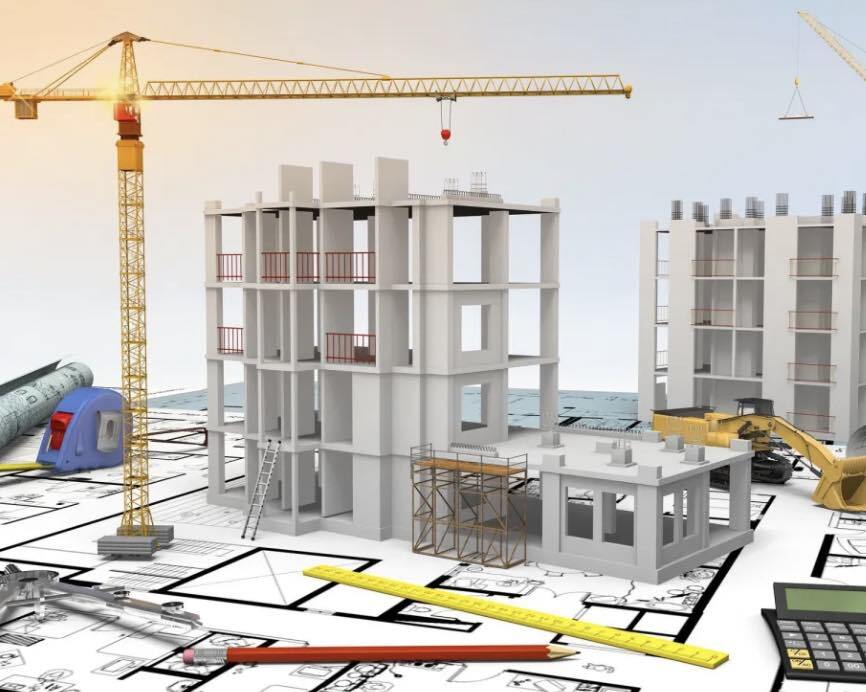
Why Specifying Floor Coating Projects Is Difficult
Specifying the right floor coating system for a project can be one of the most challenging aspects of building design and construction.
- High Performance Coatings
Specifying the right systems in the right places is not easy. This blog will help discuss what performance criteria is important for specific areas.
Why Specifying Floor Coating Projects is difficult: A Guide for Architects and Engineers
Introduction
Specifying the right floor coating system for a project can be one of the most challenging aspects of building design and construction. While floors may seem straightforward compared to complex mechanical systems or structural elements, getting the coating specification right involves navigating a maze of technical requirements, performance characteristics, and application considerations. This blog explores the unique challenges architects and engineers face when specifying floor coatings and offers practical guidance for making informed decisions.
The Complexity of Performance Requirements
One of the primary challenges in specifying floor coatings is defining the precise performance characteristics required for each specific environment. Industrial facilities, healthcare settings, commercial spaces, and institutional buildings all present unique demands:
- Chemical resistance: Different environments expose floors to various chemicals, from mild cleaning solutions to aggressive acids or solvents
- Abrasion resistance: Traffic patterns and equipment usage create varying degrees of wear
- Impact resistance: Dropped tools, equipment movement, or heavy machinery can damage inadequate coatings
- Thermal stability: Extreme temperatures in commercial kitchens or manufacturing facilities require specialized formulations
- Moisture transmission: Concrete substrate conditions significantly impact coating selection and performance
Tnemec's Series 222 Deco-Tread, for instance, offers exceptional chemical and abrasion resistance for industrial settings, while their Series 281 Tneme-Glaze provides a more decorative yet durable option for commercial spaces. The challenge lies in precisely matching these performance attributes to your project's specific needs.
Understanding Performance Metrics
When evaluating floor coating performance, architects and engineers must understand the standardized testing methods and metrics used in the industry:
Abrasion Resistance
Measured by the Taber Abrasion test (ASTM D4060), this metric indicates how well a coating withstands mechanical wear. The results are typically expressed as weight loss in milligrams after a specified number of cycles with standardized abrasive wheels. Lower numbers indicate better performance.
