
UV Resistant Epoxy?
Owners and Designers have turned to epoxy based coatings for decades as an economical way to protect substrates from corrosion.
- High Performance Coatings
Owners and Designers have turned to epoxy based coatings for decades as an economical way to protect substrates from corrosion, provide chemical resistance, durability and improve facility aesthetics as a floor topping. Although epoxy provides all of these wonderful features, they are vulnerable to degradation from various light sources, specifically ultra-violet (UV) light. Once an epoxy polymer coating is cured, UV light and even fluorescent indoor lighting can cause the film to break down. The most noticeable change is with respect to color. When UV or fluorescent light hits the epoxy polymer, it degrades, causing ambering. Even the most crystal-clear epoxy resin will turn shades of yellow with time. For this reason, exterior and many architectural interiors applications commonly require the use of UV stable aliphatic polyurethane finishes to protect the underlying epoxy.
Even with this option available, often as a function of economy, many Owners and Designers will choose to forgo urethane finish coats. This practice has led to a rash of coating manufacturers claiming that their epoxy-based floor coatings are “UV Resistant or Stable.” This is just not true as evident by the photo below.
The epoxy coatings above, from various Manufacturers who market their products as floor toppings, were applied to the exact same blend of color flakes, placed on the Southern exterior of a Contractors shop in Northern Minnesota and exposed for 6 months during the Summer. Although none of the products are immune to the effects of UV light ,some products do better than others. Quality of resin, hardeners and additives used to engineer these materials all play a role on how well they will perform both aesthetically and functionally.
