
What an Engineer should know before spec'ing High Performance Coatings
There are many factors that should be considered by an Engineer before specifying high-performance coatings.
- High Performance Coatings
There are many factors that should be considered by an Engineer before specifying high-performance coatings, including:
1. Surface Requirements: One should understand the specific requirements of the surface or substrate that needs to be coated. This includes its composition, condition, preparation needs, and any environmental or chemical exposures it may encounter.
2. Performance Needs: Determine the desired performance characteristics of the coating, such as corrosion resistance, abrasion resistance, chemical resistance, UV resistance, thermal stability, or non-stick properties. Understanding the expected performance requirements will help in selecting the appropriate coating formulation. These performance criteria are specifiable through ASTM's. For example, ASTM B117 (Salt Fog) is a great way to specify a minimum level of corrosion resistance. ASTM D4547 (QUV) can represent expectations for longevity of color and gloss protection. ASTM D1653 (Permeability) can set the expectation for the minimum allowable permeability. There are dozens more ASTM's that can help set the minimum performance requirements for products that will be approved for the project.
3. Environmental Factors: Consider the operating environment in which the coated surface will be exposed. Factors like temperature fluctuations, humidity, chemical exposure, UV radiation, or outdoor weathering can impact coating performance. Select a coating that can withstand the specific environmental conditions.
4. Industry Standards and Regulations: Different industries may have specific standards, regulations, or certifications that coatings need to meet. Ensure the chosen coating complies with applicable industry requirements, such as aerospace, automotive, marine, or infrastructure standards.
5. Application Method: Understand the practical aspects of coating application, such as the available equipment, application techniques, and expertise required. Consider factors like curing time, drying conditions, surface preparation requirements, and compatibility with existing coating systems if applicable.
6. Maintenance and Durability: Evaluate the expected maintenance requirements and durability of the coating. Consider the anticipated lifespan of the coating, ease of maintenance, and potential costs associated with recoating or touch-ups over time.
7. Cost and Budget: Consider the budgetary constraints for the project. High-performance coatings may have higher upfront costs compared to regular coatings, but they can provide long-term cost savings through improved performance, extended lifespan, and reduced maintenance needs. Balance the performance requirements with the available budget.
8. Supplier and Technical Support: Engage with reputable coating suppliers who can provide technical support, guidance, and documentation for the selected high-performance coatings. Ensure the supplier has a track record of delivering quality products and has a reliable support system in place.
By considering these factors, engineers can make informed decisions when specifying high-performance coatings that best meet the requirements of their projects and deliver the desired performance and protection. For help considering many of the above-referenced requirements, reach out to a High Performance Coatings consultant for a free consultation.
Check out these additional resources on wastewater and water treatment coatings
Severe Wastewater Testing for Coatings
Ductile Iron Surface Preparation
Coatings for Wastewater Facilities
Don't miss these wastewater and water treatment coating project profiles
Howard Berry Water Treatment Plant
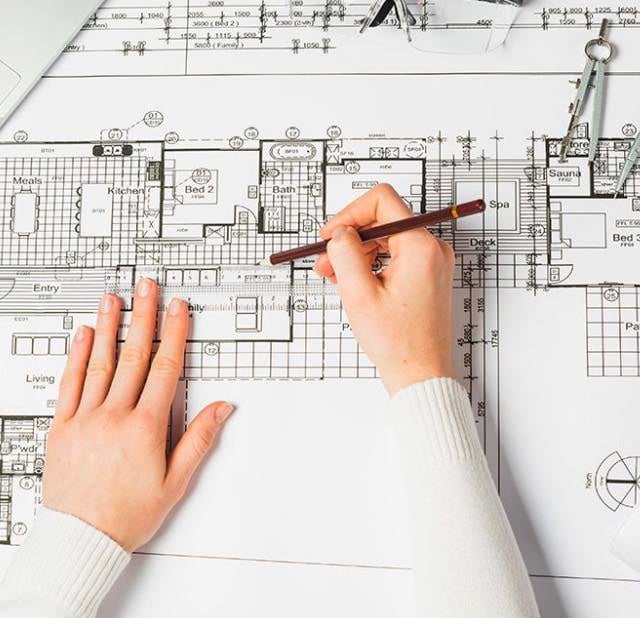
What Considerations Should an Architect Make...
Before specifying a high-performance coating,...
