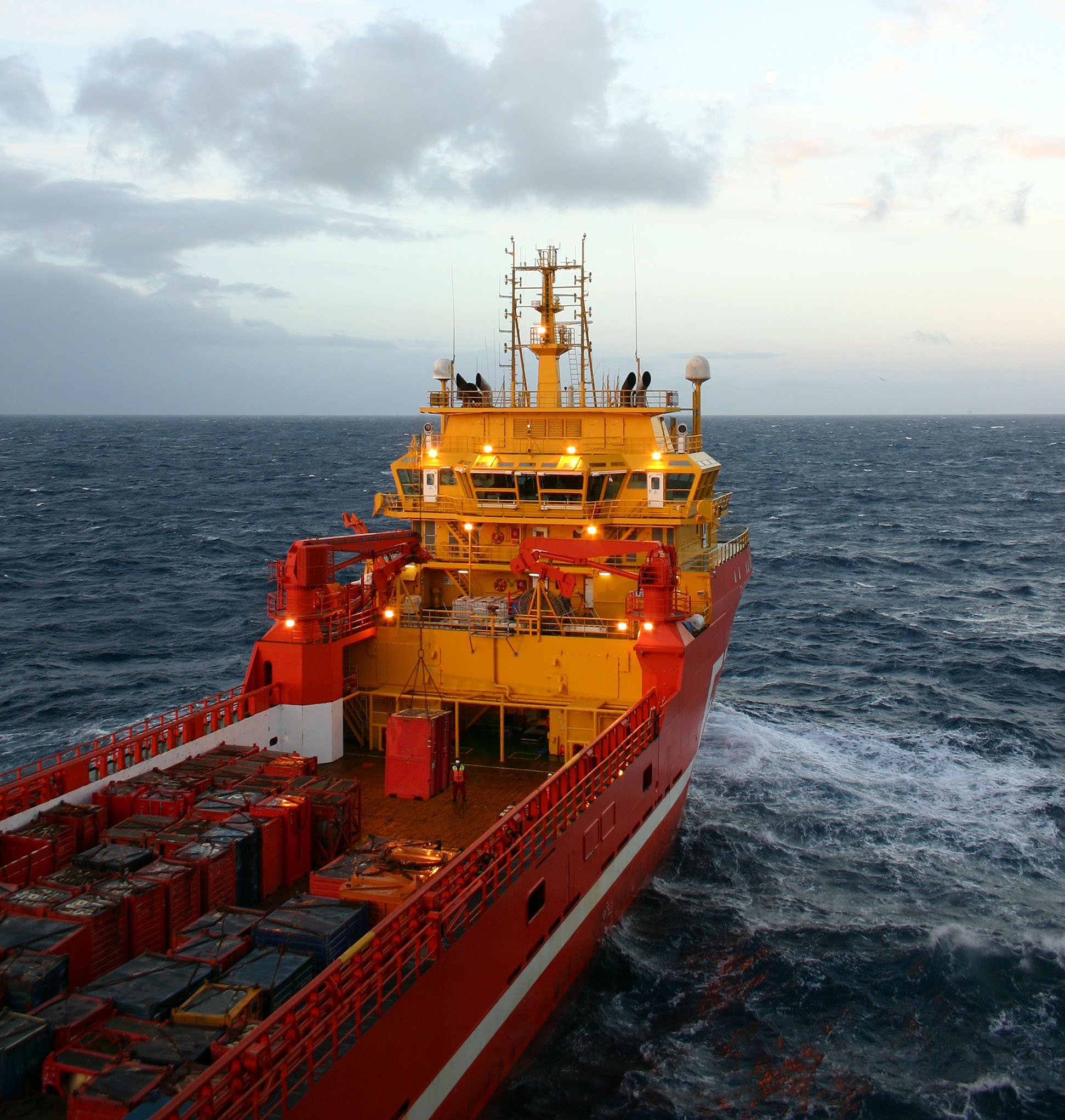
A Vessel Owner's Guide to Marine coating Performance
Shipyards often prioritize initial costs of coatings; as an owner, your perspective should focus on long-term performance and total cost of ownership.
