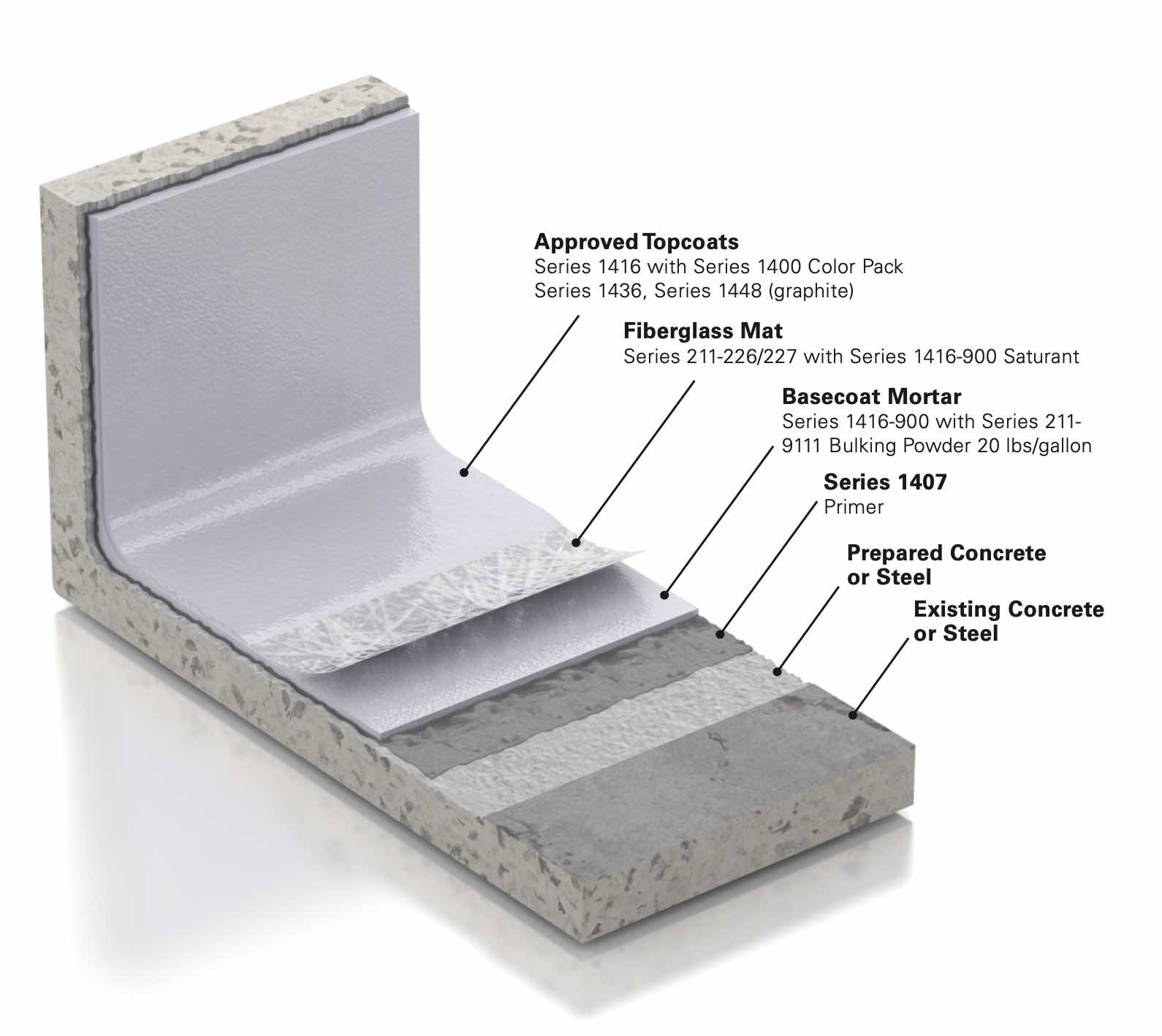
Vinyl Ester Systems (VE): The Solution for Industrial Environments
Vinyl ester systems represent advanced polymer technology engineered to withstand extreme chemical exposure, temperature fluctuations, and abrasion.
- High Performance Coatings
Vinyl Ester systems represent advanced polymer technology engineered to withstand extreme chemical exposure.
