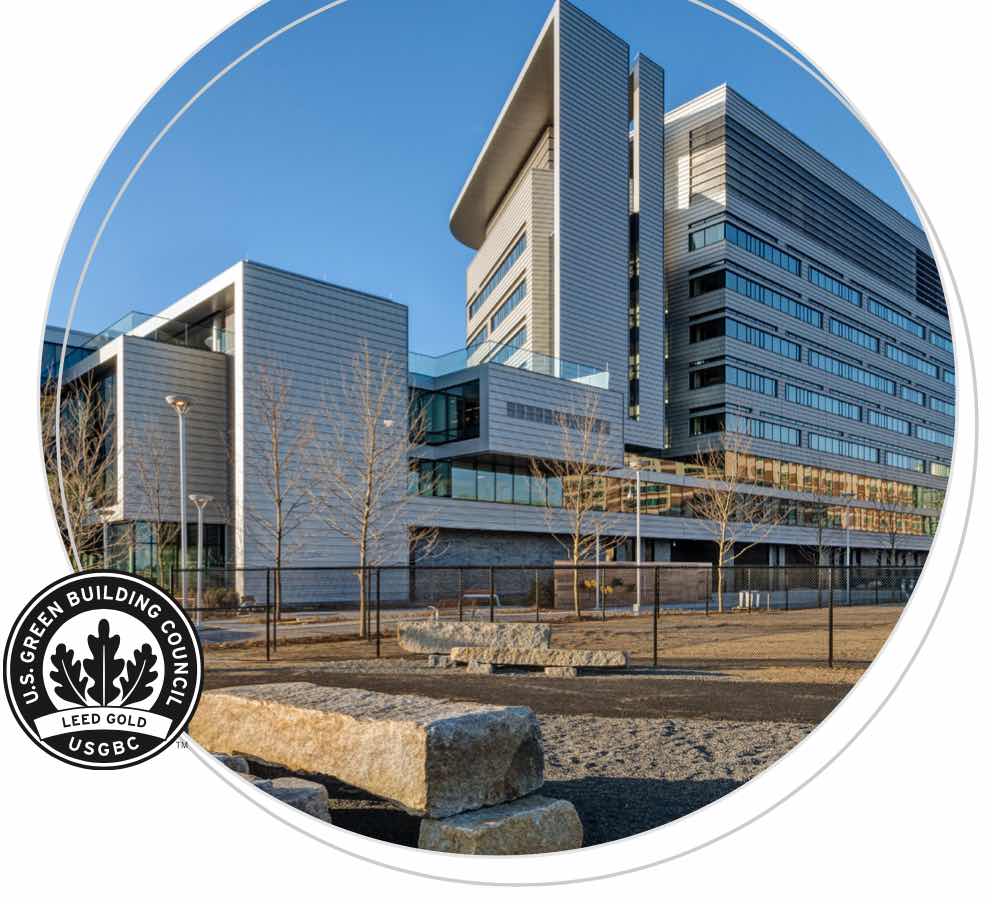
All Elastomeric wall coatings aren’t equal!
Elastomeric coatings are highly flexible and designed to be applied over vertical substrates, including brick, concrete block, stucco, and concrete.
- High Performance Coatings
All Elastomeric wall coatings aren’t equal!
Elastomeric Concrete Coatings Can Vary Widely, Across Performance Metrics
Elastomeric coatings represent a critical line of defense for masonry structures, offering thick, highly flexible protection designed specifically for vertical substrates including brick, concrete block, plaster, stucco, poured concrete, and stone. These specialized coatings solve a fundamental challenge in building protection: how to keep external moisture out while allowing interior moisture vapor to escape.
The Science Behind Effective Moisture Management
The permeability rate of quality elastomeric coatings creates a one-way moisture barrier that protects structures from both internal and external threats. Interior moisture vapor can pass through the coating film, preventing the dangerous pressure buildup that occurs when moisture becomes trapped within masonry walls. This pressure, especially when combined with recurring freeze-thaw cycles, creates cracks and fissures that substantially weaken substrates over time.
Simultaneously, the water-repellent coating surface remains impervious to external weather conditions, keeping rain, snow, and humidity from penetrating the structure. This dual-action protection is essential for long-term structural integrity.
Not All Elastomeric Coatings Are Created Equal
Understanding the different types of elastomeric coatings available is crucial before specifying protection for your structure. The market offers a wide range of options, each with distinct performance characteristics and cost implications.
