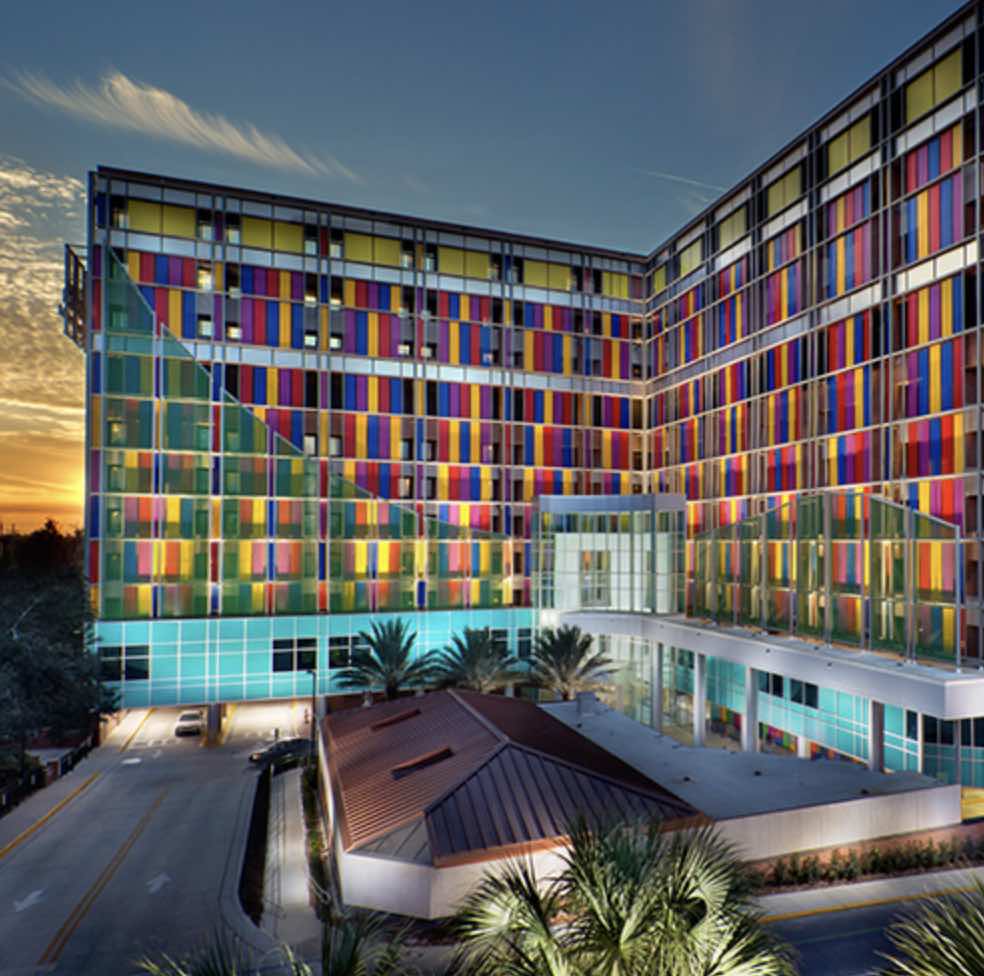
Understanding AAMA 2605 Standards for High Performance Coatings
In the world of architectural coatings, not all finishes are created equal. AAMA 2605 represents the highest level of performance for organic coatings in the industry.
- High Performance Coatings
AAMA 2605 is a stringent performance standard.
Understanding AAMA 2605 Standards for High Performance Coatings
In the world of architectural coatings, not all finishes are created equal. When specifying coatings for aluminum structural steel or curtain wall in building projects, understanding industry standards is crucial for ensuring long-term performance, durability, and aesthetic appeal. Among these standards, AAMA 2605 represents the highest level of performance for organic coatings in the architectural industry.
What is AAMA 2605?
AAMA 2605 is the most stringent performance specification developed by the American Architectural Manufacturers Association (now part of the Fenestration and Glazing Industry Alliance) for superior performing organic coatings on aluminum extrusions and panels used in architectural applications. This rating ensures that materials specified today will maintain their appearance for years to come, even in harsh climates, offering designers and building owners a low-maintenance solution for exterior cladding.