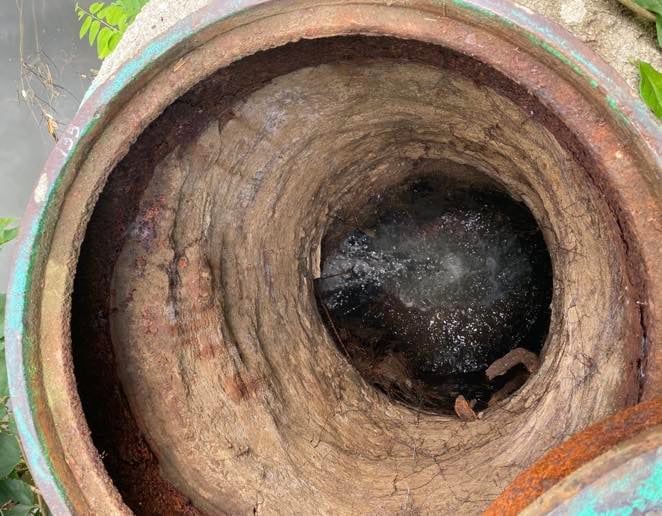
Comparing Structural Epoxy to Other Repair...
Structural epoxy and cementitious repair...
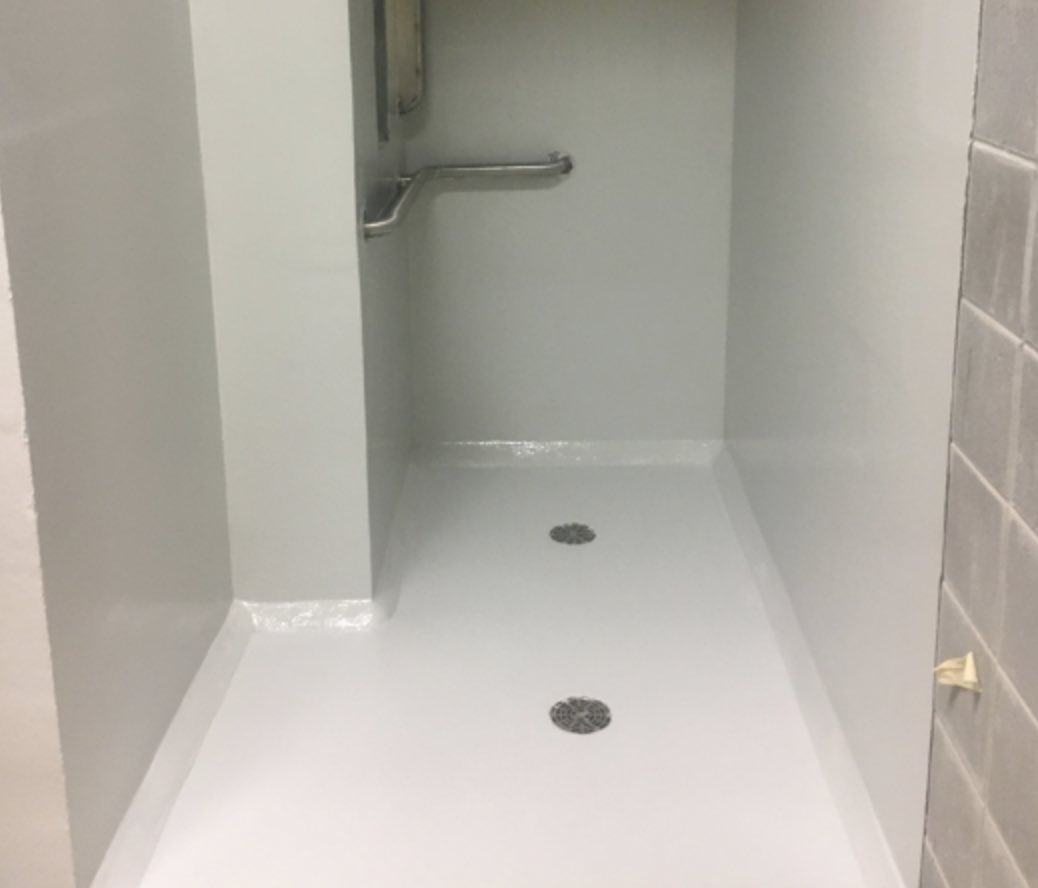
Where to use a Fiberglass Reinforced Wall System
Epoxy mat layup wall systems, like Tnemec...