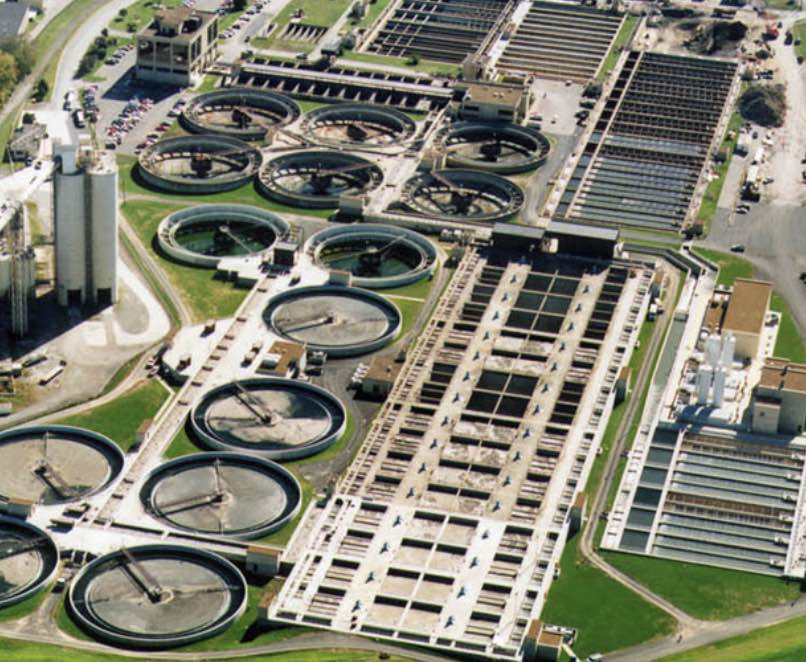
Q&A on Water Treatment Coatings and Linings
Water and wastewater infrastructure require specialized solutions to maintain their structural integrity and operational efficiency.
- High Performance Coatings
Water and wastewater infrastructure requires specialized solutions.
Ask the Experts: Q & A on Waster Coatings and Linings
Ensuring the longevity and safety of data center servers requires specialty coating systems.
Data Center Resinous Flooring: When Performance Matters Most
Introduction
Water and wastewater infrastructure face unique challenges when it comes to protection and longevity. From corrosive chemicals to constant water exposure, these systems require specialized solutions to maintain their structural integrity and operational efficiency. We've consulted with industry experts to bring you answers to the most common questions about water treatment coatings and linings.
What's the difference between a coating and a lining?
According to the Association for Materials Protection and Performance (AMPP), coatings are pigmented materials applied to protect surfaces from environmental effects. The thickness varies based on substrate condition and service environment. Linings, on the other hand, are typically applied to interior surfaces of infrastructure like pipes or wet well structures, providing a critical barrier against highly corrosive environments.
While both serve as the first line of defense against corrosion, they differ in application and thickness. Coatings are generally applied to exterior surfaces using brushes, rollers, or spray guns, while linings are applied to interior surfaces using spray, trowel, or casting methods.
What types of facilities benefit from specialized coatings and linings?
Water and wastewater treatment facilities have numerous structures that depend on protective coatings and linings for durability, including:
- Potable water storage tanks and pipelines
- Wastewater treatment plants and digesters
- Sewage collection systems including manholes and lift stations
- Clarifiers, headworks, and aeration basins
- Chemical storage areas and secondary containment
- Intake structures and sedimentation basins
- Structural steel and facility floors/walls
What materials are commonly used for water treatment coatings and linings?
Several high-performance materials are utilized depending on the specific application requirements:
- Epoxies: Including standard, novolac, and specialized phenalkamide formulations
- Polyurethanes: Both elastomeric and rigid systems
- Vinyl esters: For aggressive chemical resistance
- Cementitious compounds: For concrete restoration
- PVC and HDPE liners: For pipe interiors
- 100% solids formulations: For quick return to service
What factors should be considered when selecting a coating or lining system?
The selection process should account for:
- Environmental exposure conditions (chemicals, pH levels, temperature)
- Required level of protection (chemical resistance, abrasion resistance)
- Substrate material (steel, concrete)
- Application method and constraints
- Regulatory compliance requirements (NSF/ANSI 61, AWWA standards)
- Expected service life and maintenance intervals
- New construction vs. rehabilitation considerations
- Budget constraints and lifecycle cost analysis
How do these systems protect against corrosion?