The AAMA Classification System
The AAMA has established three primary performance standards for organic coatings applied to architectural aluminum:
- AAMA 2603: Good performance level (basic standard)
- AAMA 2604: High performance level (intermediate standard)
- AAMA 2605: Superior performance level (highest standard)
These specifications apply to both liquid and powder coatings, contrary to the common misconception that they only apply to liquid coatings. Each standard specifies different performance requirements and testing procedures, with AAMA 2605 being the most rigorous.
Key Requirements of AAMA 2605
What makes AAMA 2605 the gold standard for architectural coatings? The specification includes numerous performance requirements, but here are some of the most significant:
Coating Composition and Application
A coating meeting AAMA 2605 specifications typically consists of a 70% fluoropolymer resin-based coating, such as PVDF (Kynar 500®). These finishes are renowned for their exceptional resistance to various environmental challenges.
Tnemec's Fluoronar is an excellent example of a high-performance coating system that meets AAMA 2605 requirements. This advanced thermoset solution fluoropolymer provides an ultra-durable finish with outstanding color and gloss retention, even in the most severe environmental exposures. Fluoronar's formulation enables it to withstand harsh weathering conditions while maintaining its appearance over extended periods, making it ideal for monumental architectural projects where long-term performance is essential. The coating can be applied via brush, roll, or spray application methods, providing flexibility for various project requirements.
Film Thickness Requirements
For spray-applied coatings, AAMA 2605 requires:
- 80% of measurements must be ≥ 30 microns (1.2 mil) on exposed surfaces
- Minimum individual thickness readings ≥ 25 microns (1.0 mil)
- No more than 5% of readings on exposed surfaces shall be below 25 microns
For coil-coated applications, the requirements are slightly different:
- 80% of measurements must be ≥ 23 microns (0.9 mil) on exposed surfaces
- No more than 5% of readings shall be below 19 microns (0.75 mil)
Accelerated Testing Requirements
AAMA 2605 coatings must undergo rigorous laboratory testing to simulate long-term exposure to harsh conditions:
- Humidity Resistance: 4,000 hours of exposure with minimal blistering
- Cyclic Corrosion Testing: 2,000 hours of exposure to cyclic fog/dry testing with minimal corrosion
- Chemical Resistance: Must withstand exposure to muriatic acid, mortar, nitric acid, detergents, and window cleaners without significant degradation
Real-World Weathering Performance
Perhaps the most demanding aspect of AAMA 2605 is its outdoor weathering requirements:
AAMA 2605 coatings are designed to withstand severe environmental conditions for ten years, making them ideal for high-rise buildings and commercial applications. After ten years of exposure in South Florida (one of the harshest UV environments in North America), the coating must demonstrate:
- Color Retention: Color change must be no more than 5 Delta E units
- Chalk Resistance: Chalking rating no less than 8 for colors and 6 for whites
- Gloss Retention: Minimum of 50% gloss retention
- Erosion Resistance: Less than 10% coating loss
This ten-year real-world testing requirement is crucial—products with less than ten years of exposure cannot truly claim compliance with AAMA 2605.
Applications for AAMA 2605 Coatings
Due to their superior durability and performance characteristics, AAMA 2605 coatings are recommended for:
Monumental architectural projects and applications that require long-lasting aluminum surfaces, including:
- High-rise buildings and skyscrapers
- Landmark structures
- Coastal buildings exposed to salt spray
- Projects in extreme climate regions
- Applications where color and gloss retention are critical
- Buildings where maintenance access is difficult or costly
These superior coatings are commonly used on curtain walls, façades, windows, doors, and other architectural elements on monumental buildings, high-value residential properties, stadiums, malls, hospitals, and government buildings.
Benefits of Specifying AAMA 2605
Choosing AAMA 2605 coatings provides several significant advantages:
- Extended Lifespan: These coatings can last decades with minimal degradation.
- Reduced Maintenance Costs: The exceptional durability translates to lower long-term maintenance expenses.
- Superior Aesthetic Retention: Buildings maintain their intended appearance for much longer, preserving architectural integrity.
- Enhanced Weather Resistance: Better protection against UV radiation, moisture, and pollutants.
- Sustainability: Longer-lasting finishes reduce the need for refinishing and replacement, lowering the environmental impact.