Chemical Resistance
Chemical resistance testing (ASTM D1308) measures a coating's ability to withstand exposure to specific chemicals without discoloration, softening, blistering, or loss of adhesion. Ratings typically range from no effect to significant failure.
Impact Resistance
The Gardner Impact Test (ASTM D2794) measures a coating's ability to resist rapid deformation. Results are reported in inch-pounds, with higher numbers indicating better resistance to impact damage.
Adhesion
Measured by the Pull-Off Adhesion Test (ASTM D4541), this indicates how well a coating bonds to the substrate. Results are expressed in pounds per square inch (psi), with higher numbers indicating stronger adhesion.
Slip Resistance
Coefficient of Friction (COF) testing (ASTM D2047) measures how slippery a floor is under various conditions. Higher numbers indicate better slip resistance.
Comparative Performance Analysis
Understanding how various floor coating systems compare can help architects and engineers make more informed decisions. The tables below provide a comparative analysis of select Tnemec floor coatings against competing products in key performance categories:
High-Performance Urethane Mortars Comparison
Performance Metric | Tnemec Series 245 Ultra-Tread S | Competitor A Urethane Mortar | Competitor B Cementitious Urethane |
---|---|---|---|
Compressive Strength | 8,300 psi | 7,250 psi | 6,800 psi |
Chemical Resistance (10% Lactic Acid) | No effect after 7 days | Slight softening after 7 days | Moderate softening after 7 days |
Abrasion Resistance (CS-17 wheel) | 18 mg loss (with 248) | 35 mg loss | 42 mg loss |
Impact Resistance | 240 in/lbs | 140 in/lbs | 125 in/lbs |
Temperature Resistance | -50°F to 250°F | -40°F to 220°F | -30°F to 200°F |
VOC Content | <0.1 lbs/gal | <0.2 lbs/gal | <0.3 lbs/gal |
Decorative Epoxy Systems Comparison
Performance Metric | Tnemec Series 222 Deco-Tread | Competitor C Decorative Epoxy | Competitor D Decorative System |
---|---|---|---|
UV Stability | Good stand alone, Excellent with urethane topcoat | Fair | Poor without special topcoat |
Abrasion Resistance (CS-17 wheel) | 65 mg loss | 96 mg loss | 120 mg loss |
Chemical Resistance (isopropyl alcohol) | No effect after 24 hours | Slight softening after 24 hours | Moderate softening after 24 hours |
Impact Resistance | 160 in/lbs | 120 in/lbs | 100 in/lbs |
Installation Time | 24-48 hours | 36-60 hours | 48-72 hours |
Customization Options | Unlimited colors | 20 standard colors | 12 standard colors |
Chemical-Resistant Coating Comparison
Performance Metric | Tnemec Series 282 Tneme-Glaze | Competitor E Novolac Epoxy | Competitor F Chemical-Resistant Epoxy |
---|---|---|---|
Chemical Resistance (98% Sulfuric Acid) | No effect after 72 hours | Slight discoloration after 72 hours | Moderate discoloration after 72 hours |
Chemical Resistance (50% Sodium Hydroxide) | No effect after 72 hours | No effect after 72 hours | Slight softening after 72 hours |
Abrasion Resistance (CS-17 wheel) | 130 mg loss | 162 mg loss | 128 mg loss |
Adhesion | 525 psi | 475 psi | 425 psi |
VOC Content | <0.4 lbs/gal | <0.7 lbs/gal | <1.0 lbs/gal |
Application Temperature Range | 40°F to 100°F | 50°F to 90°F | 55°F to 85°F |
Performance Trade-offs and Considerations
Beyond the raw numbers, architects and engineers must consider several practical factors when evaluating performance:
Service Life vs. Initial Cost
Higher-performing systems like Tnemec's Series 245 Ultra-Tread S generally command premium pricing but can deliver significantly longer service life under harsh conditions. For example, in a food processing facility exposed to organic acids and daily washdowns:
- A standard epoxy system might last 2-3 years before requiring replacement
- A mid-range urethane cement might last 5-7 years
- A premium system like Ultra-Tread S could extend to 10+ years
The lifecycle cost analysis often reveals that higher initial investment yields lower total cost of ownership when factoring in installation labor, downtime, and replacement costs.