Vinyl Ester (VE) Systems: The Solution for Harch Industrial Environments
In today's demanding industrial landscape, protecting infrastructure against corrosion, chemical attack, and extreme environments isn't just about maintenance—it's about ensuring operational continuity and safety. Vinyl Ester (VE) systems have emerged as the gold standard for protection in the harshest industrial settings, but as industry professionals know, not all vinyl ester formulations deliver equal performance.
Understanding Vinyl Ester Systems: Beyond Basic Protection
Vinyl ester systems represent advanced polymer technology specifically engineered to withstand extreme chemical exposure, temperature fluctuations, and abrasion that would quickly degrade conventional coating systems. These high-performance linings combine the superior chemical resistance of epoxies with the processing advantages and resilience of polyesters, creating a versatile protective solution for industrial environments.
What sets vinyl esters apart is their exceptional resistance to acids, bases, solvents, and oxidizing chemicals—conditions commonly found in chemical processing, power generation, wastewater treatment, and food processing facilities. This remarkable chemical resistance, combined with excellent adhesion properties and thermal stability, makes VE systems indispensable where infrastructure protection is mission-critical.
Why All Vinyl Esters Are Not Created Equal
While vinyl esters share a common chemical backbone, significant performance differences exist between products and manufacturers. This reality becomes apparent when discussing vinyl ester systems with industry experts.
A Conversation with Rick, Industrial Coating Specialist:
Rick: "The biggest misconception I encounter is clients assuming all vinyl esters deliver the same performance just because they share the same chemical classification."
Interviewer: "What key factors create these performance differences?"
Rick: "It comes down to three critical areas: resin chemistry, filler selection, and formulation expertise. Standard vinyl esters perform adequately in many environments, but specialized novolac vinyl esters offer substantially improved chemical and temperature resistance. Then there's the filler technology—glass flake versus mineral fillers dramatically affects permeation resistance and thermal stability. Finally, proprietary formulation techniques separate premium products from commodity offerings."
Interviewer: "How do these differences manifest in real-world applications?"
Rick: "I've seen dramatic performance variations in identical environments. Premium vinyl esters can deliver 2-3 times the service life in aggressive chemical immersion or high-temperature settings. That translates directly to reduced maintenance costs and operational disruptions."
Performance Criteria: What Separates Premium Vinyl Esters From Standard Formulations
When evaluating vinyl ester systems for critical applications, understanding key performance criteria is essential:
- Chemical Resistance Spectrum: Standard vinyl esters offer good resistance to acids, while novolac-modified formulations provide enhanced resistance to solvents, oxidizing chemicals, and higher concentrations of acids.
- Temperature Resistance: Basic vinyl esters typically perform well up to 150°F in immersion service, while specially formulated systems can withstand temperatures exceeding 300°F.
- Permeation Resistance: The incorporation of specialized fillers (particularly glass flake) significantly reduces the permeation rate of chemicals through the coating film.
- Application Versatility: Premium systems offer multiple application methods (spray, trowel, roller) without compromising performance.
- Reinforcement Options: The ability to incorporate glass mat reinforcement for enhanced structural integrity and crack-bridging capabilities.
- FDA Compliance: Specially formulated systems meeting FDA requirements for food-grade applications.
Tnemec's Vinyl Ester Systems: Engineered Performance for Specific Challenges
Tnemec has established itself as a leader in high-performance protective coatings, with a comprehensive lineup of vinyl ester systems engineered for specific industrial challenges. Their vinyl ester portfolio reflects the understanding that different applications demand tailored protection solutions.