In a more extreme example of how quality in formulation matters, shown below are photographs of a contractor's garage floor who wanted to compare the long-term aesthetic retention of two leading suppliers of epoxy flooring.
After 5 years the difference can be seen in drastic fashion. The half of the floor finished with Tnemec Series 222 has maintained clarity while the half finished with “Brand X” has washed out, covering the red quartz.
As an Owner or Architectural Designer you often do not have the time or ability to subject finishes to long-term comparisons like this. So what do you do when selecting the longest lasting most sustainable finishes? The short answer is to turn to industry recognized consensus standards to benchmark product performance. ASTM, among other organizations, provide guidance for Manufacturers to perform accelerated testing. In a relatively short duration of time the information derived from these testing protocols provide a complete picture on how one product will perform compared to another. When considering lasting aesthetic performance in a decorative epoxy flooring topping, QUV Testing (ASTM D4587) with various light sources can be particularly helpful. This accelerated weathering test provides exposed samples for comparison to one another and/or unexposed control samples. Such comparisons may involve the measurements of Haze, Transmission, Yellowness Index, Color Change and/or physical properties such as Impact Strength.
Simple comparisons like this show that performance really does matter.
LET OUR KNOWLEDGE AND EXPERTISE HELP ENSURE YOUR NEXT PROJECT IS SUCCESSFUL
Check out our other resources on this topic:
Don't miss these project profiles:
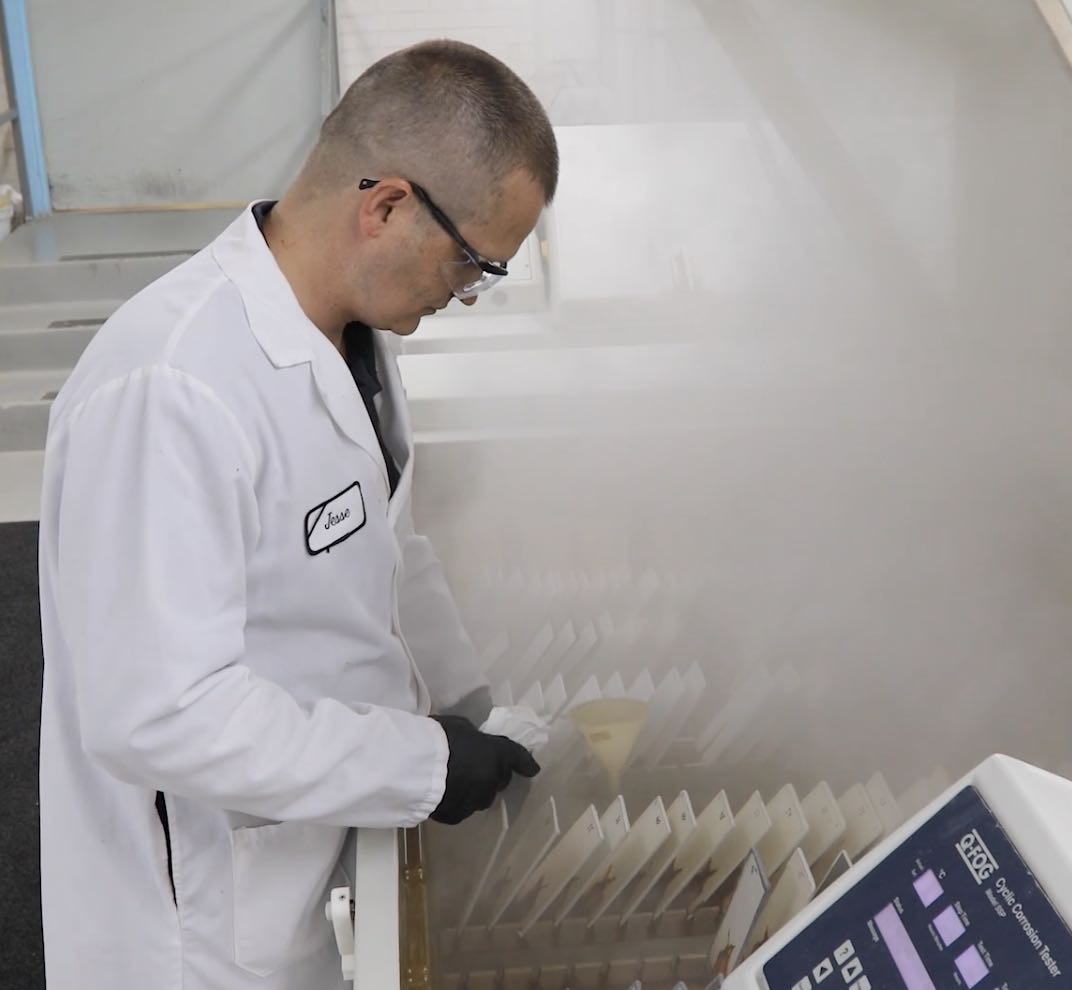
What is ASTM D4585 (Accelerated Weathering)...
ASTM D4585 is a standard practice developed by...
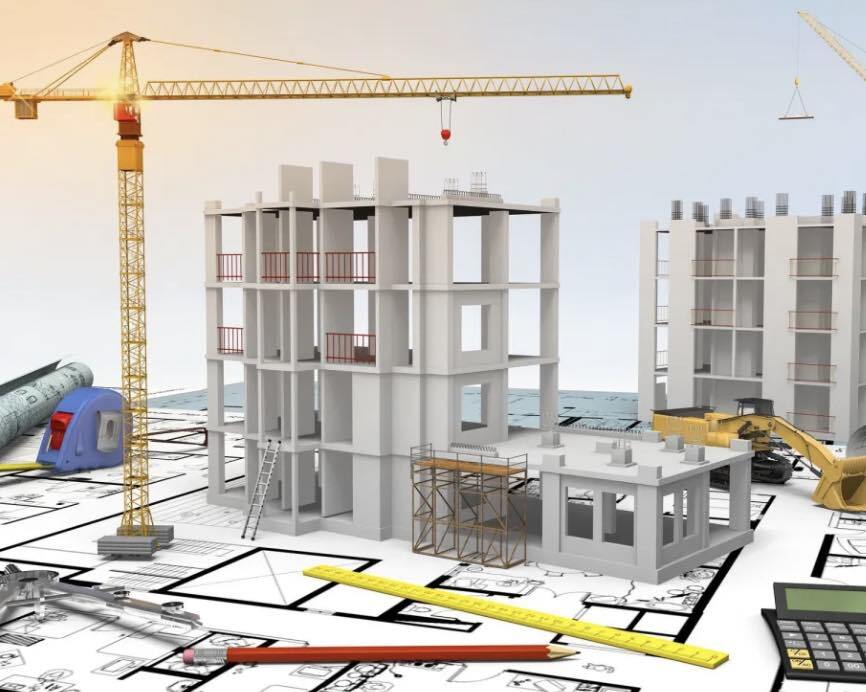
Why Specifying Floor Coating Projects Is Difficult
Specifying the right systems in the right places...