Cost Considerations
It's important to note that AAMA 2605 coatings typically represent a higher initial investment compared to AAMA 2603 or 2604 coatings. However, when considering the total lifecycle cost of a building, this premium is often justified by the reduced maintenance requirements and extended service life.
Industry-Leading Products
Several manufacturers offer AAMA 2605-compliant coatings, including:
- 70% PVDF fluoropolymer liquid coatings
- FEVE-based fluoropolymer powder coatings
- Custom formulations for specialized applications
Beyond the Standard: How Premium Coatings Like Tnemec Fluoronar Exceed Requirements
While AAMA 2605 represents the highest industry standard for architectural coatings, it's important to understand that these requirements are minimum performance metrics. Premium coating systems like Tnemec's Fluoronar actually surpass these baseline requirements, offering even greater longevity and performance.
Performance Comparison: AAMA 2605 vs. Tnemec Fluoronar
Performance Criteria | AAMA 2605 Requirement | Tnemec Fluoronar Performance |
---|---|---|
UV Exposure Testing | 10 years South Florida exposure (≈2,800 MJ/m²) | EMMAQUA testing at 4,500 MJ/m² (equivalent to 16 years of South Florida exposure) |
Color Retention | Maximum 5 Delta E units change after 10 years | 0.32 Delta E Hunter (0.24 Delta E00) after accelerated testing equivalent to 16 years |
Gloss Retention | Minimum 50% after 10 years | 80% after accelerated testing equivalent to 16 years |
Film Thickness | 80% of measurements ≥30 microns (1.2 mil) | Typical 2.0-3.0 mils (50-75 microns) per coat |
Environmental Features | Not specified | Low VOC formulations available, contributes to LEED certification |
Special Performance | Not specified | Tolerates areas that are frequently wet or experience standing water and situational immersion |
The laboratory testing required by AAMA 2605 ensures a baseline level of performance, but advanced coatings like Fluoronar are subjected to even more rigorous testing protocols. EMMAQUA (Equatorial Mount for Mirrors for Acceleration with Water) testing, one of the most widely used outdoor accelerated weathering tests, allows manufacturers to simulate extended periods of UV exposure in a compressed timeframe.
The real-world performance of Fluoronar has been validated through extensive field studies. Some of the earliest applications from the early 2000s continue to demonstrate excellent color and gloss retention after 15+ years of service in harsh environments, confirming the laboratory test predictions.
When specifying high-performance coatings for prestigious architectural projects, looking beyond the minimum AAMA 2605 requirements to solutions that significantly exceed these standards can provide substantial long-term value through extended maintenance cycles and superior aesthetic retention.
Enhancing Specifications Beyond AAMA 2605 Minimum Requirements
While AAMA 2605 sets forth rigorous performance criteria, architects and specifiers should understand that this standard represents the minimum acceptable performance level for superior coatings, not the ultimate achievement. Forward-thinking specifiers are increasingly using AAMA 2605 as a baseline and then adding enhanced requirements to ensure even better long-term performance.
Strategies for Upgrading Specifications
- Specify Extended Testing Requirements
- Require products to undergo accelerated testing beyond the standard requirements (e.g., EMMAQUA testing equivalent to 15+ years of exposure rather than the standard 10 years)
- Include additional testing protocols not mandated by AAMA 2605, such as extended cyclic corrosion testing or abrasion resistance
- Establish More Stringent Performance Metrics
- Lower the allowable Delta E color change threshold (e.g., maximum 3 units instead of 5)
- Increase the required gloss retention percentage (e.g., minimum 70% after testing instead of 50%)
- Specify improved salt spray or humidity resistance (e.g., additional exposure hours)
- Include Real-World Performance Documentation
- Require manufacturers to provide case studies or documented evidence of actual field performance beyond 10 years
- Specify coatings with proven performance in similar environmental conditions to the project location
- Request coating formulations with a minimum of 5-10 years of market presence to ensure reliability
- Mandate Environmental and Sustainability Criteria
- Specify low or zero VOC formulations
- Require coatings that contribute to green building certification programs
- Include criteria for sustainable manufacturing practices
- Require Enhanced Application and Quality Control
- Specify certified applicators with experience applying high-performance coatings
- Mandate more stringent inspection protocols during application
- Require environmental controls during application that exceed the manufacturer's minimum recommendations
By viewing AAMA 2605 as a starting point rather than the ultimate goal, specifiers can significantly enhance the longevity and performance of architectural coatings. This approach may require a higher initial investment but can dramatically reduce life-cycle costs through extended maintenance intervals and preserved aesthetic qualities.