Performance Balance
No single coating excels in all performance categories. Architects must prioritize which characteristics matter most for each specific application:
- Manufacturing facilities might prioritize chemical and impact resistance
- Commercial spaces might emphasize aesthetics and UV stability
- Healthcare facilities might focus on cleanability and bacteriostatic properties
Environmental Factors
Performance metrics are typically established under laboratory conditions, but real-world environments introduce variables that can significantly impact performance:
- Thermal cycling
- Cleaning chemical interactions
- Unexpected chemical exposures
- Maintenance practices
- Substrate movement
Substrate Considerations
Another significant hurdle is properly assessing and preparing the substrate. Floor coatings are only as good as the surface they're applied to:
- Moisture content: Excessive moisture vapor transmission can cause coating delamination
- Surface profile: The concrete's profile must be appropriate for the selected coating
- Contaminants: Oil, grease, or previous coatings can compromise adhesion
- Age and condition: New versus old concrete requires different approaches
Tnemec's approach includes comprehensive substrate testing protocols and preparatory products like their Series 201 Epoxoprime to address these variables, but specifiers must still understand and account for these factors in their specification documents.
Application Nuances
The application process itself introduces another layer of complexity:
- Environmental conditions: Temperature and humidity during application significantly impact curing and performance
- Time constraints: Project schedules may conflict with proper cure times
- Skilled labor requirements: Many high-performance systems require certified applicators
- Safety considerations: VOC levels and other safety factors must be addressed
Tnemec's Series 256 ExcellaThane, while offering excellent UV stability and chemical resistance, requires careful attention to application parameters to achieve optimal performance.
Balancing Performance and Budget
Perhaps the most challenging aspect is balancing performance requirements with budget constraints:
- Initial cost vs. lifecycle cost: Higher-performance systems often cost more upfront but often offer better value over time
- Maintenance requirements: Some systems require more frequent maintenance or specialized cleaning procedures
- Service life expectations: Different environments and use patterns affect coating longevity
- Downtime considerations: Future recoating or repairs impact facility operations
Tnemec offers solutions across the price-performance spectrum, from their economical Series 287 Enviro-Pox to premium Series 245 Ultra-Tread S, but specifiers must carefully assess which provides the best value for each specific application.
Navigating Complex Specifications
The specification documents themselves present challenges:
- Manufacturer-neutral requirements: Creating performance-based specs while ensuring quality
- Coordination with other trades: Interface with walls, drains, and equipment requires careful detailing
- Warranty considerations: Understanding what is and isn't covered
- Testing requirements: Defining appropriate quality control measures
- Substitution requests: Utilizing a basis of design, where substitutions MUST MEET design criteria and performance requirements.
Conclusion
Successfully specifying floor coating systems requires a deep understanding of material science, application techniques, and facility requirements. By thoroughly analyzing performance needs, substrate conditions, and budget constraints, architects and engineers can navigate these complexities to select systems that will perform reliably throughout their service life.
Working with knowledgeable coating consultants can help navigate these challenges through their technical support services, from specification assistance to on-site inspections. Their diverse product line allows specifiers to address virtually any flooring requirement with tested, proven solutions.
The most successful floor coating projects result from collaborative efforts between informed specifiers, experienced contractors, and supportive manufacturers working together to overcome these inherent complexities.