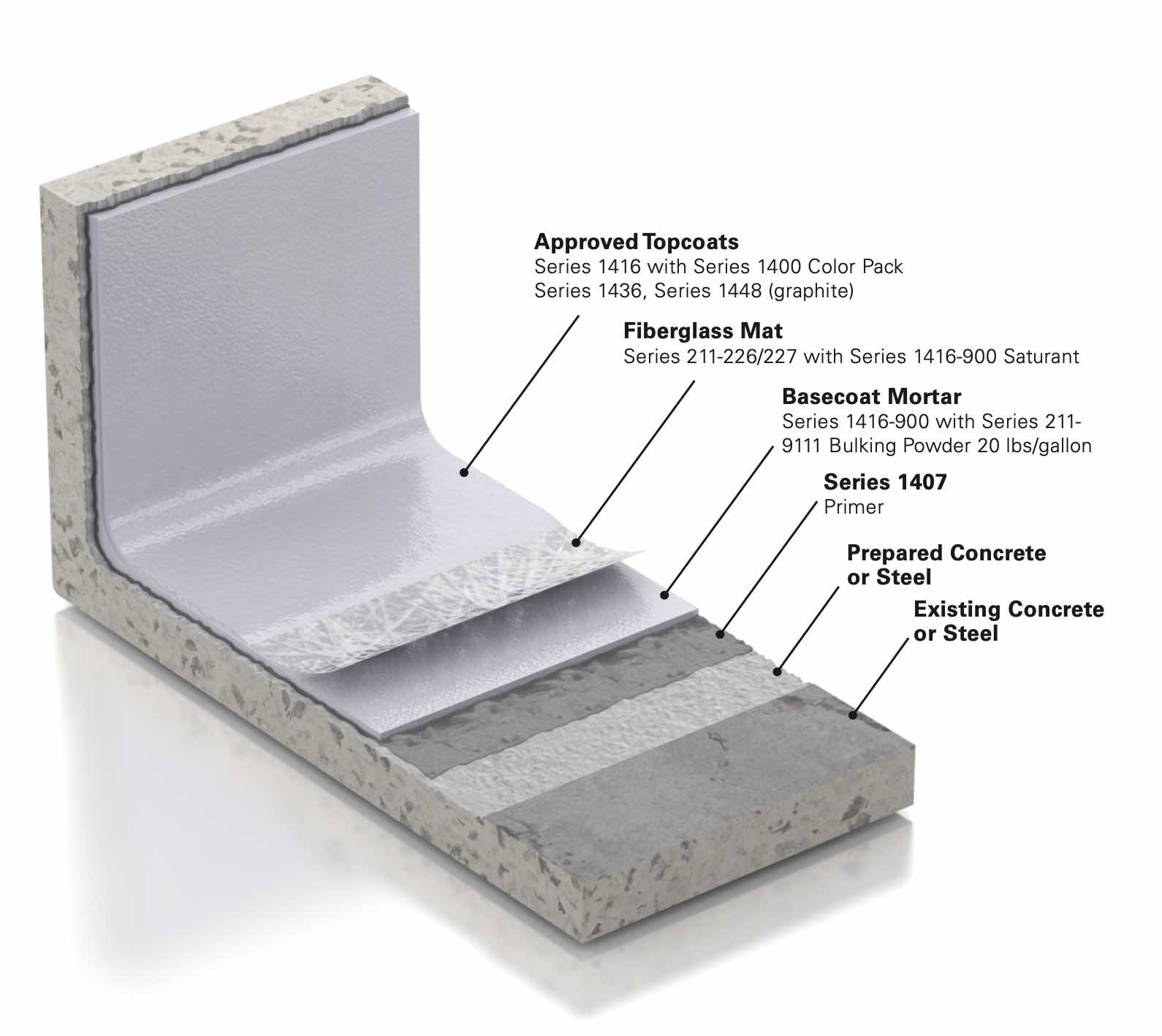
Vinyl Ester Systems (VE): The Solution for...
Vinyl Ester systems represent advanced polymer...