Protective coatings and linings shield infrastructure through multiple mechanisms:
- Creating impermeable barriers against corrosive chemicals
- Preventing moisture penetration that leads to corrosion
- Resisting biogenic sulfide corrosion common in wastewater systems
- Providing monolithic protection that eliminates vulnerable joints and seams
- Offering resistance to abrasion, impact, and other physical damage
- Creating a barrier against microbiologically induced corrosion (MIC)
What is ASTM G210 and why is it important?
ASTM G210, also known as the Severe Wastewater Analysis Test (S.W.A.T), is a standardized testing protocol that evaluates how protective coatings and linings perform in aggressive wastewater environments. Here's what makes it significant:
- Simulates real-world sewer environments in an accelerated testing format
- Tests materials against the most corrosive elements found in wastewater systems
- Uses a dual-phase testing chamber with both liquid and vapor phases
- Exposes coatings to sewer gases (hydrogen sulfide, carbon dioxide, methane) and sulfuric acid
- Operates at elevated temperatures to accelerate chemical reactions and corrosion processes
- Provides standardized methodology for comparing different coating systems
- Helps predict long-term performance without waiting for years of field testing
- Recognized as an industry innovation, winning the Materials Performance Magazine's first Readers' Choice Corrosion Innovation of the Year Award in 2012
The test involves intermittent immersion of samples in an acidic solution followed by exposure to concentrated sewer gases. After testing, samples are evaluated for various performance criteria including visual changes, adhesion, barrier properties, and structural integrity.
How S.W.A.T Testing Works
The S.W.A.T testing procedure follows a specific protocol to ensure consistency and reproducibility:
- Test Duration: The standard test runs for 28 days
- Sample Preparation: Coatings are applied to steel, ductile iron, or concrete substrates according to manufacturer specifications
- Test Chamber Setup: A sealed glass tank containing a carousel mechanism holds test specimens
- Cycling Process: During weekdays, samples are immersed in a sulfuric acid and saline solution for 15 minutes, three times daily
- Continuous Exposure: Between immersion cycles, samples remain in the vapor phase containing hydrogen sulfide, carbon dioxide, and methane gases
- Temperature Control: The chamber is maintained at elevated temperatures (typically 150°F) to accelerate reactions
- Evaluation Methods: After exposure, samples undergo various assessments including:
- Visual inspection for blistering, cracking, or color changes
- Coating thickness measurements
- Adhesion testing (knife adhesion and tensile adhesion)
- Electrochemical Impedance Spectroscopy (EIS) to assess barrier properties
- Additional substrate-specific evaluations
Evolution and Significance of S.W.A.T Testing
The development of the S.W.A.T test was driven by changing conditions in wastewater management. Several factors contributed to the need for more robust testing:
- Implementation of the Clean Water Act in 1980 led to pretreatment requirements that altered wastewater chemistry
- Regionalization of wastewater facilities created longer transmission distances and more aggressive environments
- Odor control measures increased hydrogen sulfide concentrations in system headspaces
- Traditional coal tar epoxy coatings from the 1950s were failing under these new, more corrosive conditions
The S.W.A.T protocol filled a critical gap in performance evaluation by providing a reliable, reproducible method to assess coating systems specifically for modern wastewater environments. The test has become an essential tool for coating manufacturers, engineers, and facility owners to select appropriate protective systems for these challenging applications.
What certifications or standards should water treatment coatings meet?
For potable water applications, coatings and linings should comply with:
- NSF/ANSI/CAN 61 and NSF-600 for potable water contact
- American Water Works Association (AWWA) standards
- FDA approvals for drinking water applications
For wastewater applications, important considerations include:
- Chemical resistance to hydrogen sulfide (H₂S)
- Resistance to microbiologically induced corrosion
- Appropriate pH resistance (acidic or alkaline materials)
- Abrasion and impact resistance specifications
- ASTM G210 compliance for severe wastewater environments
What are the latest innovations in water treatment protective systems?
Recent advancements include:
- Ultra-high solids linings with high film build capabilities reducing application time
- Epoxy linings (Perma-Shield) offering extended service life
- Quick-curing formulations allowing faster return to service
- 100% solids coatings with zero VOC emissions for environmental compliance
- Edge-retentive properties for superior protection at vulnerable points
- Thermal insulating coatings for temperature control in pipe galleries
- Advanced polymer formulations with enhanced chemical resistance profiles
What's involved in proper surface preparation and application?