Standard Water-Based Elastomeric Coatings are the most common and least expensive option. These generic coatings can be highly permeable—sometimes as high as 35 perms—but this high permeability comes at the cost of long-term protection and durability.
100% Acrylic Emulsion Elastomers represent a step up in quality. Manufactured by companies including Tnemec, these coatings use acrylic resins that form the protective film. However, these resins consist of long chains that simply lie on top of each other without cross-linking, which limits their moisture resistance and color retention over time.
Advanced Protection Through Innovative Chemistry
Tnemec's Series 156 Enviro-Crete represents a significant advancement in elastomeric coating technology through its unique styrenated acrylate formulation. Unlike conventional acrylic resins, this coating features a self-cross-linking micro-polymer system that delivers superior performance across multiple criteria.
Key Technical Advantages
Cross-Linked Film Structure: Each acrylate polymer in Enviro-Crete is silane-tipped at both ends. These reactive groups create cross-linking that results in a tighter, more durable film with exceptional moisture and UV resistance.
Lightweight Hollow Bead Technology: The coating incorporates inert hollow beads that weigh only one-eighth as much as conventional pigments. This innovation eliminates the need for additional anti-sag additives while achieving excellent film build per coat. The beads provide dual benefits: they reflect light twice as it passes through (improving UV resistance and hiding power), and unlike regular pigments, they don't absorb water.
Superior Penetration: The micro-polymer size allows better penetration into substrate pores and cracks, creating stronger adhesion and more complete protection.
Comprehensive Performance: Enviro-Crete combines elasticity with adhesion, toughness, UV resistance, and moisture vapor management—a combination that sets it apart from other coating options.
Antimicrobial Properties: The acrylate chemistry naturally resists mold and mildew growth per ASTM D3273, keeping the coating cleaner throughout its service life.
The True Cost of Protection
While Enviro-Crete carries a higher upfront cost per gallon due to its advanced raw materials and manufacturing processes, this initial investment delivers substantially lower life-cycle costs. The combination of superior durability, reduced maintenance requirements, and extended service life makes it a cost-effective choice for long-term structural protection.
When specifying elastomeric coatings, consider not just the initial price but the total cost of ownership. The most expensive coating failures are often those that result from choosing the least expensive product upfront.
LET OUR KNOWLEDGE AND EXPERTISE HELP ENSURE YOUR NEXT PROJECT IS SUCCESSFUL
Check out these other Resources:
Don't miss these Project Profiles:

Spalling Concrete and How to Fix It
Concrete Spalling: Understanding, Preparing, and...
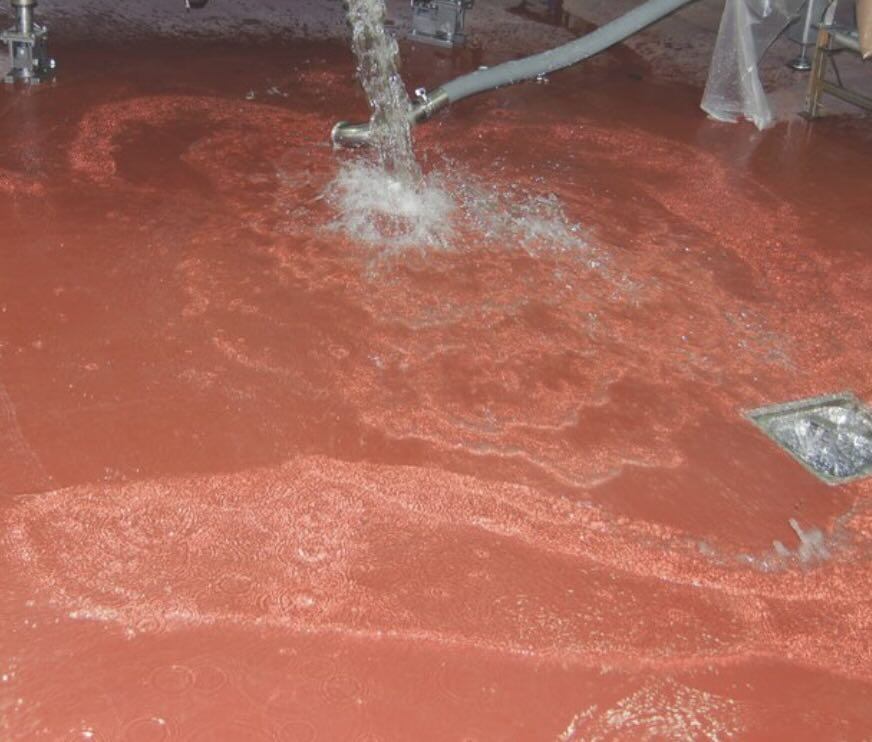
Shielding Your Concrete Floors: Essential...