Table 1: Tnemec Vinyl Ester Systems for Various Industrial Applications
Series | Type | Key Features | Recommended Applications |
---|---|---|---|
1434 | Novolac Vinyl Ester | High molecular weight, glass-flake filled, elevated temperature service | High temperature filtration units, bag houses, exhaust ductwork, chemical immersion |
1438 | Novolac Vinyl Ester | High-build, glass-flake filled, enhanced temperature resistance | FGD units, hot ductwork, wet/dry absorbers, chemical immersion |
1428 | Novolac Vinyl Ester | High film build, heavily corroded substrate rehabilitation | FGD units, repairs, highly corrosive environments |
1432 | Standard Vinyl Ester | FDA-compliant, glass-flake filled | Food grade tanks, thermal cycling vessels, chemical reaction tanks |
1430 | Standard Vinyl Ester | FDA-compliant, mineral flake-filled | Food grade tanks, standalone lining or topcoat |
Table 2: Tnemec Vinyl Ester Performance Comparison
Performance Criteria | Standard VE (Series 1430/1432) | Novolac VE (Series 1434/1438) |
---|---|---|
Chemical Resistance | Good resistance to acids, caustics | Superior resistance to solvents, oxidizers, concentrated acids |
Temperature Resistance | Up to 180°F immersion service | Up to 300°F immersion service |
Application Methods | Spray, roller | Spray, roller, trowel application options |
Filler Technology | Mineral flake/glass flake | Premium glass flake with specialized treatment |
Service Life Expectancy* | 5-7 years in moderate exposure | 7-12+ years in severe exposure |
Suitable Substrates | Steel, concrete | Steel, concrete, heavily corroded surfaces |
*Service life varies greatly depending on specific exposure conditions
System Approach: The Foundation of Successful Vinyl Ester Applications
The performance of vinyl ester systems depends not only on the topcoat quality but on a properly engineered system approach. A correctly specified system includes:
- Surface Preparation: Proper abrasive blasting or other preparation methods to create the optimal anchor profile.
- Primer Selection: Specialized primers like Tnemec's Series 1402 (for food grade applications) or Series 1407 (for general service) that enhance adhesion and substrate sealing.
- Build Coat/Reinforcement: For severely aggressive environments, incorporating reinforcement materials or specialized build coats.