LET OUR KNOWLEDGE AND EXPERTISE HELP ENSURE YOUR NEXT PROJECT IS SUCCESSFUL
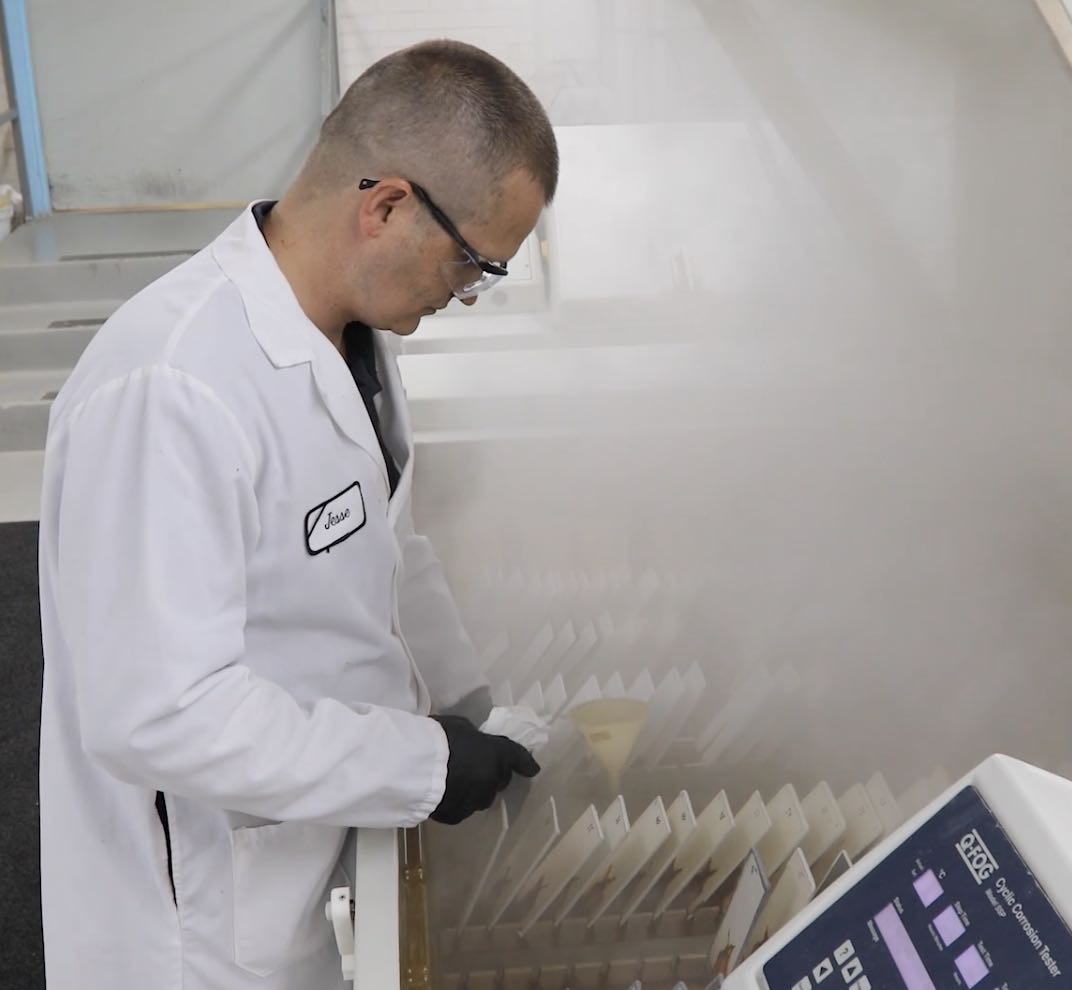
What is ASTM D4585 (Accelerated Weathering)...
ASTM D4585 is a standard practice developed by...