Proper preparation and application are critical to system performance:
- Surface preparation includes thorough cleaning, removal of contaminants, and creating appropriate surface profiles
- For concrete substrates, attention to moisture content and pH is essential
- Application methods vary by product but must ensure consistent coverage and thickness
- Quality control testing during application helps verify proper installation
- Ambient conditions including temperature and humidity must be monitored
- Curing times need to be respected before returning systems to service
How do coatings and linings contribute to infrastructure longevity?
These protective systems extend infrastructure lifespan by:
- Preventing premature corrosion that leads to structural failure
- Reducing the need for frequent maintenance and repairs
- Maintaining flow characteristics and system efficiency
- Preserving water quality and preventing contamination
- Protecting against both chemical and physical degradation
- Lowering total ownership costs through extended service intervals
What should maintenance programs include for coated/lined systems?
Effective maintenance programs should incorporate:
- Regular visual inspections for damage or deterioration
- Documentation of system condition over time
- Protocols for spot repairs when needed
- Reapplication schedules based on manufacturer recommendations
- Staff training on identifying early warning signs of failure
- Coordination with facility operations to minimize downtime
Conclusion
Selecting the right coating or lining system for water and wastewater applications requires understanding your specific needs and working with experienced providers. By leveraging modern protective technologies and implementing proper maintenance protocols, water utilities and industrial facilities can significantly extend the life of their infrastructure assets while reducing lifecycle costs and ensuring operational reliability.
For specific project requirements, consulting with a protective coatings specialist who understands the unique challenges of water treatment environments is strongly recommended. Give us an opportunity to help you navigate the complex factors involved in system selection, application, and maintenance planning.
LET OUR KNOWLEDGE AND EXPERTISE HELP ENSURE YOUR NEXT PROJECT IS SUCCESSFUL
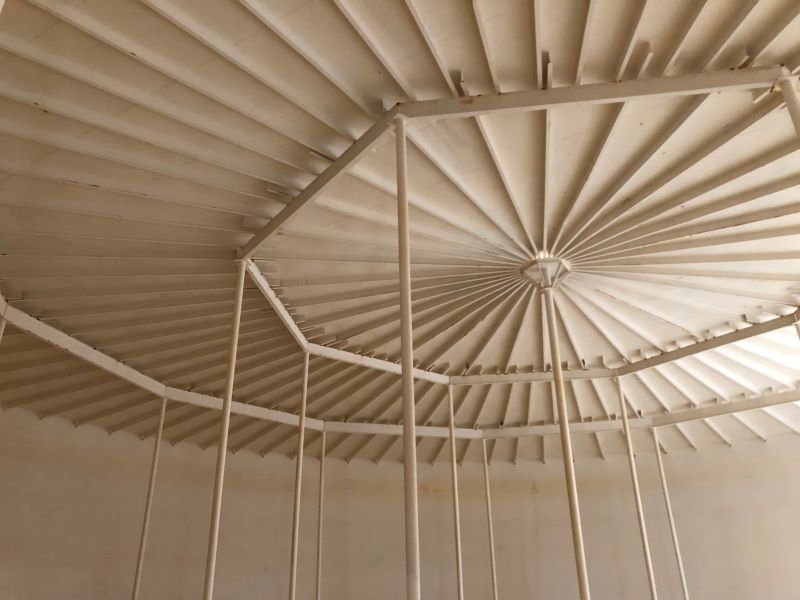
Why Interior Dry Space Coatings Are Essential for...
Ensuring the longevity and safety of potable...