- High Performance Coatings
Marine Coatings: A Vessel Owner's Guide to Performance Criteria
Introduction
When it comes to protecting your vessel, marine coatings are one of your most critical investments. While shipyards often prioritize initial costs, as an owner, your perspective should focus on long-term performance, durability, and total cost of ownership. This Q&A guide explores the key performance criteria that vessel owners should consider when selecting marine coating systems.
Q&A
Q: Why should I care about marine coating selection when the shipyard handles it?
A: While shipyards typically select and apply coatings, they're often incentivized to choose the lowest-cost options to stay competitive in their bids. As an owner, you'll live with these decisions for years after the shipyard work is complete. The right coating system can significantly reduce operational costs through fuel savings, extended dry-docking intervals, and decreased maintenance expenses. Taking control of coating specifications is one of the most impactful ways to protect your long-term investment.
Q: What are the most important performance criteria I should consider?
A: Key performance criteria include:
- Corrosion resistance
- Antifouling performance
- Abrasion resistance
- Chemical resistance
- UV and weather resistance
- Application properties (ease of application, cure time)
- Service life expectancy
- Environmental compliance
- Fuel efficiency impact
Each of these factors contributes to the total value proposition beyond just initial application cost.
Q: How do coatings affect my vessel's operational efficiency?
A: Marine coatings directly impact fuel consumption through hull smoothness and fouling resistance. Premium coating systems can maintain smoother surfaces over time, reducing drag and improving fuel efficiency by 5-10% compared to basic systems. For commercial vessels, this translates to hundreds of thousands in fuel savings over a standard dry-docking interval.
Q: What's the difference between antifouling and fouling-release coatings?
A: Antifouling coatings traditionally work by releasing biocides that prevent marine growth. Fouling-release coatings, by contrast, create a surface too slippery for marine organisms to firmly attach. While fouling-release systems typically have higher upfront costs, they often deliver superior long-term performance with better environmental profiles and potentially longer service intervals. Your operating profile (vessel speed, idle time, geographic regions) should determine which technology is optimal for your needs.
Q: How should I evaluate corrosion protection systems?
A: Look beyond just the thickness specifications. Premium systems utilize advanced barrier technologies, optimized zinc content in primers, and specialized tie-coats for superior adhesion between layers. Request accelerated testing data showing performance in salt spray tests, cyclic corrosion testing, and immersion testing. The best systems will provide documentation on expected service life in various environments and may offer warranties beyond standard terms.
Q: Are environmentally-compliant coatings as effective as traditional options?
A: Today's high-performance environmentally-compliant coatings often outperform older, more toxic formulations. Regulatory changes have driven significant innovation in the industry. The best systems now offer excellent performance while meeting global environmental standards. Focus on performance data rather than making assumptions based on environmental compliance. Many premium eco-friendly options deliver better long-term value than their conventional counterparts.
Q: How do I balance initial cost versus long-term performance?
A: Calculate the total cost of ownership by considering:
- Initial application cost
- Expected service life
- Predicted maintenance requirements
- Impact on fuel efficiency
- Potential extended dry-docking intervals
- Vessel downtime costs during recoating
Premium coating systems typically show return on investment within 1-3 years through operational savings, even with 30-50% higher initial costs.
Q: What documentation should I request when evaluating coating systems?
A: Request:
- Independent performance test results (not just manufacturer claims)
- Case studies from vessels with similar operating profiles
- Technical data sheets with specific performance metrics
- Warranty terms and conditions
- Track record of performance in your specific operating environments
- Technical service and support availability
This documentation provides objective criteria for comparing systems beyond price.
Q: How does coating selection impact my vessel's resale value?
A: Premium coating systems with documented maintenance history can significantly enhance resale value. Prospective buyers recognize the value of well-maintained coating systems with demonstrated performance. Quality coatings that have preserved the vessel's structural integrity and protected against corrosion will command higher values during inspection and valuation.
Q: What ASTM standards should I research and verify when evaluating marine coating systems?
A: Several critical ASTM standards can help you objectively evaluate coating performance:
- ASTM F941: Standard Practice for Inspection of Marine Surface Preparation and Coating Application. This standard ensures proper application procedures are followed during the coating process.
- ASTM D 4141, Method C: Color and Gloss Performance
- ASTM D 4585: Humidity, simulates long-term exposure to the elements
- ASTM B117: Salt Spray (Fog) exposes samples to a continuous spray of a neutral salt water solution in a controlled temperature and humidity environment simulating long-term marine and salt water exposure.