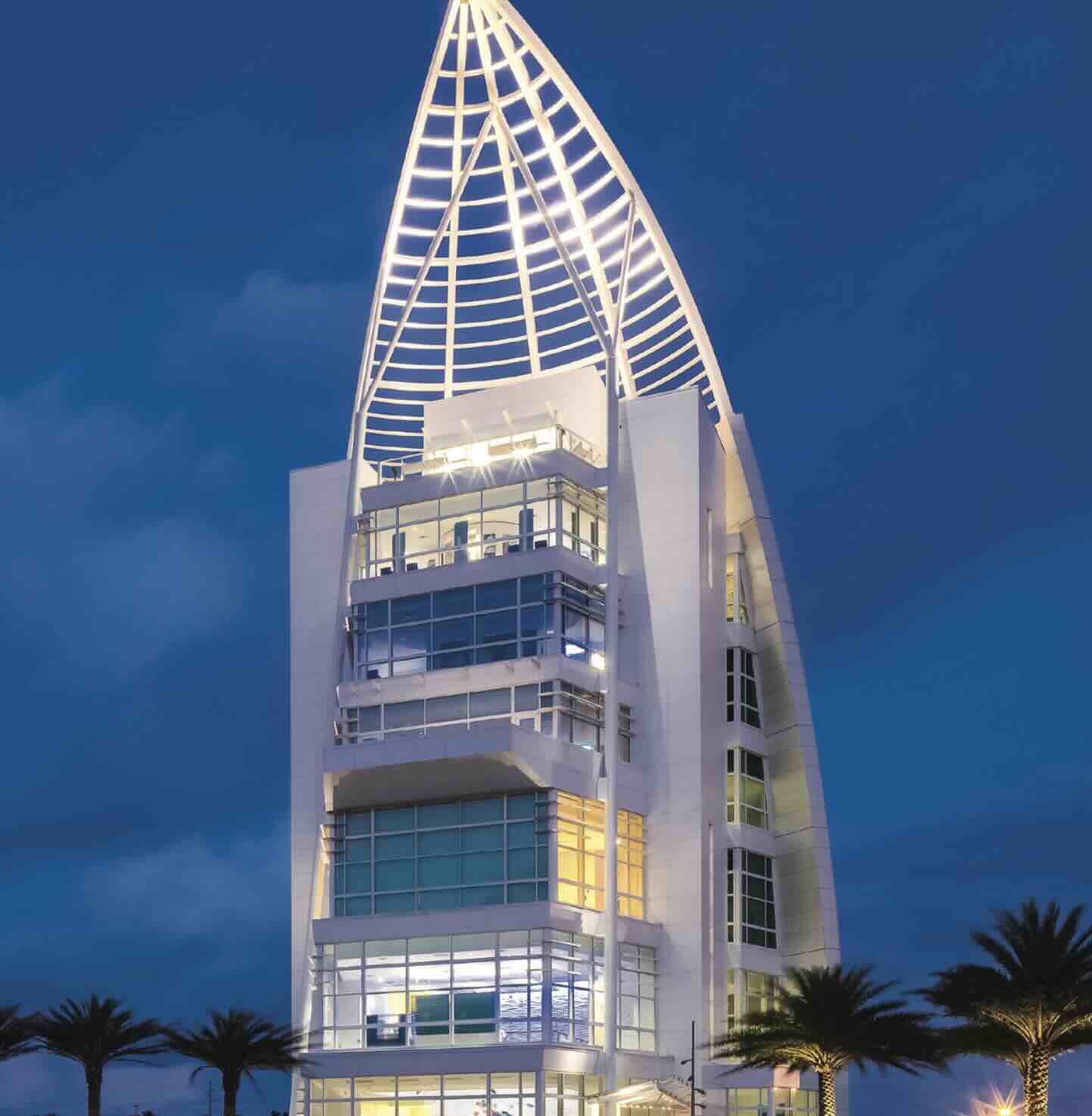
Decoding High Performance Coatings: A Comparative...
Explore the cutting-edge world of high...
