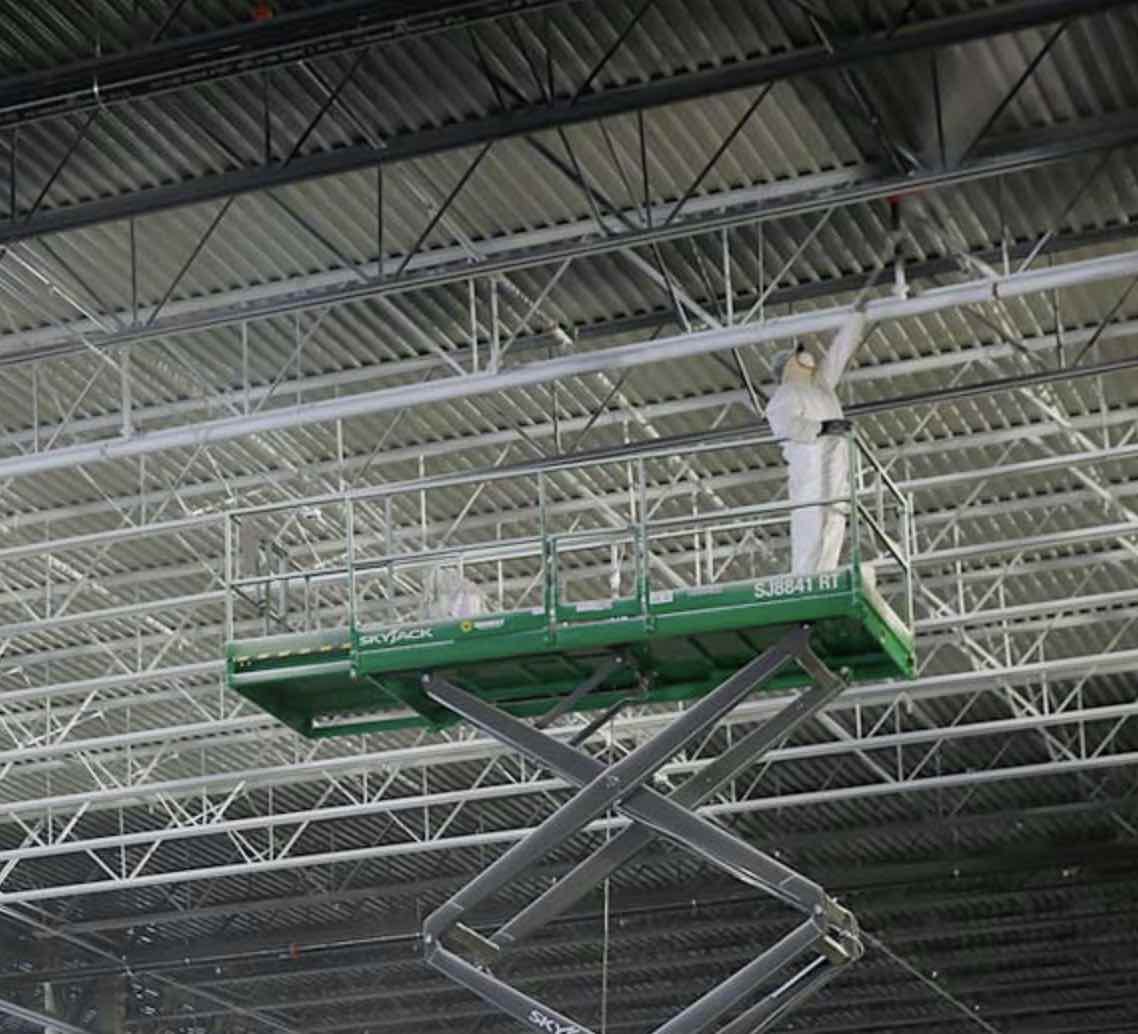
Maintenance Guide for Metal Surfaces with High-Performance Coatings
High-performance coatings provide excellent protection for metal surfaces, but proper maintenance is essential to ensure their longevity and effectiveness.
- High Performance Coatings
High Performance Coatings provide excellent protection for metal surfaces, if you choose the right system.
Maintenance Guide for Metal Surfaces with High Performance Coatings: Tips for Long-Term Durability.
High-performance coatings provide excellent protection for metal surfaces, but proper maintenance is essential to ensure their longevity and effectiveness. This guide outlines best practices for maintaining coated metal surfaces to maximize their durability and performance over time.
Regular Inspection and Cleaning
Regular inspection is the foundation of effective maintenance. Examine coated surfaces often looking for signs of damage such as damage, chips, or areas where the coating appears worn or discolored. Early detection allows for prompt remediation before minor issues become major problems.