- Topcoat Selection: Choosing the appropriate vinyl ester formula based on specific exposure conditions.
Case Study: Vinyl Ester Performance in Chemical Processing
A major chemical processing facility in the Gulf Coast region faced recurring coating failures in their sulfuric acid storage and transfer systems. Traditional epoxy systems were failing within 18-24 months, creating significant maintenance costs and production disruptions.
After consulting with coating specialists, the facility implemented a comprehensive protection strategy using Tnemec's novolac vinyl ester system:
- Surface preparation to SSPC-SP5 White Metal Blast
- Series 1407 primer
- Series 1434 novolac vinyl ester topcoat with glass flake reinforcement
After five years of continuous service, inspection revealed the coating system maintained excellent integrity with minimal signs of degradation—dramatically outperforming previous systems and delivering substantial return on investment through reduced maintenance requirements.
Conclusion: Making the Right Choice for Your Industrial Environment
When protecting critical industrial infrastructure, the differences between vinyl ester systems become magnified over time. While premium systems may represent a higher initial investment, their extended service life and superior performance in aggressive environments deliver compelling long-term value.
Understanding your specific exposure conditions, consulting with coating specialists, and selecting formulations engineered for your particular challenges will ensure your vinyl ester system delivers the protection your facility demands. Remember—not all vinyl esters are created equal, and the performance differences become most apparent precisely when protection matters most.
For facilities facing the most demanding chemical, temperature, and abrasion challenges, engineered vinyl ester systems like those offered by Tnemec provide proven protection that extends asset life and reduces lifetime maintenance costs. Give us a call, we'll help build the right system for your unique condition.
LET OUR KNOWLEDGE AND EXPERTISE HELP ENSURE YOUR NEXT PROJECT IS SUCCESSFUL
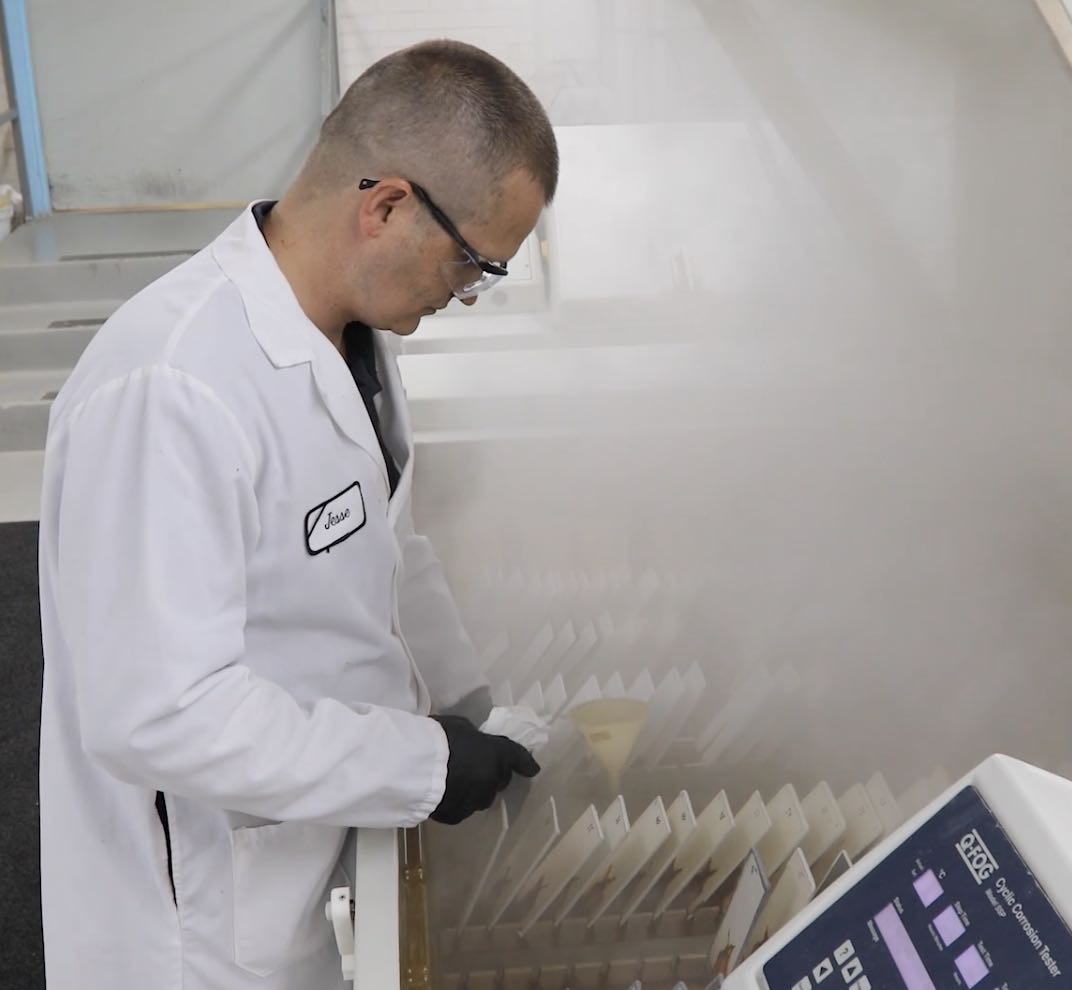
What is ASTM D4585 (Accelerated Weathering)...
ASTM D4585 is a standard practice developed by...

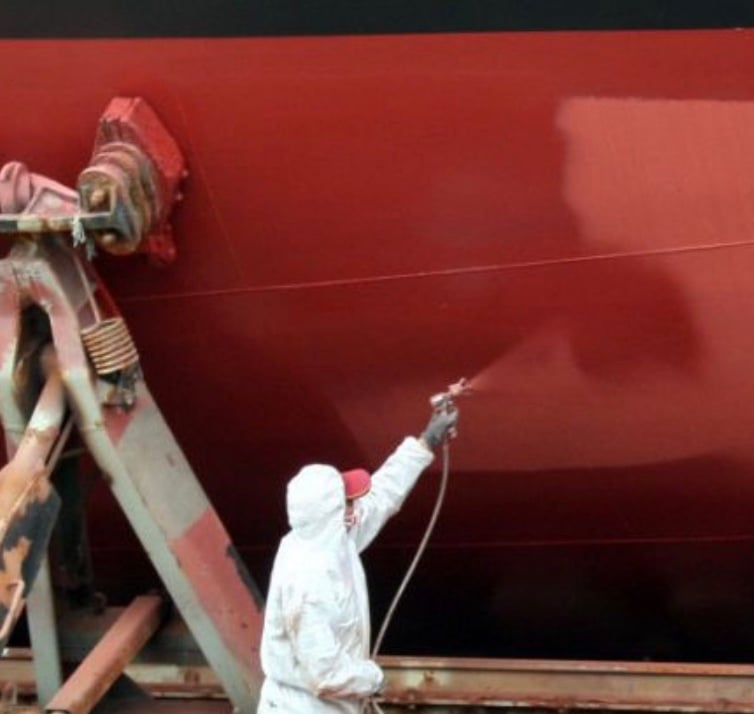
Tnemec's HullClad: The Marine Industry's Trusted...
Challenging marine environments require...