- ASTM D2794: Impact Resistance testing to ensure coatings can withstand physical impacts without failure.
- ASTM D5722: Accelerated Outdoor Weathering tests that simulate long-term exposure effects.
- ASTM D1735: Water Resistance testing to evaluate performance in high-humidity environments.
- ASTM D660-D662: Standards for evaluating coating deterioration like checking, cracking, and erosion.
- ASTM D5531: Standard for appearance consistency and quality.
Request test results according to these standards when evaluating coating systems to make truly objective comparisons between options.
Q: What topcoat provides the longest life cycle for corrosion resistance and color and gloss performance?
A: Fluoropolymer coatings provide the longest life cycle for both corrosion resistance and color/gloss performance in marine environments. These high-performance topcoats, which meet the stringent AAMA 2605 specification, offer exceptional UV resistance, chalk resistance, and color retention even after decades of exposure to harsh marine conditions.
Tnemec's Fluoronar is an excellent example of this technology. This advanced fluoropolymer coating system has demonstrated outstanding long-term performance in independent testing and real-world applications. According to performance data, Fluoronar meets or exceeds the weathering requirements of AAMA 2605, which is considered the highest standard for architectural coatings.
Performance Data: Tnemec Fluoronar
Performance Criteria | Test Method | Results |
---|---|---|
UV Exposure Resistance | EMMAQUA Testing | 80% gloss retention after 4,500 MJ/m² (equivalent to ~16 years in South Florida) |