When drafting specifications, language such as "Coatings shall meet or exceed all requirements of AAMA 2605, plus the following enhanced criteria..." allows specifiers to build upon the established industry standard while ensuring superior performance for their specific project requirements.
Conclusion
For architects, specifiers, and building owners concerned with long-term performance and aesthetics, AAMA 2605 represents the highest standard in the industry for architectural coatings. While the initial investment may be higher than less durable alternatives, the superior performance characteristics—particularly in challenging environments—make these coatings the optimal choice for prestigious projects and applications where longevity and appearance retention are paramount.
When specifying coatings for your next architectural project, consider not just the color and initial appearance, but the long-term performance requirements and the value that superior coatings can provide over the building's lifecycle. AAMA 2605 coatings represent an investment in quality that pays dividends through decades of exceptional performance, and premium solutions like Tnemec Fluoronar that exceed these standards offer even greater returns through enhanced durability and aesthetic longevity.
If you have a project to discuss, please reach out to our team.
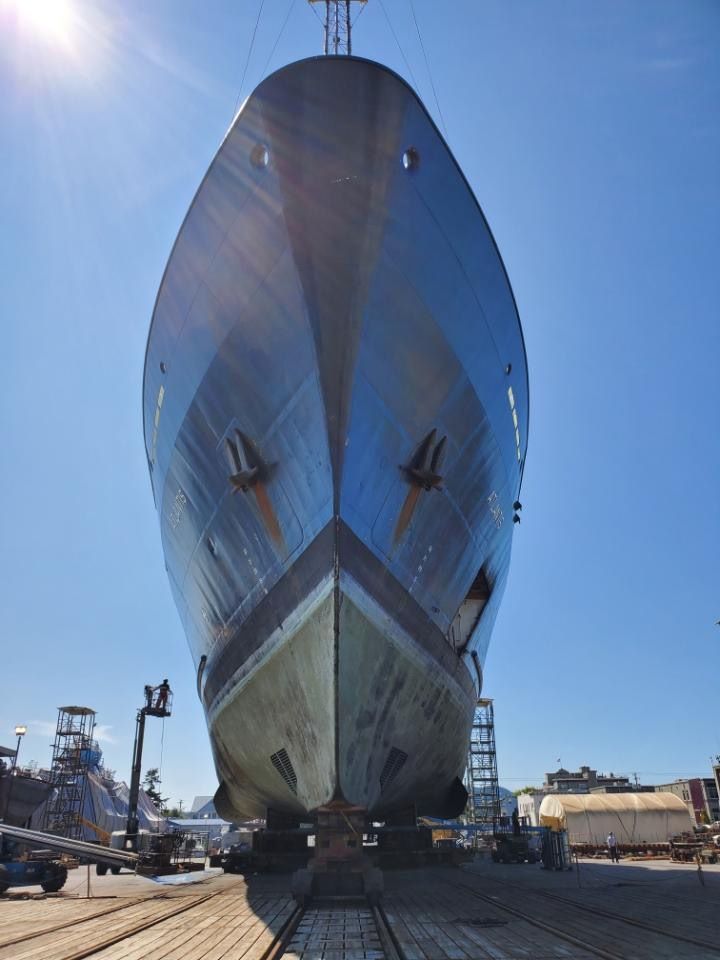
The Declining Performance of Marine Coatings
In the competitive world of marine coatings, a...