For cleaning, use mild, pH-neutral detergents with soft cloths or sponges. Avoid abrasive cleaning tools or harsh chemicals that can degrade the coating. Always rinse thoroughly with clean water after cleaning to remove any residue that could potentially damage the coating over time.
Handling Environmental Factors
Different environments pose unique challenges to coated metals. In coastal areas, salt water exposure can accelerate corrosion, necessitating more frequent cleaning to remove salt deposits. Industrial settings may expose coatings to chemical contaminants that require specialized cleaning protocols. Always adjust your maintenance schedule based on environmental exposure.
For outdoor applications, UV radiation can cause coating degradation over time. Some high-performance coatings include UV inhibitors, but additional protection may be necessary in areas with intense sunlight exposure.
Addressing Damage Promptly
When damage occurs, prompt action is crucial. Small chips or scratches can often be repaired with touch-up products recommended by the coating manufacturer. For larger areas of damage, consult with coating specialists to determine the best approach for repair or reapplication.
Document all maintenance activities and repairs, keeping detailed records of products used, dates of application, and any special conditions or considerations. This documentation provides valuable reference for future maintenance planning.
Preventive Measures
Prevention is always more effective than remediation. Use protective measures such as:
- Sacrificial barriers in high-contact areas
- Graffiti coatings in high risk areas (low steel or accessible concrete)
- Proper handling procedures to minimize physical damage
- Controlled environmental conditions where possible
Professional Assessment
Schedule professional assessments every few years, depending on the coating type and environment. Coating specialists can provide detailed evaluations of coating condition and recommend specialized maintenance procedures tailored to your specific application.
Reapplication Considerations
Even the highest-quality coatings eventually require reapplication. Monitor the coating's condition and consult with the manufacturer about expected service life. Plan for reapplication before the coating deteriorates to the point where the underlying metal is exposed and vulnerable to damage.
Specifiers Can Affect Maintenance Requirements During the Project Design Phase
Aliphatic polyurethane coatings (like Tnemec Series 1095) provide excellent color and gloss retention for exterior applications to steel, concrete, and other substrates in commercial, industrial, and marine environments. Fluoropolymer coatings (like Tnemec Series 1071) are ultra-durable finishes with even better color and gloss retention even in the most severe exposures when compared to polyurethanes.
The key difference between these two high-performance coatings lies in their formulation and longevity. Series 1071 Fluoronar has outstanding resistance to ultra-violet light degradation, providing unprecedented long-term gloss and color retention with excellent resistance to abrasion and chalking. This makes it especially suitable for structures where extremely long-term maintenance cycles are desired or in coastal environments where extremely corrosive exposures will occur.
Comparative Maintenance Requirements
The following tables highlight the differences in maintenance schedules and life cycle considerations between these two coating systems:
Table 1: Inspection and Cleaning Frequency
Maintenance Activity | Series 1095 Endura-Shield | Series 1071 Fluoronar |
---|---|---|
Visual Inspection | Quarterly | Annually |
Routine Cleaning | Every 6-12 months | Every 2-3 years |
Detailed Assessment | Annually | Every 5 years |
Professional Evaluation | Every 2-3 years | Every 5-10 years |
Table 2: Estimated Service Life and Recoating Intervals
Performance Metric | Series 1095 Endura-Shield | Series 1071 Fluoronar |
---|---|---|
Expected Service Life | 10-15 years | 20-30+ years |
Color/Gloss Retention | Good (5-7 years) | Excellent (15+ years) |
First Touch-up | 5-7 years | 10-15 years |
Complete Recoating | 10-15 years | 20-30+ years |
Life Cycle Cost (relative) | Moderate | Higher initial, lower long-term |
Table 3: Environmental Exposure Maintenance Adjustments
Environment Type | Series 1095 Maintenance Adjustment | Series 1071 Maintenance Adjustment |
---|---|---|
Industrial | Additional cleaning for contaminants | Standard schedule with monitoring |
High UV Exposure | Monitor for early degradation | Standard schedule |
Chemical Exposure | Specialized cleaning protocols | Specialized cleaning protocols |
Maintenance Guidelines for Series 1095 Endura-Shield
Regular Inspection and Cleaning
- Quarterly Visual Inspections: Check for scratches, chips, color fading, and chalking.
- Semi-Annual Cleaning: Use mild, pH-neutral detergents with soft cloths or sponges.
- Rinse Thoroughly: Always rinse with clean water after cleaning to remove detergent residue.
- Document Conditions: Keep records of coating appearance and any issues identified.
Damage Remediation
- Touch-up Small Areas: For minor damage, use manufacturer-approved touch-up products.
- Address Surface Contamination: Remove salt, industrial pollutants, and other contaminants promptly.
- Plan for Recoating: Begin assessment for potential recoating at 7-year mark.
Maintenance Guidelines for Series 1071 Fluoronar
Extended Maintenance Schedule
- Annual Visual Inspections: Less frequent due to superior durability and UV resistance.