Discover how the right coatings can safeguard...
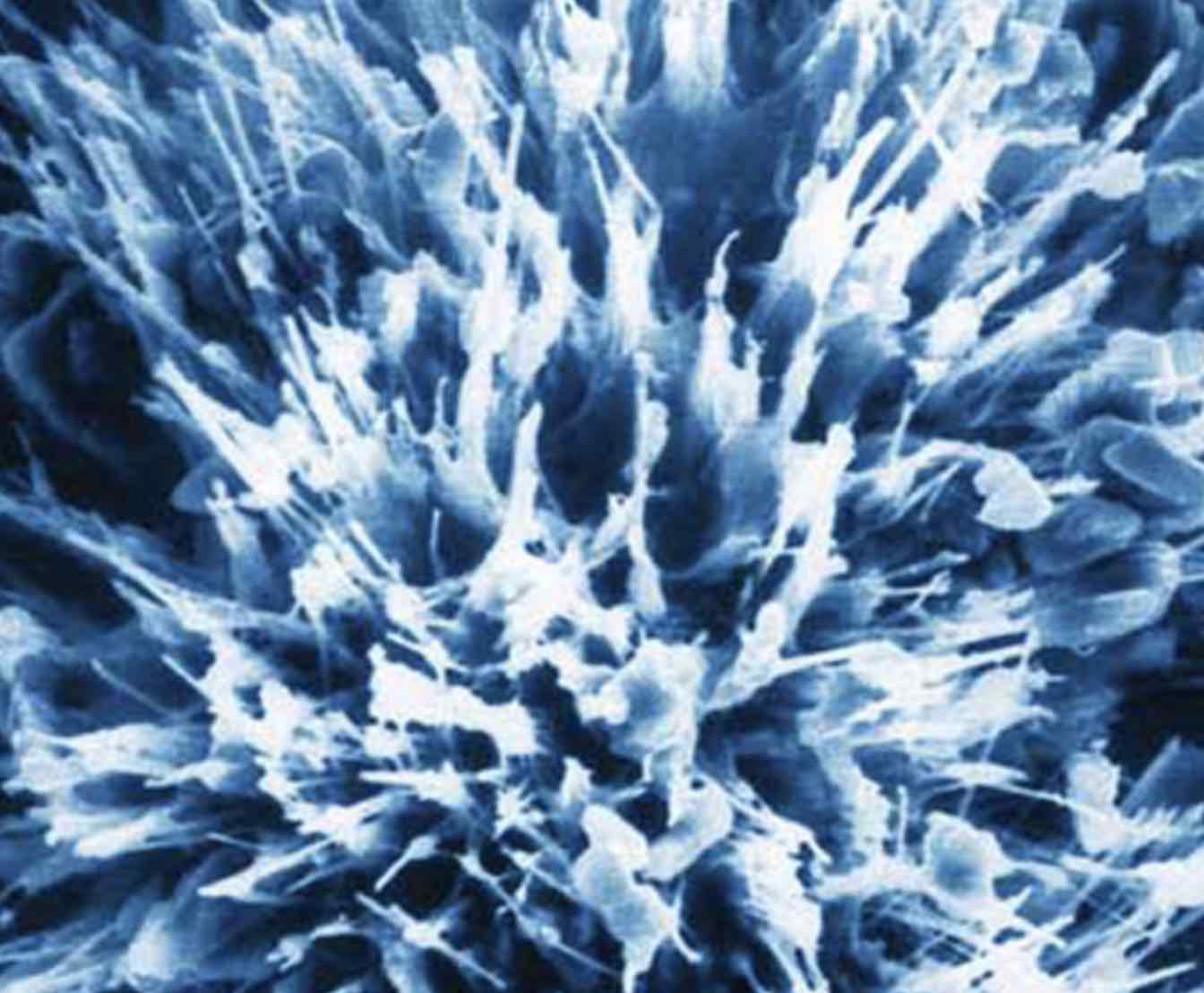
The Use of Crystalline Waterproofing Additives in...
The Use of Crystalline Waterproofing Additives...