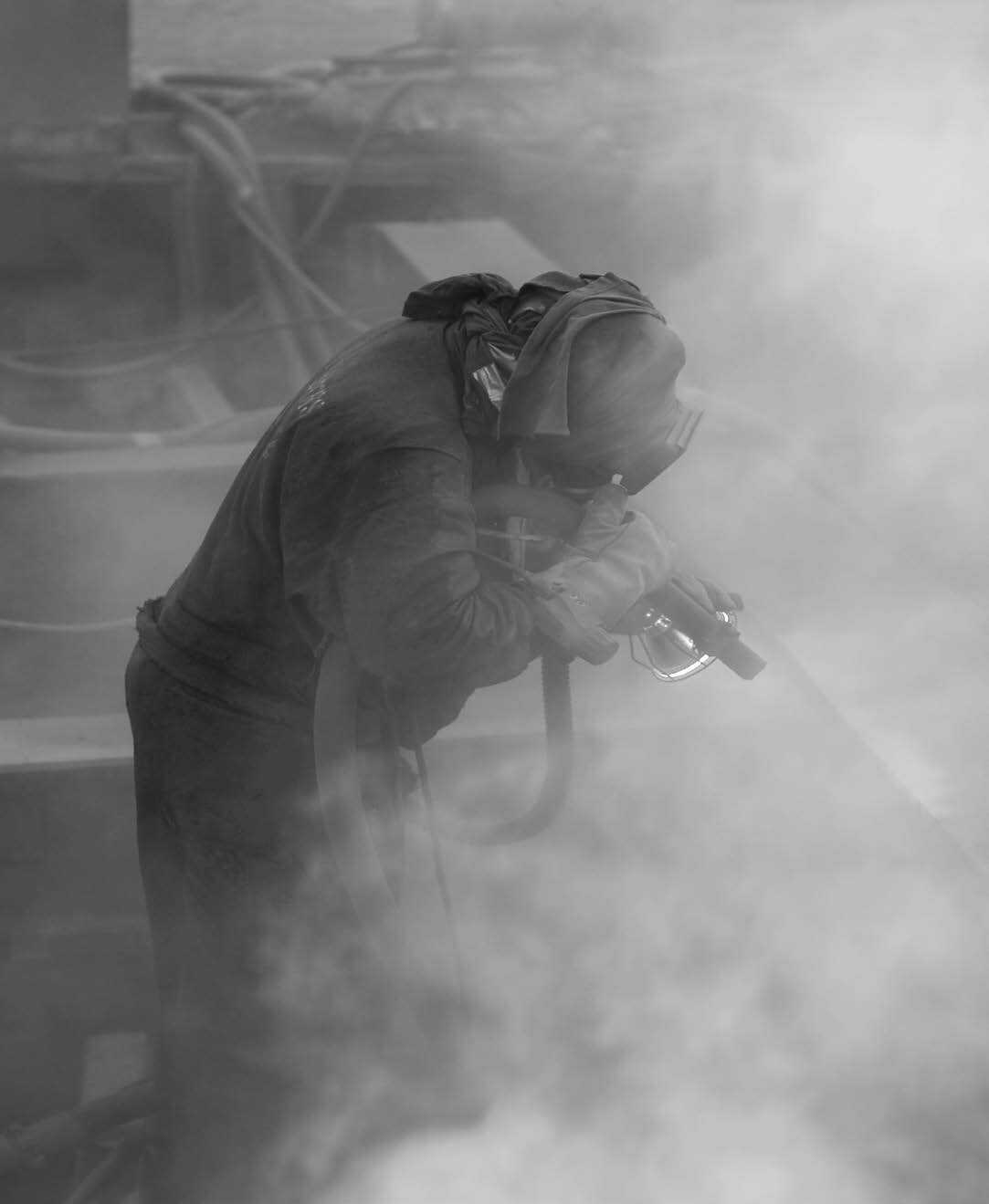
Choosing Surface Preparation Standards
The efficacy of any coating system begins with...
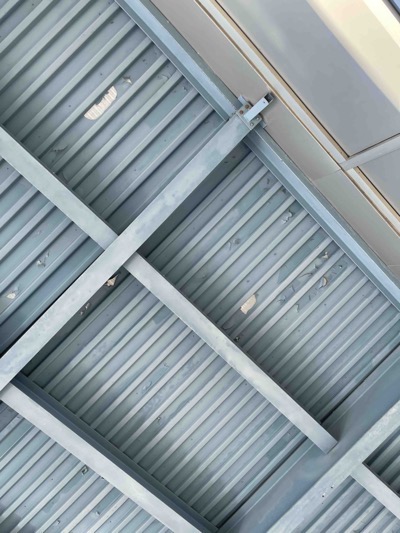
Can galvanized steel be coated?
What is Passivation on Galvanized Steel and Can...