- Less Cleaning Required: Standard cleaning with mild detergents usually sufficient.
- Long-Term Planning: Recoating typically not required for 15+ years in normal conditions.
Specialized Considerations
- Higher Initial Investment: The initial cost is offset by significantly reduced maintenance requirements.
- Touch-up Protocol: When required, follow manufacturer specifications precisely for touch-up procedures.
- Environmental Resilience: Less maintenance adjustment needed for harsh environments, but regular inspection remains important.
Life Cycle Cost Comparison
Table 4: 20-Year Life Cycle Cost Analysis (Per 1,000 sq. ft.)
Cost Factor | Series 1095 Endura-Shield | Series 1071 Fluoronar |
---|---|---|
Initial Application | $3,000-$4,000 | $5,000-$7,000 |
Cleaning/Maintenance (20 years) | $8,000-$10,000 | $4,000-$6,000 |
Touch-up Repairs | $2,000-$3,000 | $1,000-$1,500 |
Complete Recoats | 2 times ($6,000-$8,000) | None or 1 time ($5,000-$7,000) |
Total 20-Year Cost | $19,000-$25,000 | $15,000-$21,500 |
Annual Cost | $950-$1,250 | $750-$1,075 |
Conclusion
While polyurethanes, like Series 1095 Endura-Shield, provides excellent performance with moderate maintenance requirements, Fluoropolymers, like Series 1071 Fluoronar, offers superior longevity and reduced maintenance frequency, resulting in potentially lower life-cycle costs despite higher initial investment. The choice between these high-performance coatings should be based on the specific application requirements, environmental exposure, and long-term cost considerations.
When properly maintained according to these schedules, both coating systems will provide excellent protection for metal surfaces, with Series 1071 being particularly advantageous for projects where minimal maintenance and extremely long service life are priorities.
LET OUR KNOWLEDGE AND EXPERTISE HELP ENSURE YOUR NEXT PROJECT IS SUCCESSFUL
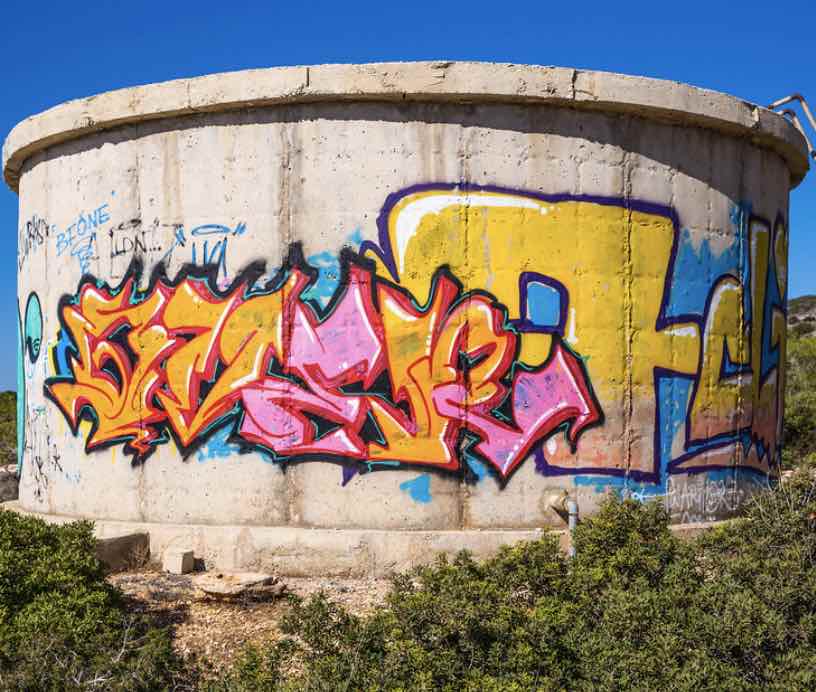
Do High Performance Coatings Provide Graffiti...
High-performance coatings can offer anti-graffiti...