Color Change | EMMAQUA Testing | Only 0.32 Delta EHunter after 4,500 MJ/m² exposure |
Weathering Performance | AAMA 2605 | Meets or exceeds 10-year South Florida exposure requirements |
Corrosion Resistance | ASTM B117 Salt Spray | Superior performance in accelerated testing |
Chemical Resistance | ASTM D1308 | Excellent resistance to acids, alkalis and solvents |
Impact Resistance | ASTM D2794 | Exceptional resistance to physical damage |
These coatings typically feature a complete system including proper surface preparation, a corrosion-resistant primer, and the fluoropolymer topcoat. While the initial cost is higher than conventional marine coatings, the extended service life (often 20+ years with minimal degradation) and significantly reduced maintenance requirements make fluoropolymer coatings the most cost-effective choice for vessel owners focused on long-term performance and protection.
Conclusion
As a vessel owner, taking an active role in coating system selection is crucial to protecting your investment and optimizing operational performance. By focusing on these key performance criteria rather than simply accepting the lowest-cost option, you can ensure your vessel remains well-protected, efficient, and valuable throughout its service life. Reach out to our Marine team for more information.
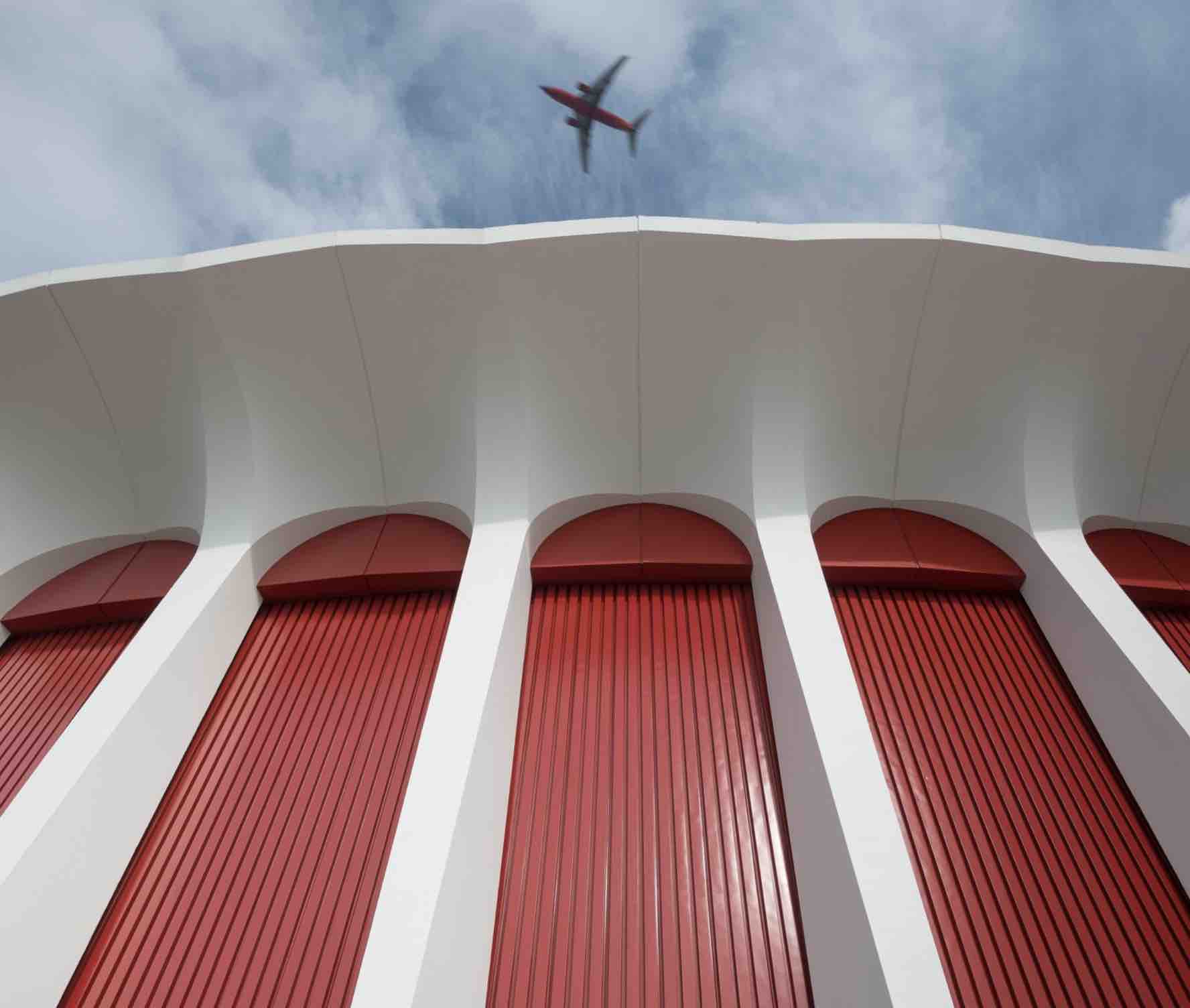
Why Performance and Formulation Matter in...
Why Performance and Formulation Matter in...
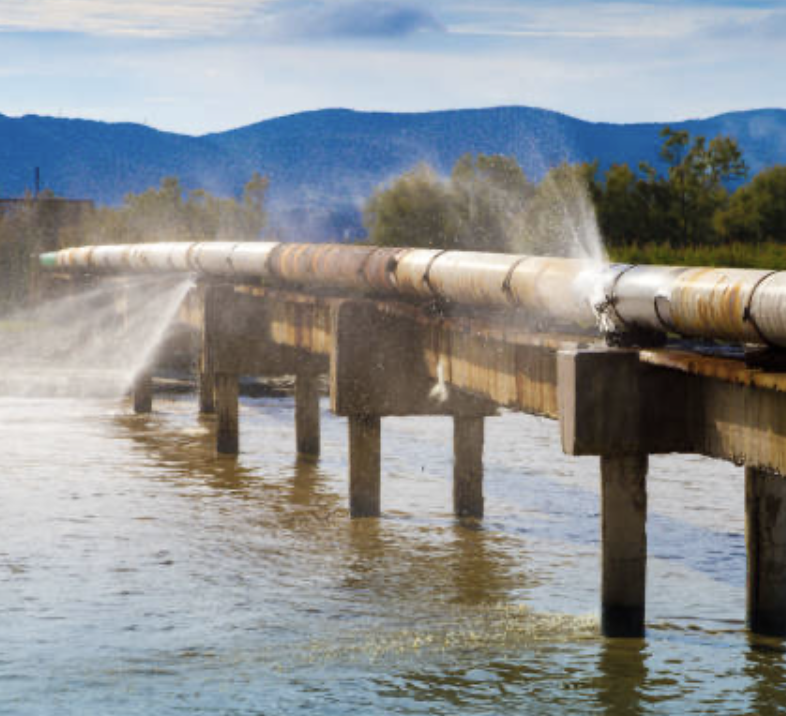
What Are The Benefits of Protective Coatings On...
Discover why coating carbon steel pipelines is...