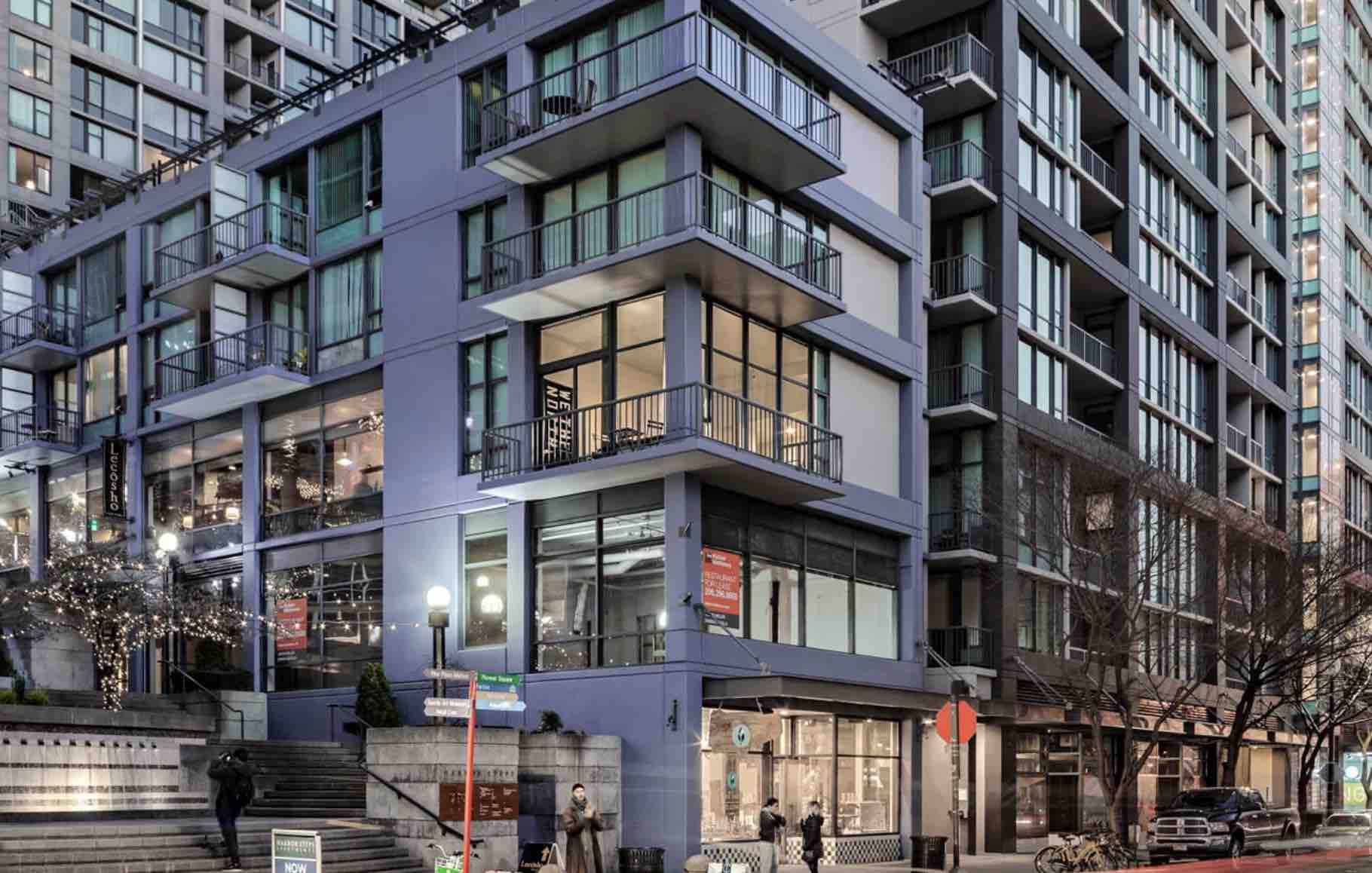
The Difference Between Elastomeric Coatings Can...
The performance differences between elastomeric...
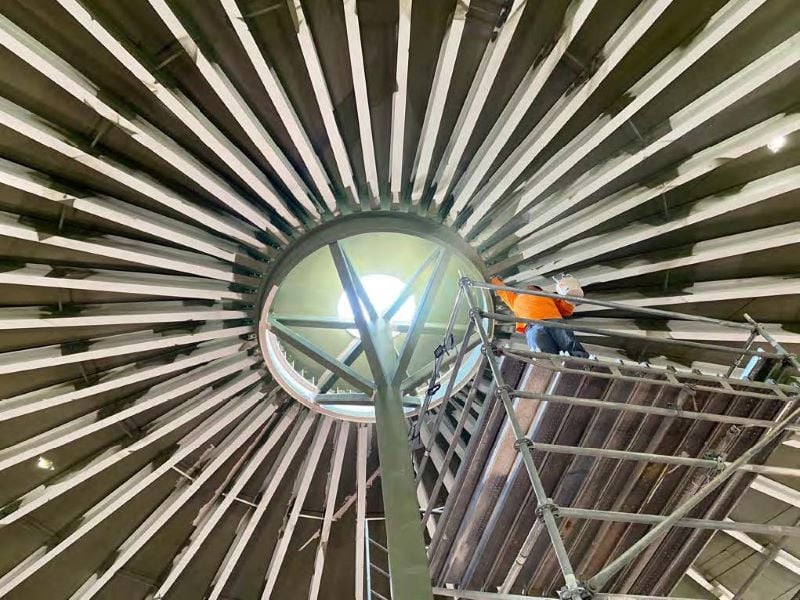
How Our Coatings Ensure Compliance for Potable...
Public Health is more important than ever, when...