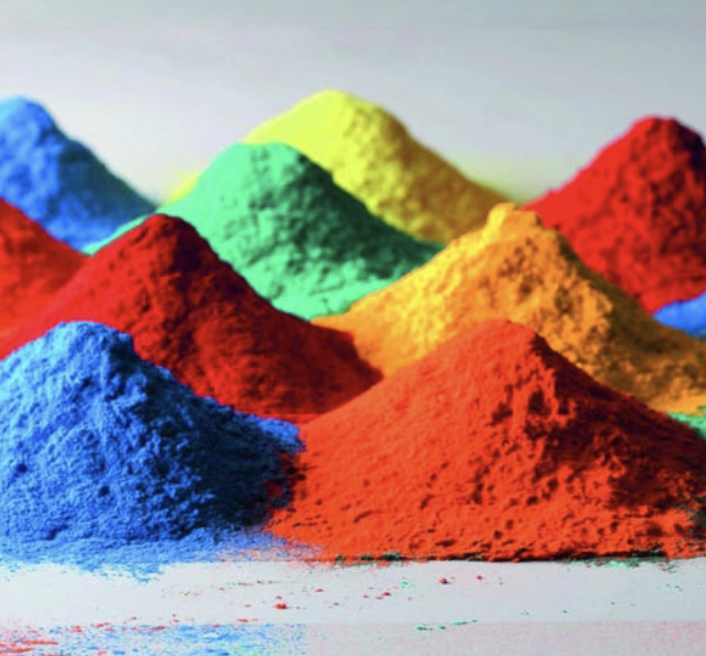
Unleashing Color Brilliance: Blending Pigment for...
Discover how blending pigments can transform the...
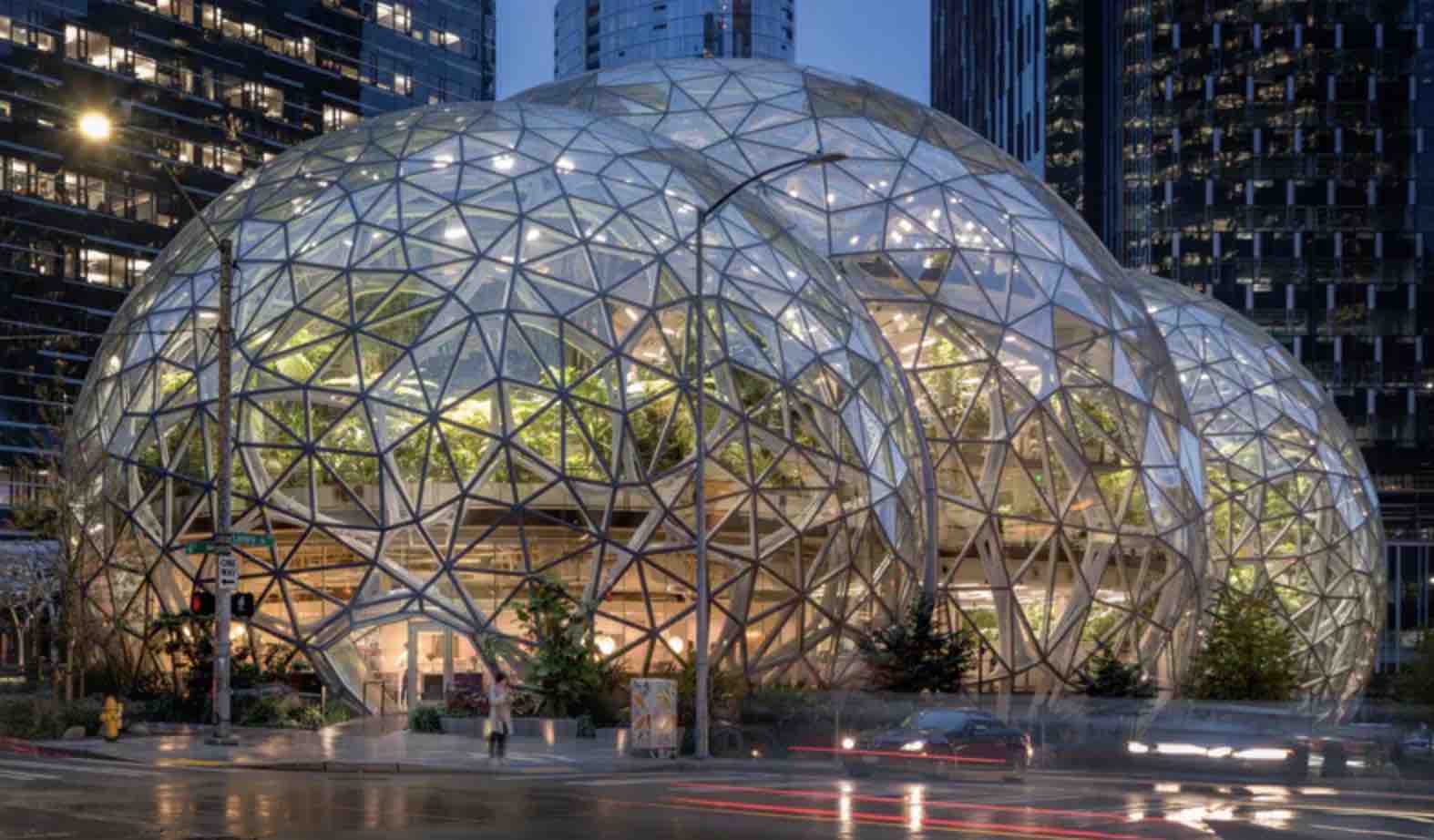